Updates:
- 2024/11/26: published
- 2024/11/23: finishing up, ready for publication
- 2024/11/21: starting write-up
Introduction
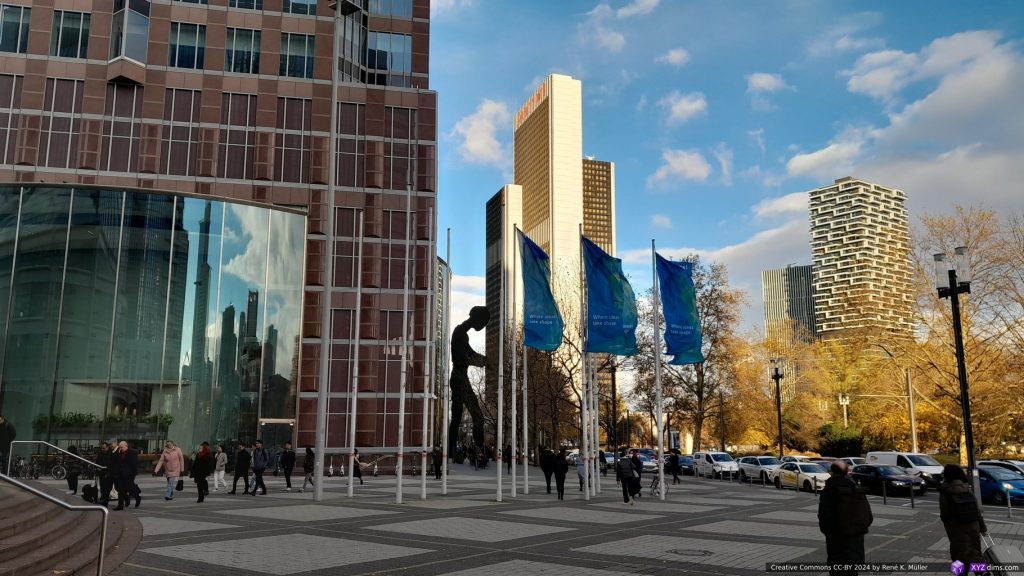
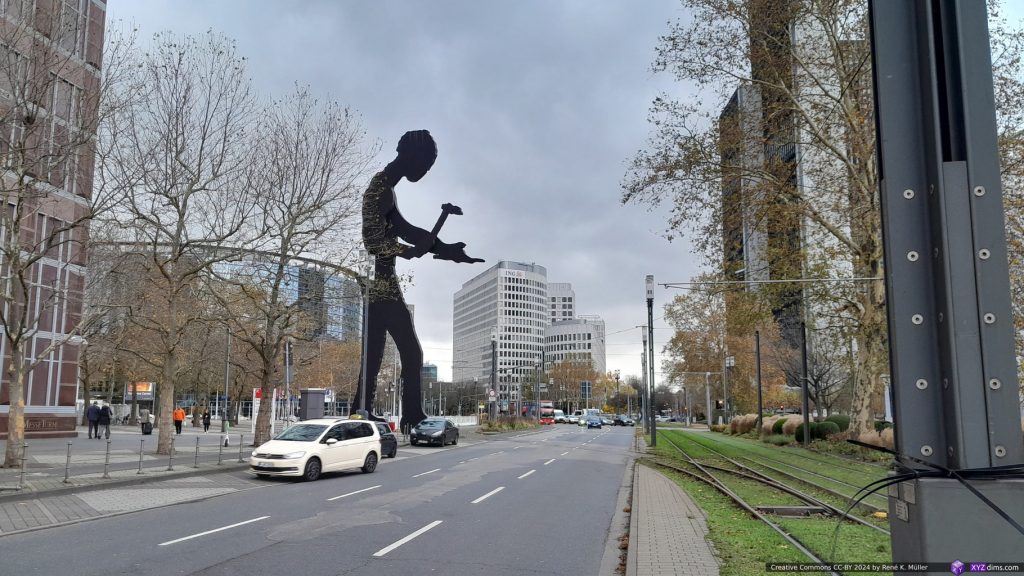
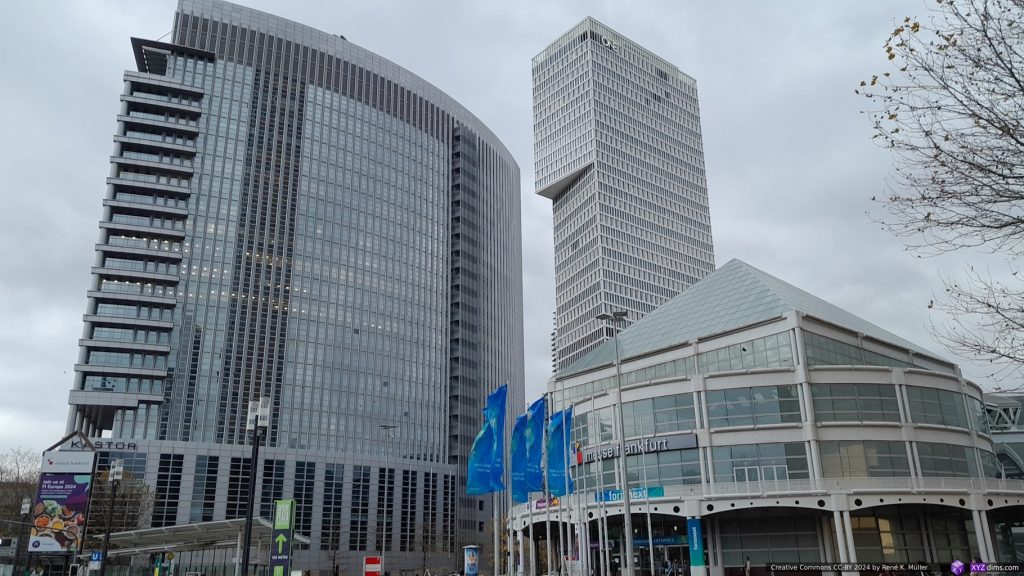
Once again in fall (November 19-22, 2024) Formnext expo opened its doors, and I attended for 2 1/2 days – here my brief write-up and reflection of my experience.
Formlabs
Formlabs made an interesting move: it abandoned the SLA (laser-based) to MSLA (UV light & LCD masking) resin printing with their Form 4 series (Form 4 & Form 4L), so I briefly visited their booth:
