Updates:
- 2025/04/21: added 2nd slicer link to new S4 Slicer (reimplementing S^3 slicer)
- 2025/03/11: added link to github repo of the radial slicer
- 2024/12/03: starting write-up, and published it
Introduction
Joshua Bird announced his 4-axis Polar CoreXB Printer December 1st 2024 on Reddit and YouTube:
Beside the hardware, he also implemented the required software and released it on github as “Radial Non-Planar Slicer” – an impressive undertake and success in one go.
4-Axis Linear Head(XZ), Rotational Head(Y)Bed(Z)
Even though I was impressed by the 4-axis RTN by ZHAW I wrote about, I abandoned the idea of 4-axis setup, as I considered it too limiting. Joshua’s approach to use a Z rotating bed, and the nozzle rotating ~180° or -90°.. +90° in Y-axis implements a polar (coordinate) printer.
He has a fixed Z-rotational center on the bed, and variable head Y-rotation in X. By keeping the Y-rotation (B) at 0° (vertical), the printer can print Z-planar cylindrical as well.
It can print XY Z-planar like a 3-axis 3D printer by mapping the XY coordinates into radial/cylindrical coordinates as well, so let’s summarize quickly what can be done:
- polar coordinates, spherical slices
- cylindrical coordinates, Z-planar cylindrical slices (fixed Y/B axis at 0°/vertical)
- cartesian coordinates, mapping XY into radial/circular coordinates and fixed Y/B axis at 0°/vertical as well
So, this setup is quite powerful – and much better than the 4-axis RTN and also my 5-axis PAX setup, where the cabling and PTFE pipe for the filament prevent 360° Z-rotation / C-axis. Because Joshua’s has the Z/C-rotation on the bed, it’s fully continuous (or use a slip-ring to deliver power for a heated bed).
Dual Z Fixed X-Axis: Bad Idea?
Joshua’s original design is a cantilever, a single XZ beam with the Y/B rotation on the head. For a more large scale setup we require the X-rail to be attached on two Z rails, like the traditional Prusa-Mendel setup. In order to keep the -90°..+90° Y/B rotation of the head/nozzle, we need to position the rotation center a bit below the X-axis – but . . . this will prevent the nozzle to rotate Y/B to -90° or +90° as the gantry likely will crash with the already printed piece. So, it’s rather a bad idea to do so. As a result, we end up with a limited build volume, as the cantilever will tilt with further extending the X-axis.