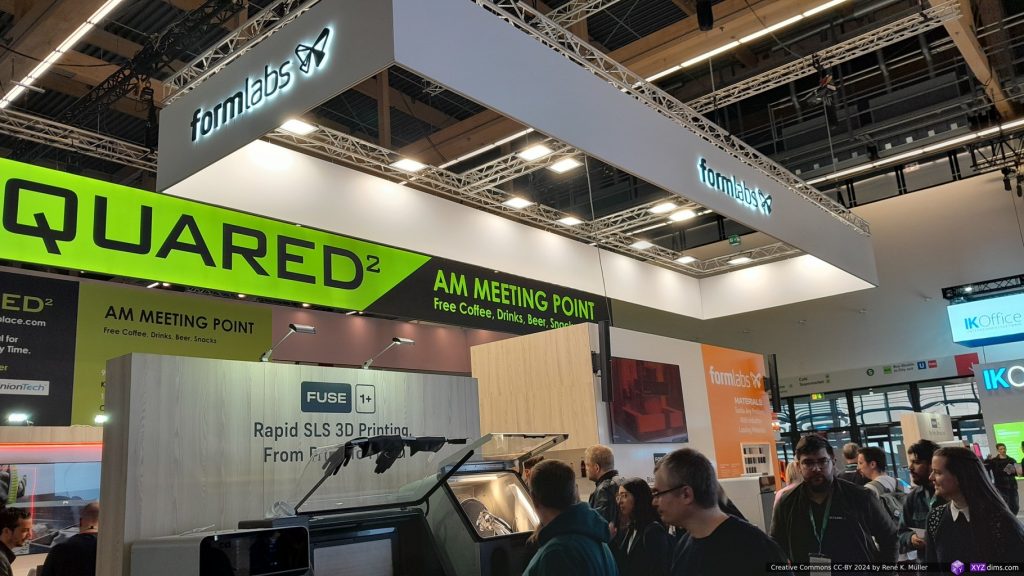
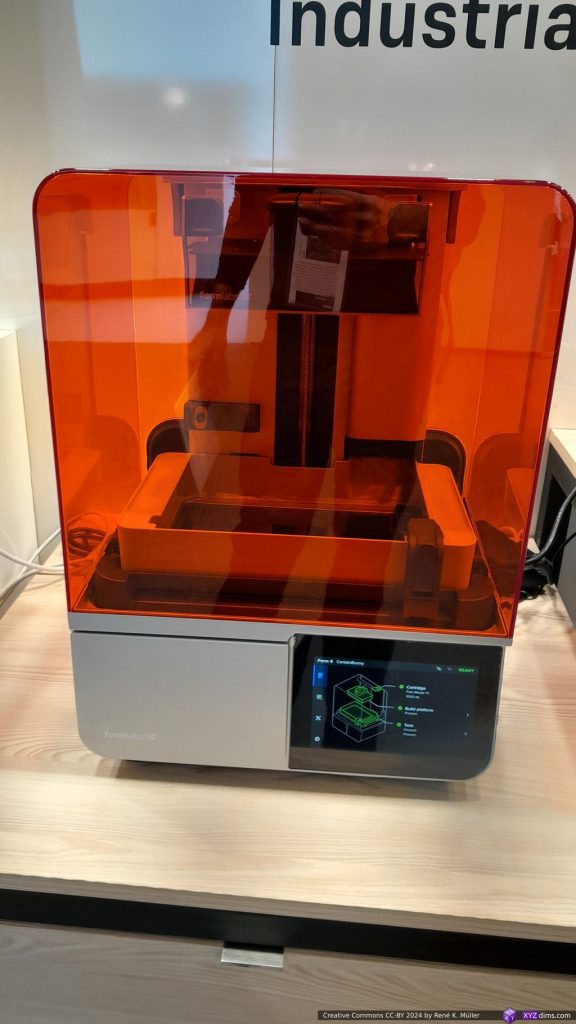
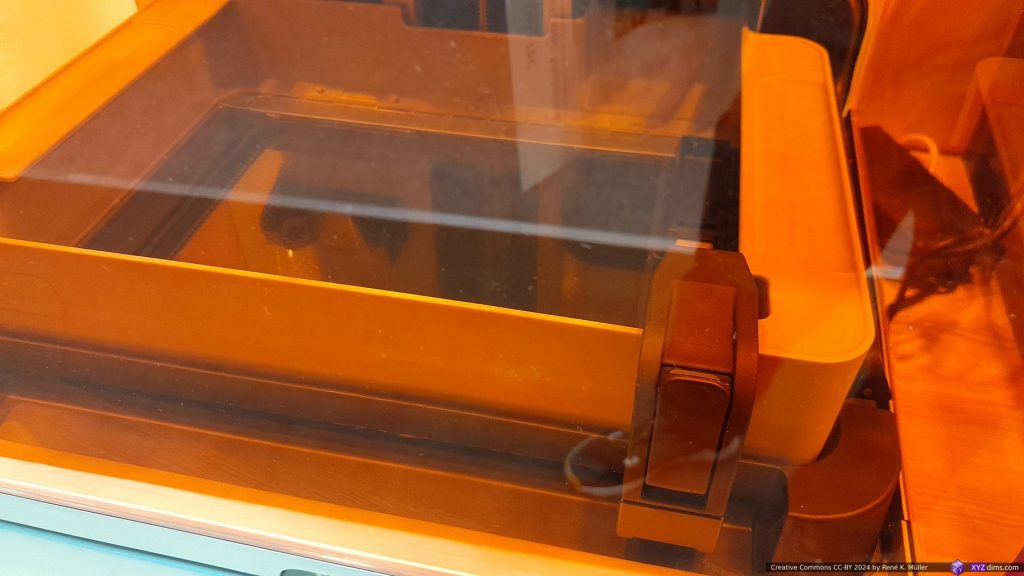
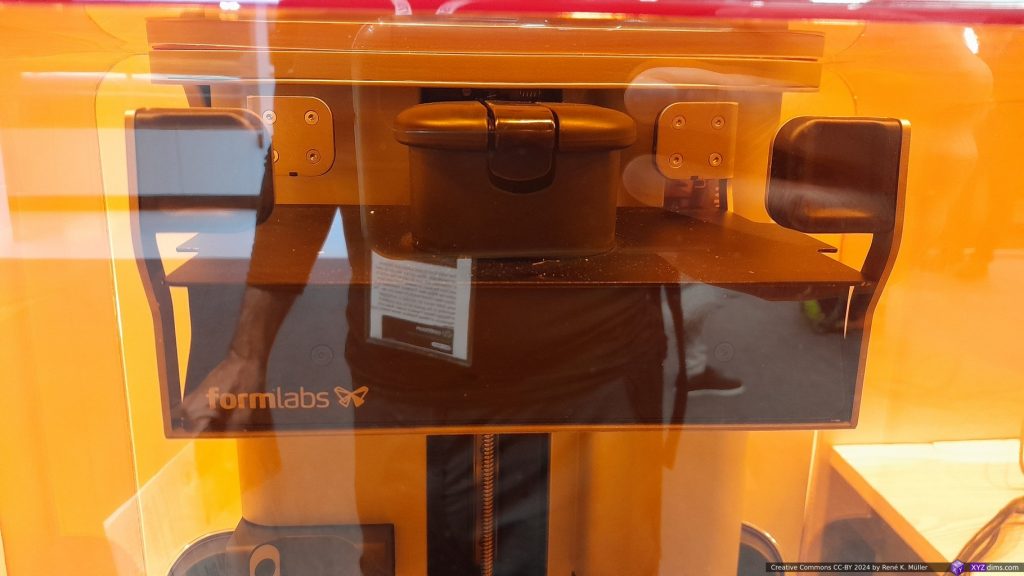
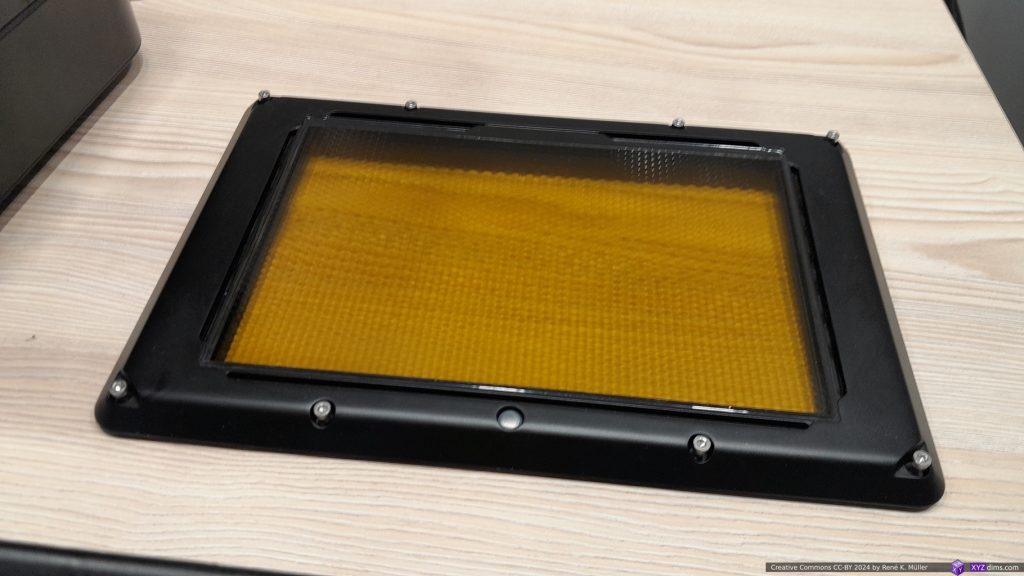
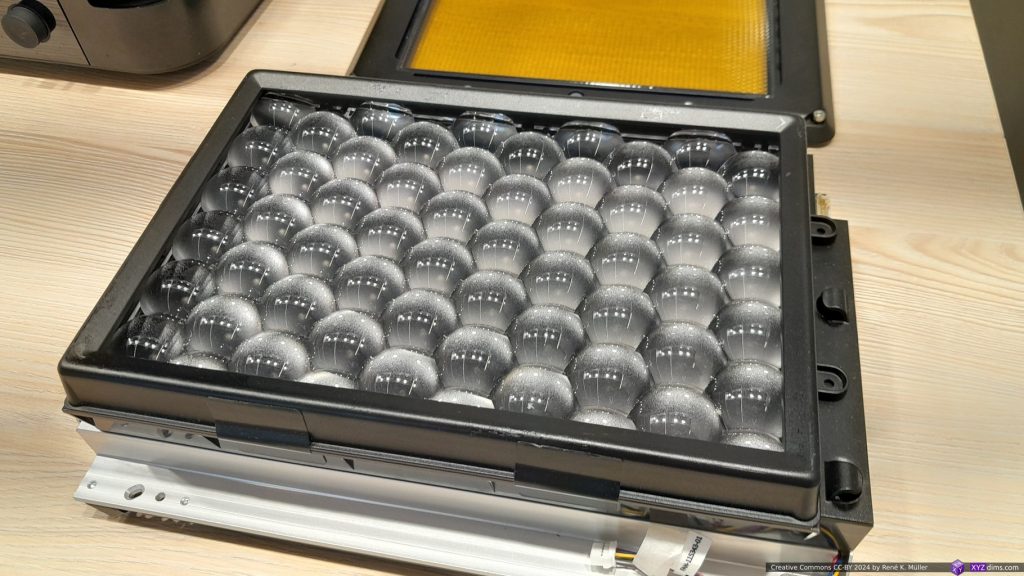

I highly recommend the taking apart of the Form 4 by Shane Wighton / Stuff Made Here to get to know all the engineering work which went into the new series.
See more at Formlabs.com
Shenzen Jiexinhua Technology Co. Ltd (SOVOL)
The company behind the commercialization of the VORON series with their SOVOL printers, SOVOL 08 or SV08, a Core XY 350x350x450mm build volume, priced at 550 EUR.
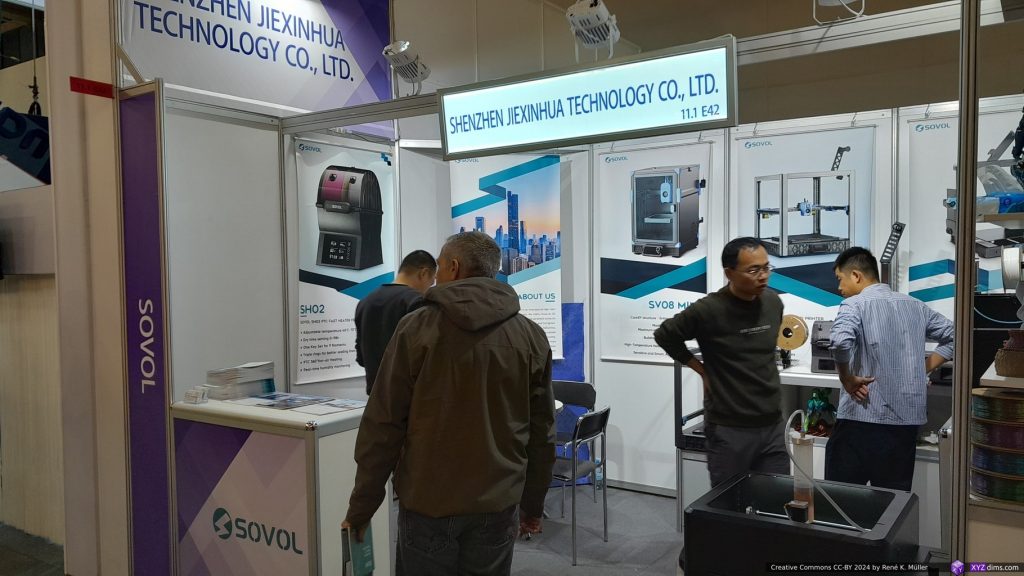

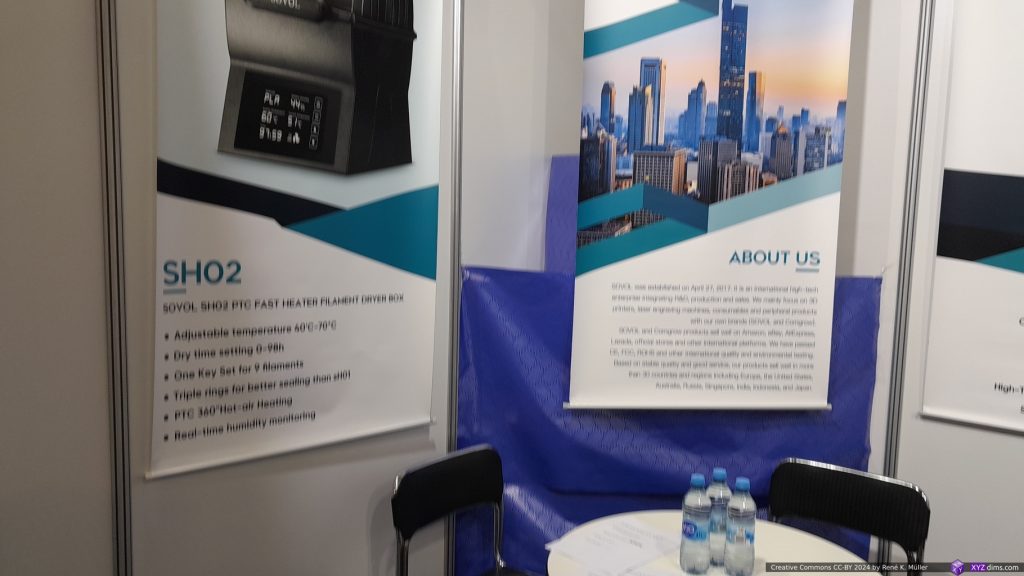
See more at Sovol3d.com
Micro Factory
A small german startup Micro Factory automated the resin printing (incl. washing & curing) within a single case:
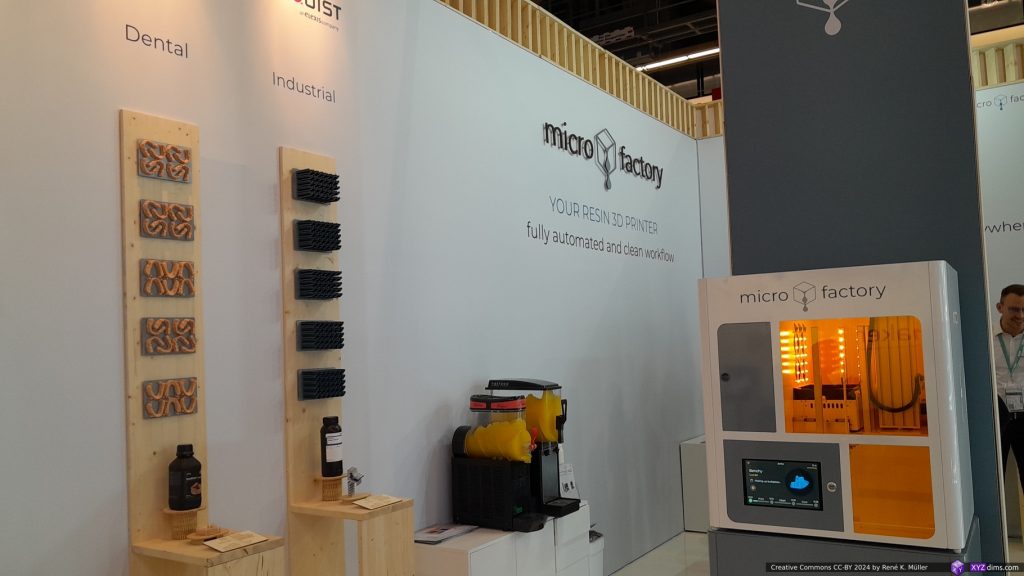
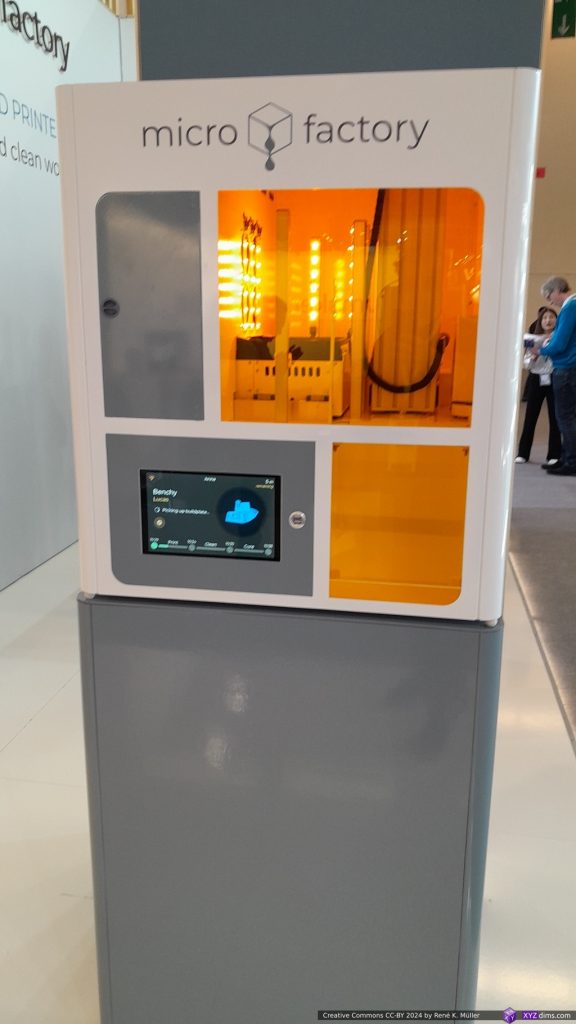
Here a brief video of the process (with german commentary in the background):
- printing with resin vat
- moving plate into isopropyl alcohol (IPA) vat
- moving plate to curing position & drying with fans
- detaching magnetic plate via electromagnetic release
See more at Micro-Factory.de
So far only Genera‘s G3 does something similar where washing & curing is done in the same case/apparatus.
Prusa Research
Prusa Research announced at the Formnext their new Prusa Core One, a Core XY with 250x220x270mm build volume, nozzle temp. max 300°C, chamber temp. max 55°C, priced at EUR 1,350, with the ability to uprade from MK4S, available later in 2025.