Core XB: Combining Linear X with Rotational B (Y-Axis)
That is a very clever setup Joshua did, by having the linear X-axis combined with the rotational B-axis (Y-rotation) which he calls “Core XΘ” (Core X-Theta).
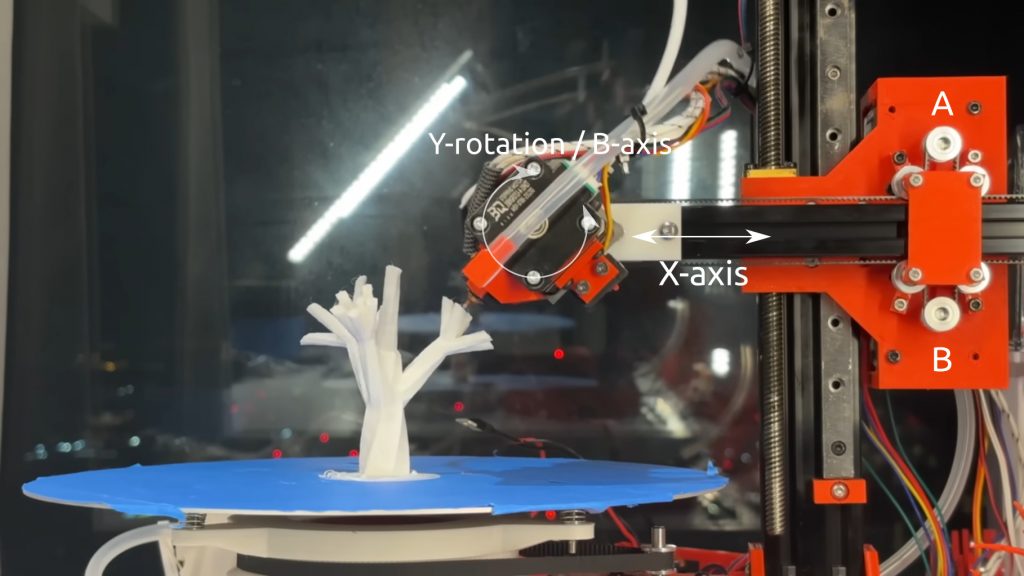
Non-Planar Polar Slicer
Joshua did also code a mixed non-planar slicer which combines multiple schemas as shown in the video:
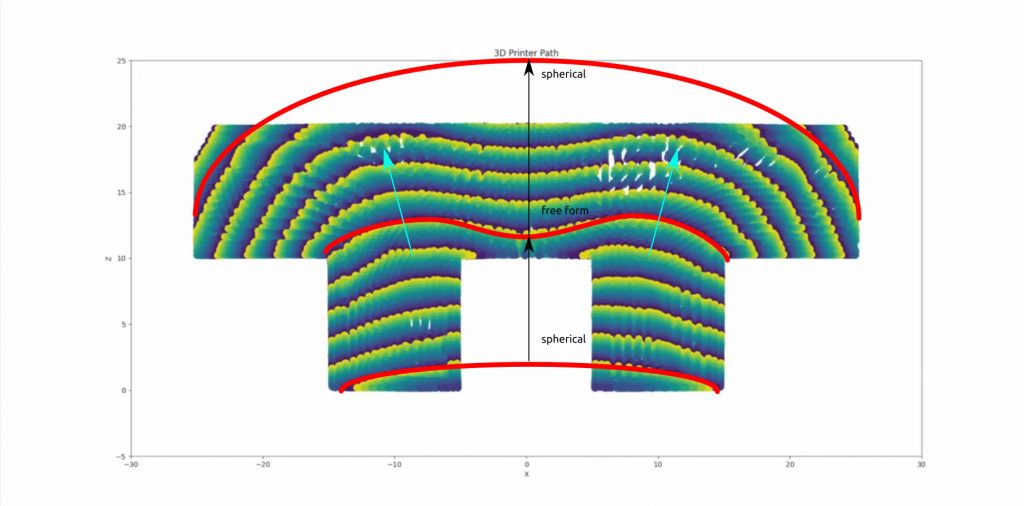
continuous printing without overhangs
That is the most tricky part, as polar (flexible tilt) and conical (fixed tilt) slicing may appear sophisticated, but it has its even more expanding challenges as Joshua mentions in his video, and obviously he developed a mixing strategy/schema slicing procedure to slice according the given requirements of printing continuous without supports – as when slicing non-planar, pieces otherwise easy to slice & print, suddenly have overhangs or are non-continuous or not connected anymore.
The S^3 DeformFDM Slicer from Manchester Uni (Tianyu Zhang, Tao Liu, Charlie C.L. Wang) has provided a solution to combine Support Free (SF), Strength Reinforcement (SR) and Surface Quality (SQ) under one umbrella of consideration and optimize all three requirements using quaterions per sample. I tried to adapt that solution but struggled to even build the solution from the sources back in 2022.
Update 2025/04/20: Joshua released his reimplementation of S^3 DeformFDM Slicer as S4 Slicer:
Impressive Step Forward
Joshua Bird has “single-handedly pushing the 3DP community forward.” according a YT-comment, and I whole-heartly agree, not only did he thought out of the box with the Core XB setup, but resolved multiple hardware and software challenges – impressive.
References
- Polar Core XB 3D Printer (original YouTube video aka “I Built a 4 Axis 3D Printer Unlike Anything You’ve Seen”)
- Radial Non-Planar Slicer (basic NP slicer)
- S4 Slicer (sophisticated NP slicer)
- Hackaday: Unique 3D Printer Has A Print Head With A Twist (2024/12/02)
- Hackaday: Non-planar Slicing Is For The Birds (2024/04/20)