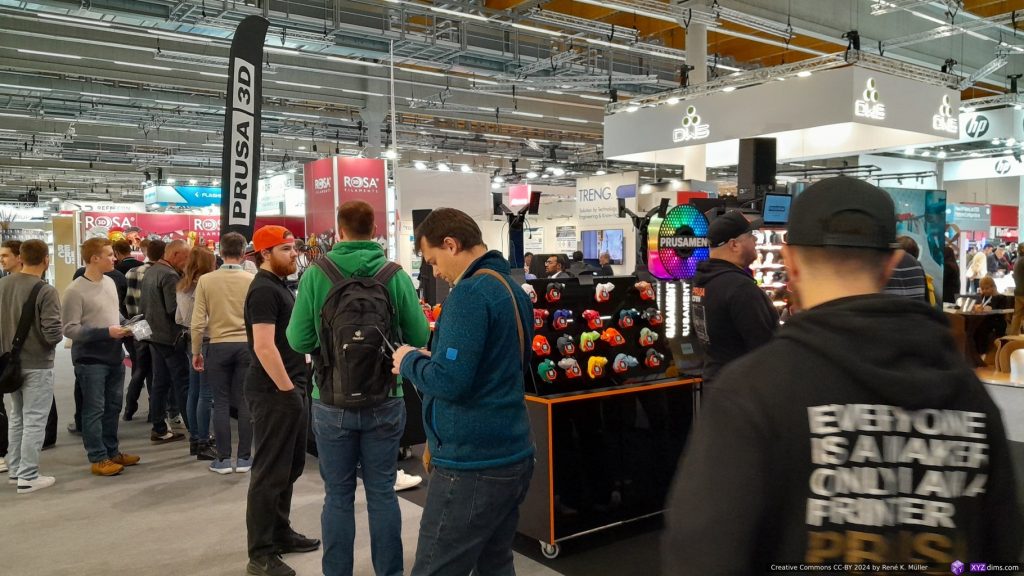
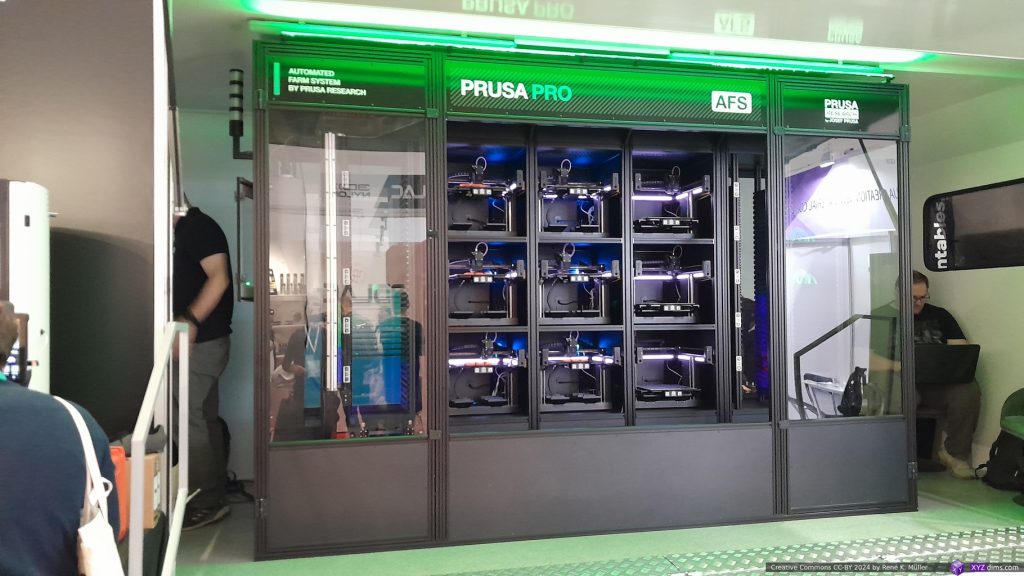
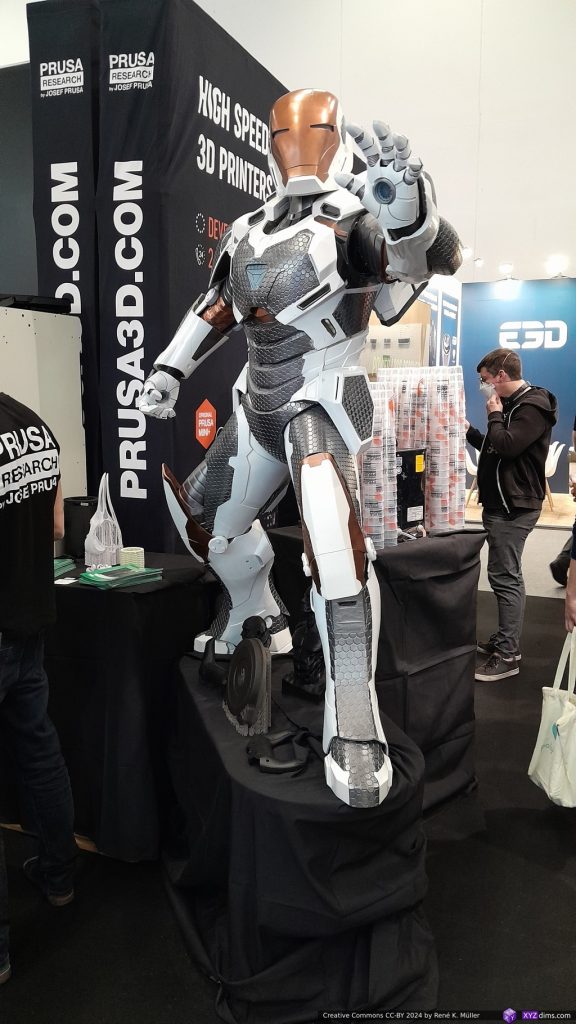
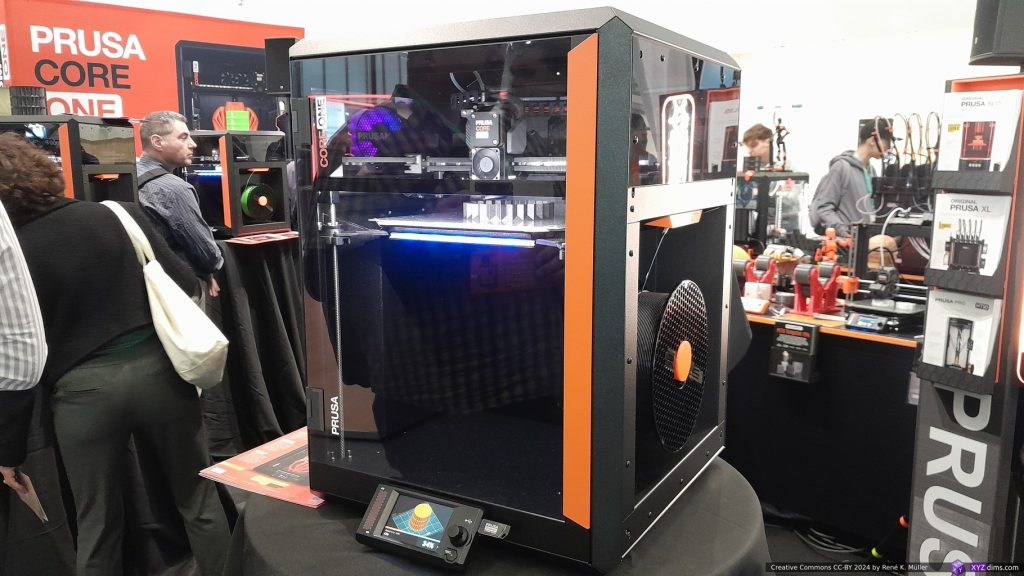
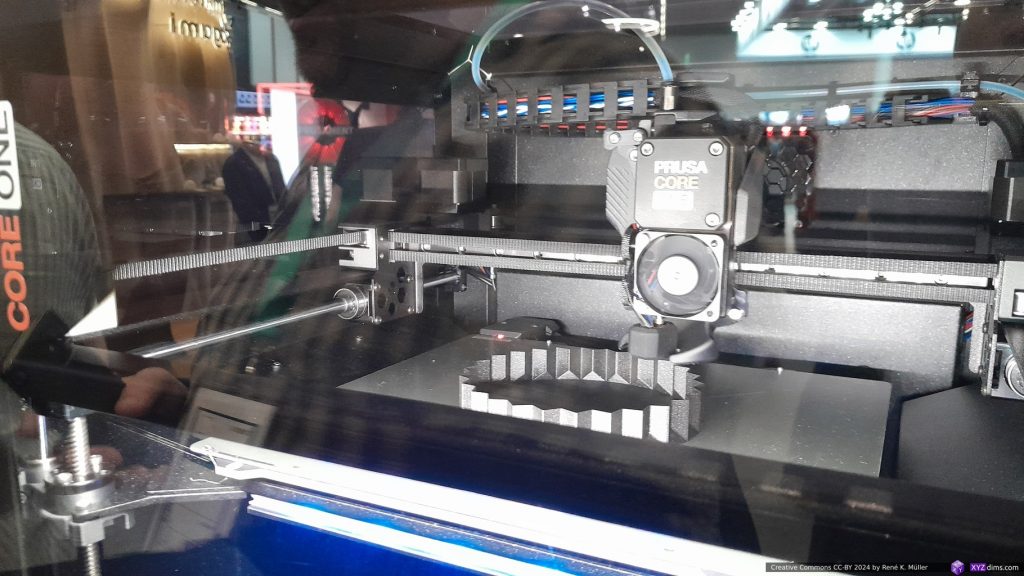
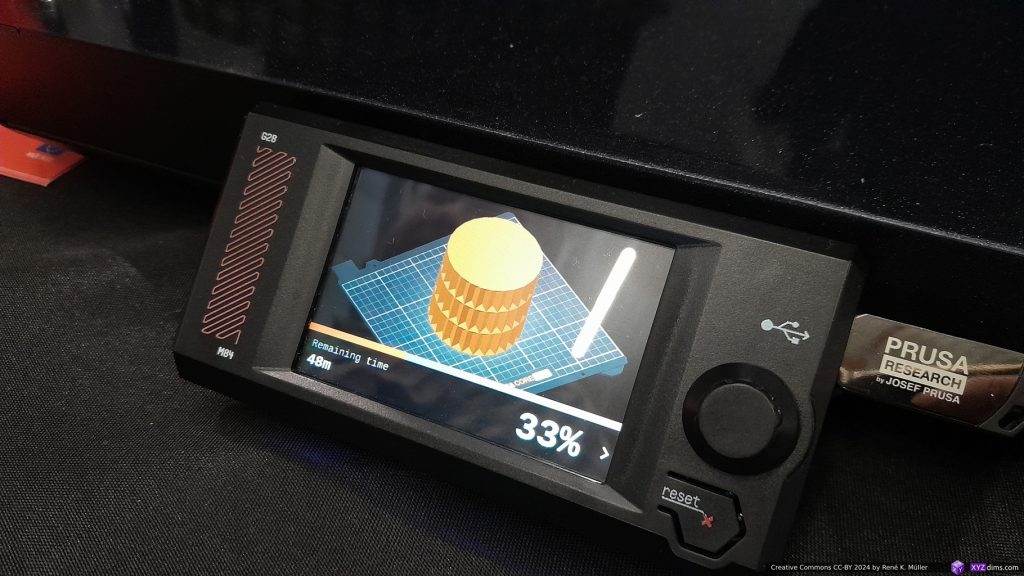

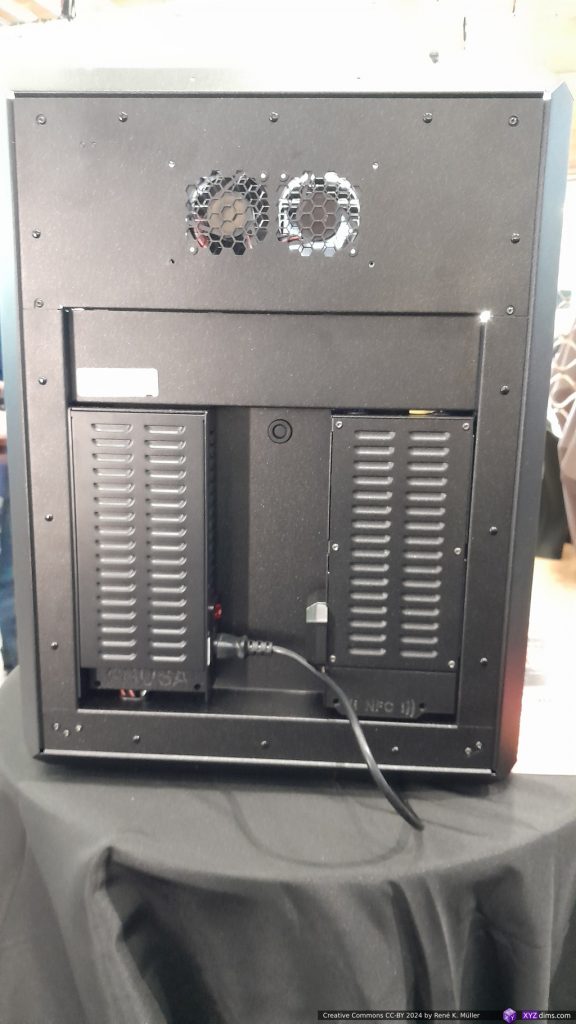
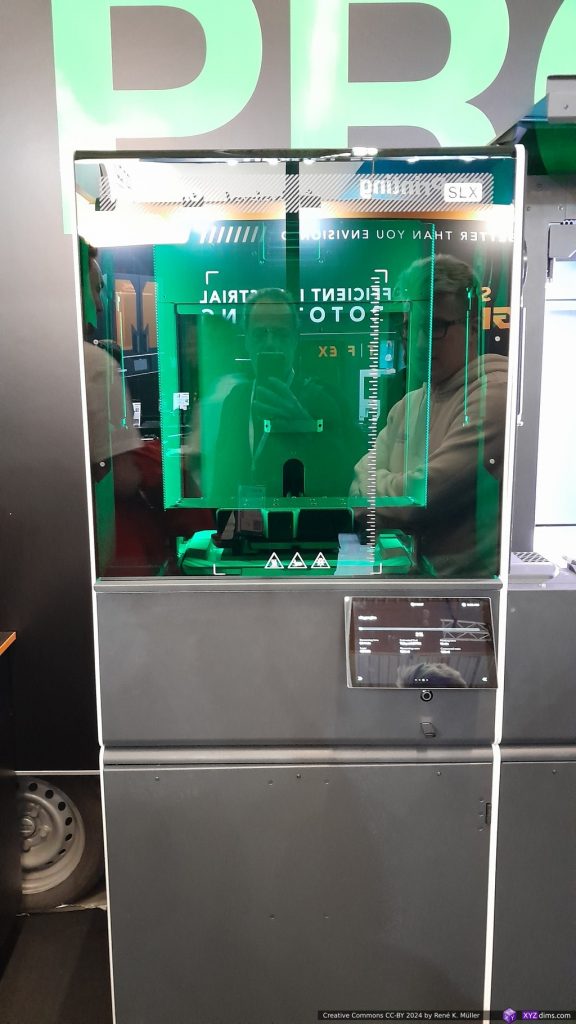
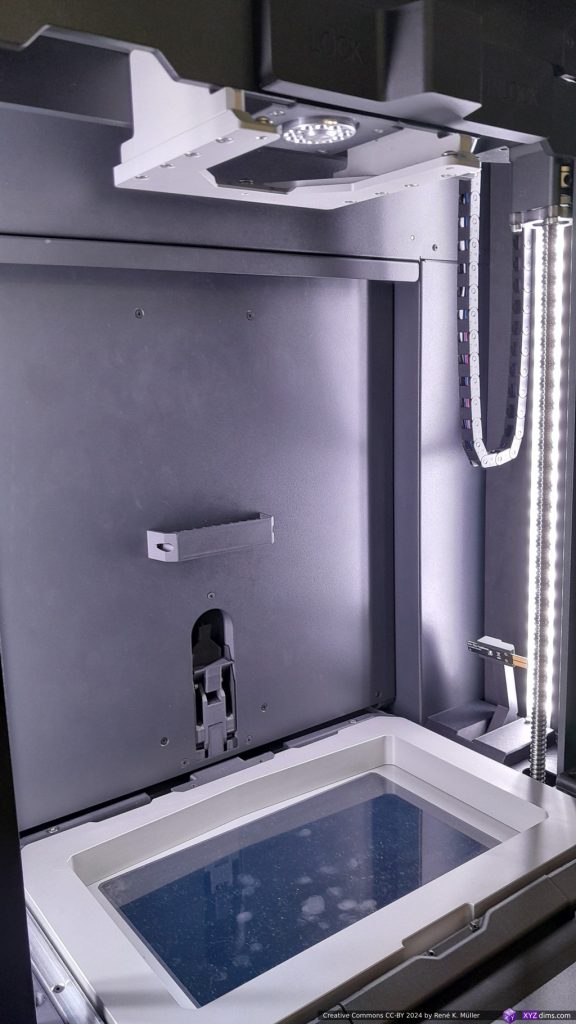
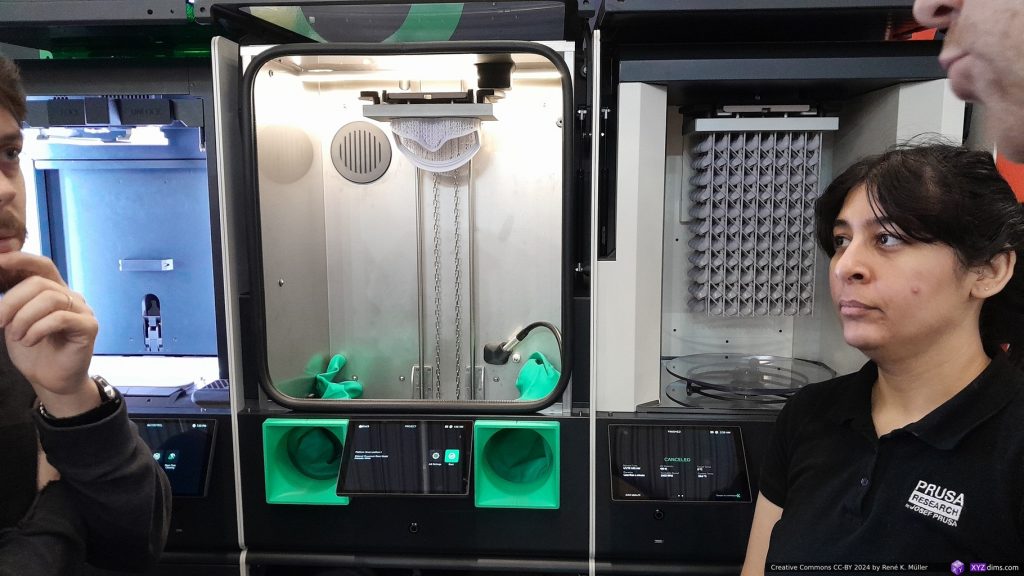
And the official announcement of Prusa Core One:
While I attended the Formnext, Hackaday published a sobering analysis on Prusa’s Open Source stand: With Core ONE, Prusa’s Open Source Hardware Dream Quietly Dies (2024/11/20).
One may argue, Prusa reached a state of commercial success, that it can’t afford to support low-cost chinese replicas of their invention, exactly as it happened to Makerbot and Ultimaker – and both stopped innovate, and recently merged – let’s see if Prusa will thrive in hardware innovation the coming years or lay back as well.
Open Source Software seems more tolerable to commercial pressure: Prusa Slicer still actively developed and forked many times, and so the Cura Slicer by UltiMaker; both slicers enable countless university labs and commercial engineering offices to develop new hardware and having an Open Source implementation of reliable slicers with a ton of detail knowledge embedded when one studies the source code.
See more at Prusa-Research.com
UniFormation
Rather unknown brand to me caught my attention the past year due to high praise from various YouTube reviewers: the older GKTwo (228x128x245mm @30um) ~670 EUR and the new GK3 Ultra (300x160x300mm @20x26um) ~1,200 EUR.
- integrated heating system at 35°C
- resin feeding system & resin weight measuring
- built-in air filter
Industrial-level features while maintaining consumer pricing.
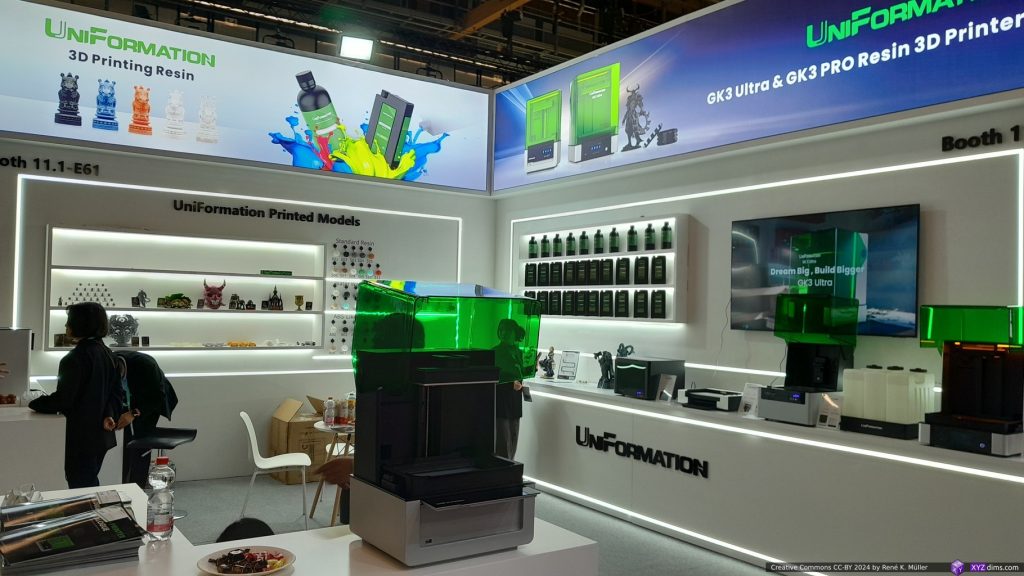
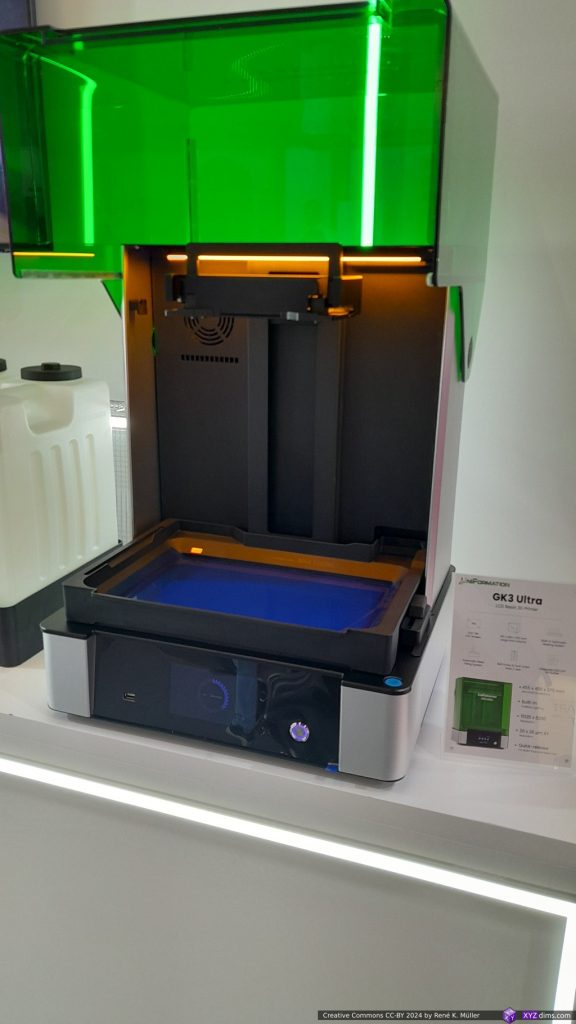

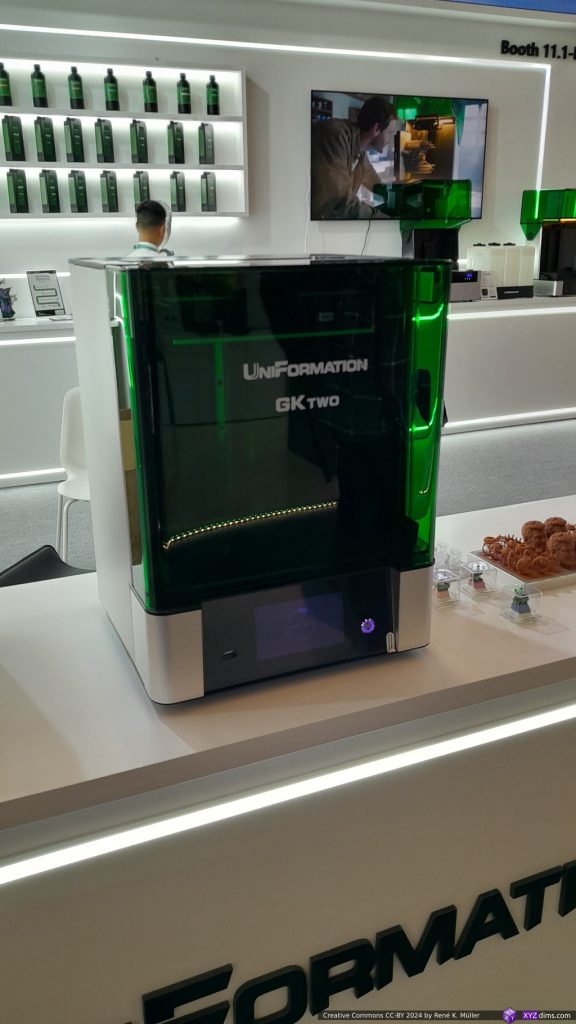
See more at UniFormation3d.com
ApexMaker

The booth featured Pengji (LCD maker) and Apex Maker (MSLA printers) together, so I assumed they are the same business with different brands with LCD making as core business – a representative at the booth confirmed my guess – so aside making UV LCDs they started to produce their own series of MSLA 3D printers:
- ApexMaker X1: 353x198x400mm @46um pixel resolution
- ApexMaker X1 Mini: 223x126x210mm @17um
- ApexMaker X2: 285x214x400mm @25um
- ApexMaker X2 Mini: 152x87x210mm @17um
Plus their own branded resins, curing and washing stations, see more at Apex-Maker.com
Elegoo
This year Elegoo released Mars 5 Ultra and the Saturn 4 Ultra which have tilting vat alike the Prusa SL1S which decreases layer print time (curing + detaching from film) down to apprx. 5 secs; so I was eyeing to get a Saturn 4 Ultra.
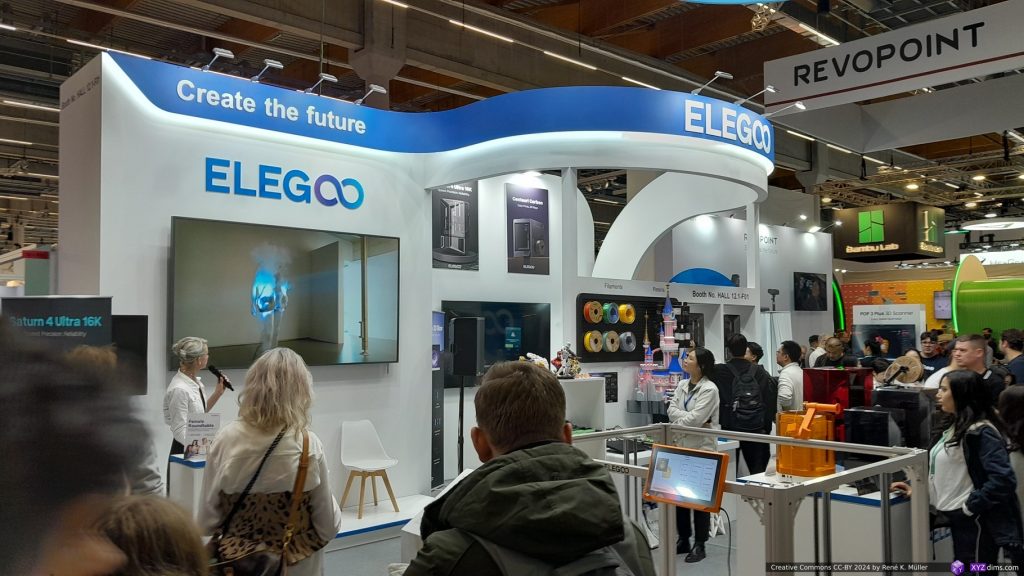
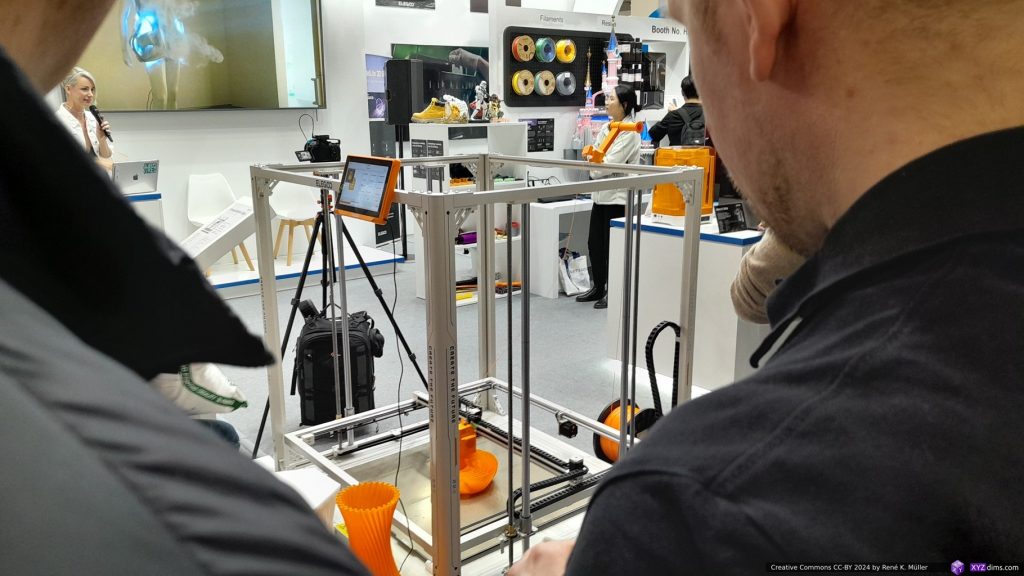
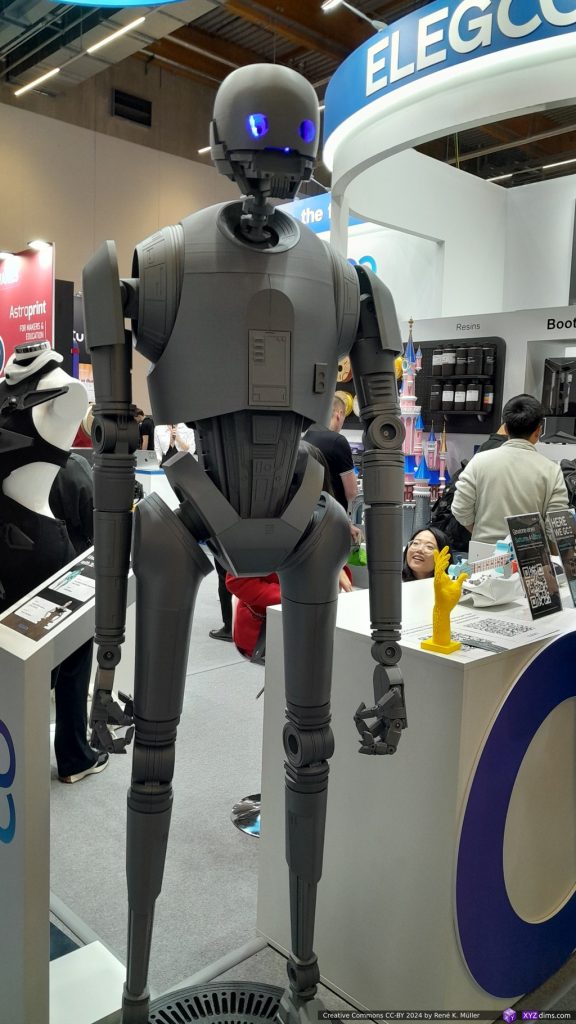
Thursday morning I revisited the booth and asked about whether Saturn 4 Ultra would permit to put a magnet flex plate on it – which would change the Z offset for homing, and two representatives explained to me it would be a bad idea as the home aka zero Z-position would fail, and one would require the change the “G-code” in the firmware (which is closed-source) . . . in other words, the Z offset or home position is somehow hard coded and doesn’t use pressure sensor to calibrate home (this Reddit thread shows Chitubox Slicer allows to alter the homing G-code, LycheeSlicer doesn’t have this option) – the usual rabbit hole.
See more at Elegoo.com
Anycubic
My resin printing farm is composed by Anycubic printers (Mono 4K, X2 and 6Ks), mainly due the diverse third party market for replacement and add-ons, so I was checking out their new Photon Mono M7 Max (298x164x300mm @46um) priced at EUR 900 (2024/11).

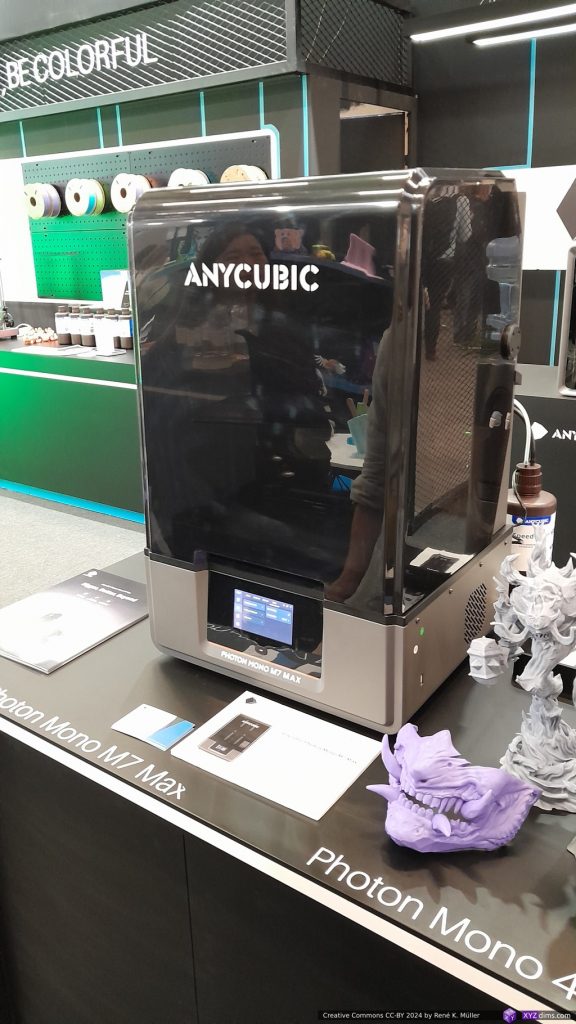
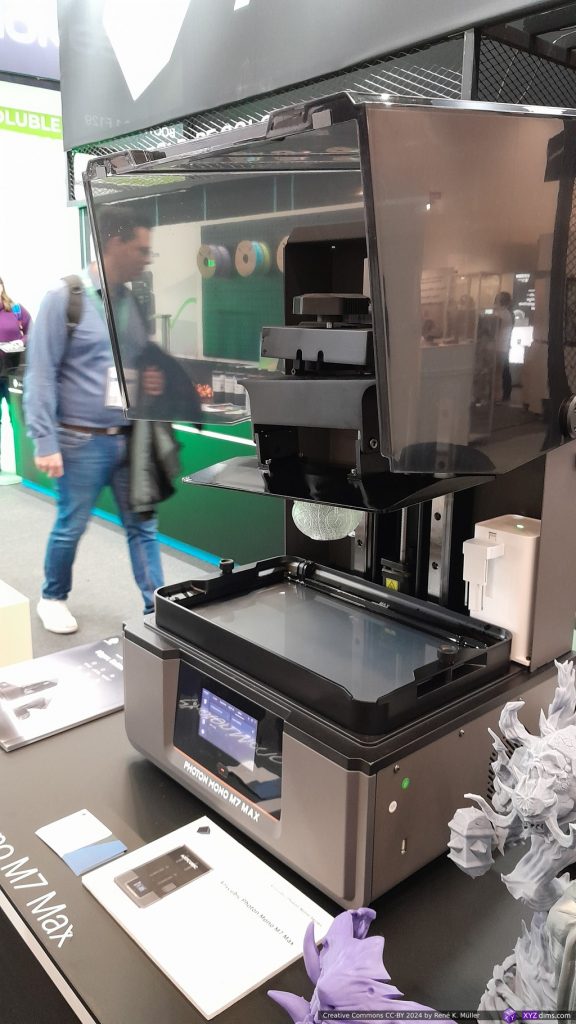
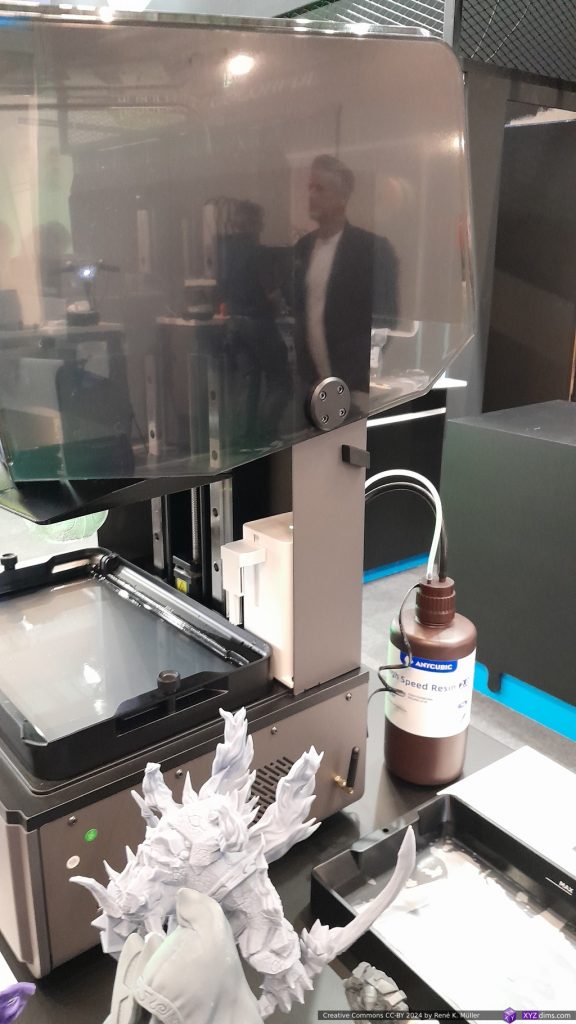
I was hoping Anycubic would also implementing tilting vat to decrease the print time and allow more delicate prints due more gentle / gradual detaching from the film with the tilting motion – so far not yet.
See more at Anycubic.com
Fooke & MELD
This basic looking booth I consider a gem among a few others at Formnext 2024, a sample of massive piece which was extruded with aluminium below the melting point using Additive Friction Stir Deposition (AFSD) procedure and yet creating a fully solid piece where layers fully bond – their main photo (1st photo below) or illustration at the booth was deceptive small at first sight, but after looking twice, I realized the entire machine “Fooke AM50” is over ~6m long with a huge build volume of 6 x 3.5 x 1.5m, and aluminium, magnesium, copper, steel and titanium as possible materials, with build rates up to 15kg/h – and all extruded in normal room atmosphere and temperature.
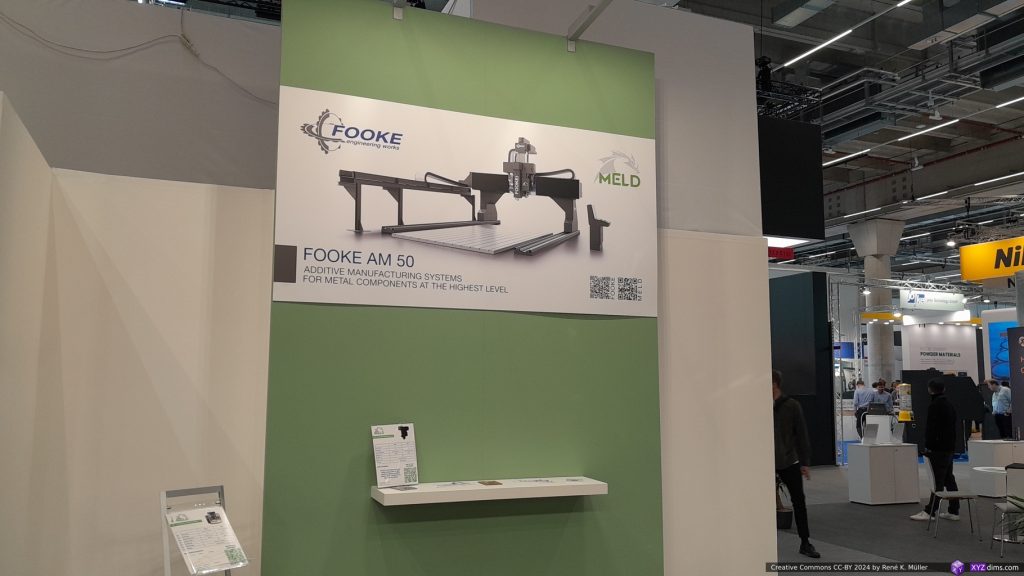
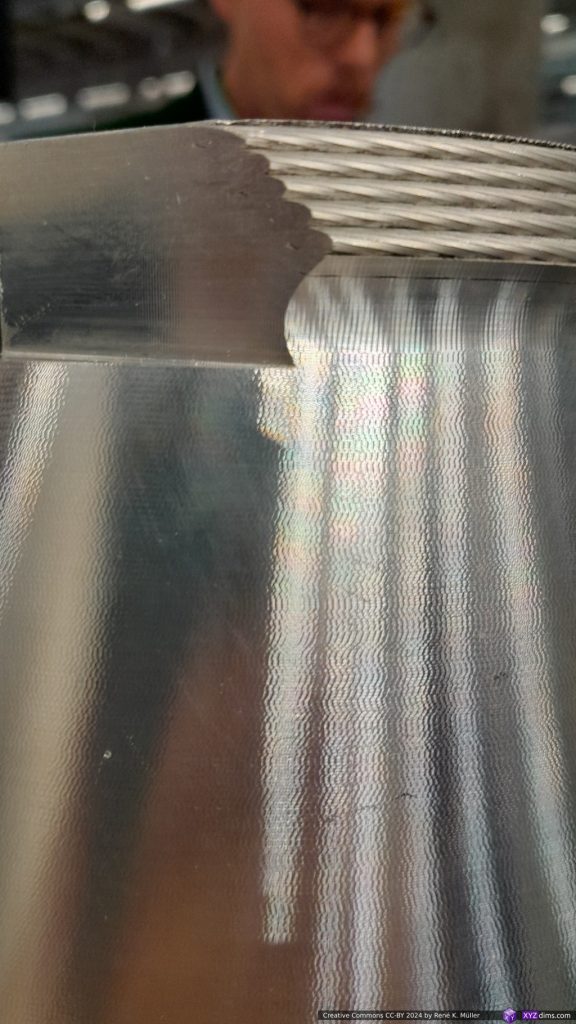
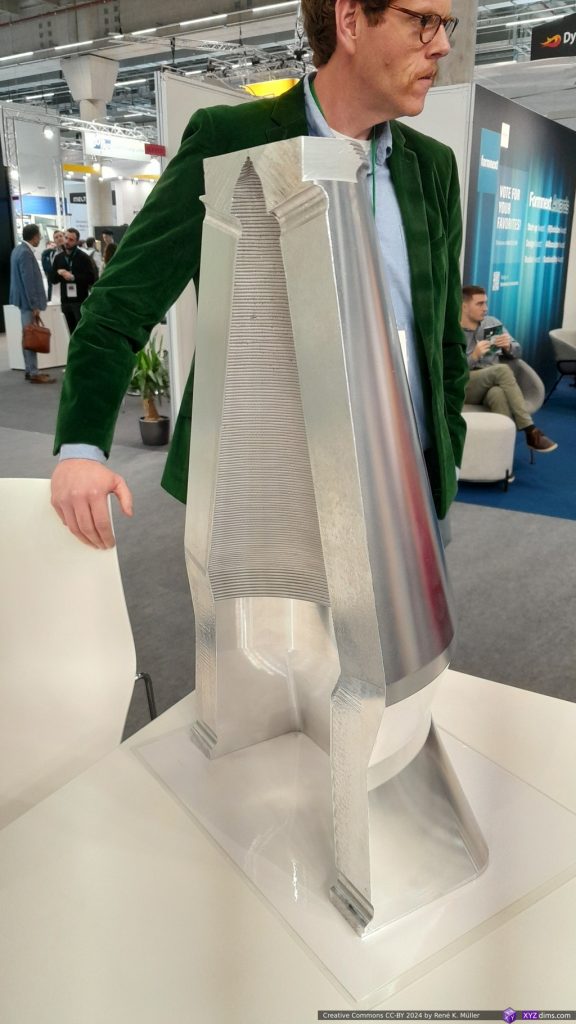
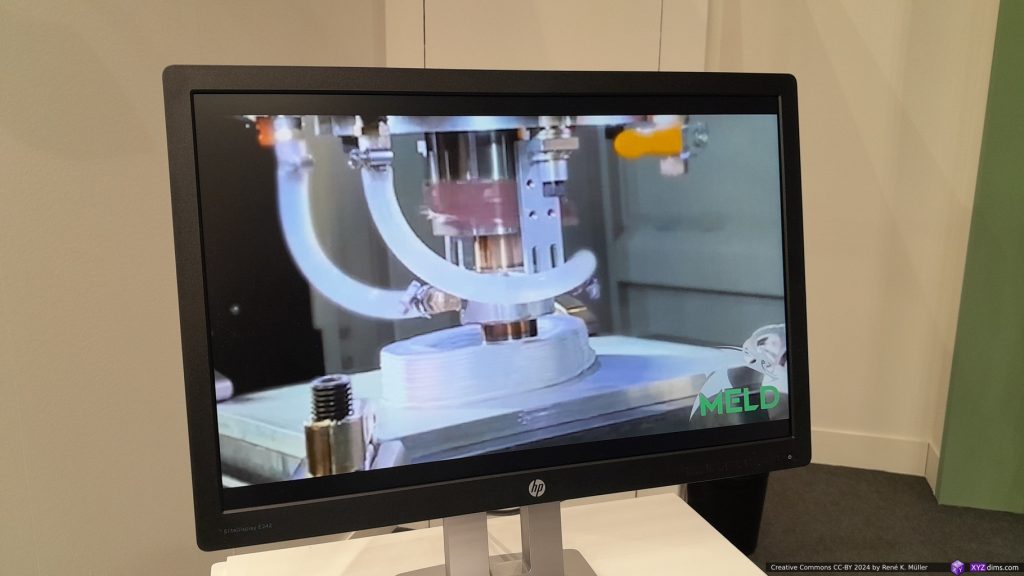
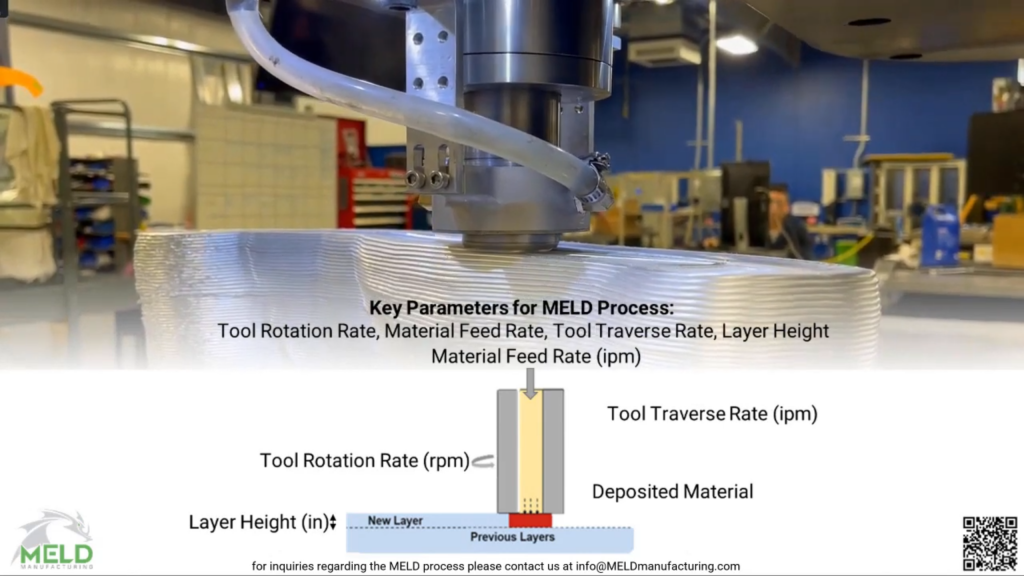
Following video gives an impression of AFSD & FSW based extrusion by MELD (unfortunately the audio is quite silent in most parts):
See more at Fooke Machines.com and MELDManufacturing.com
Spherene
A few weeks I wrote about them already, so I briefly visited their booth as well:
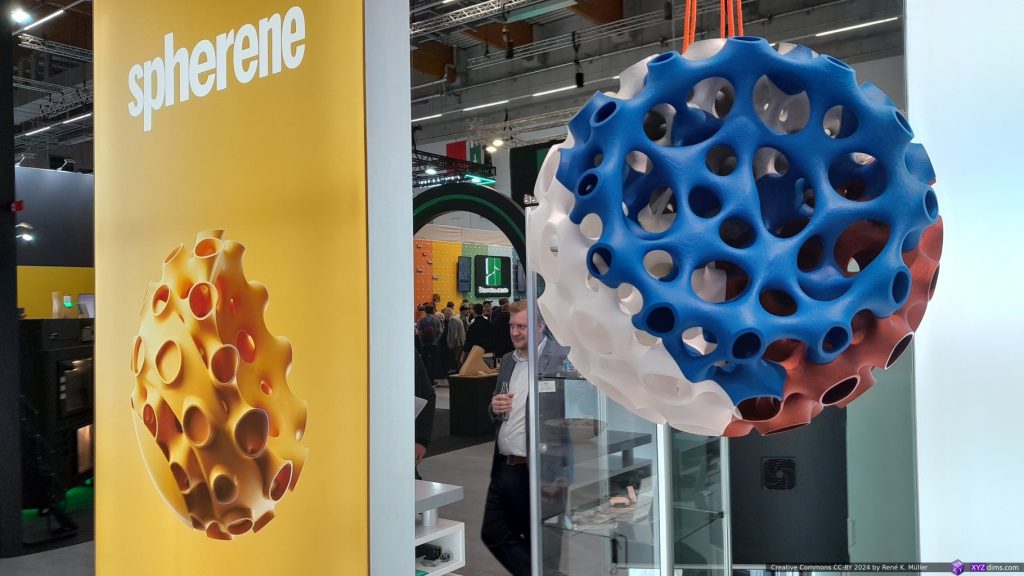
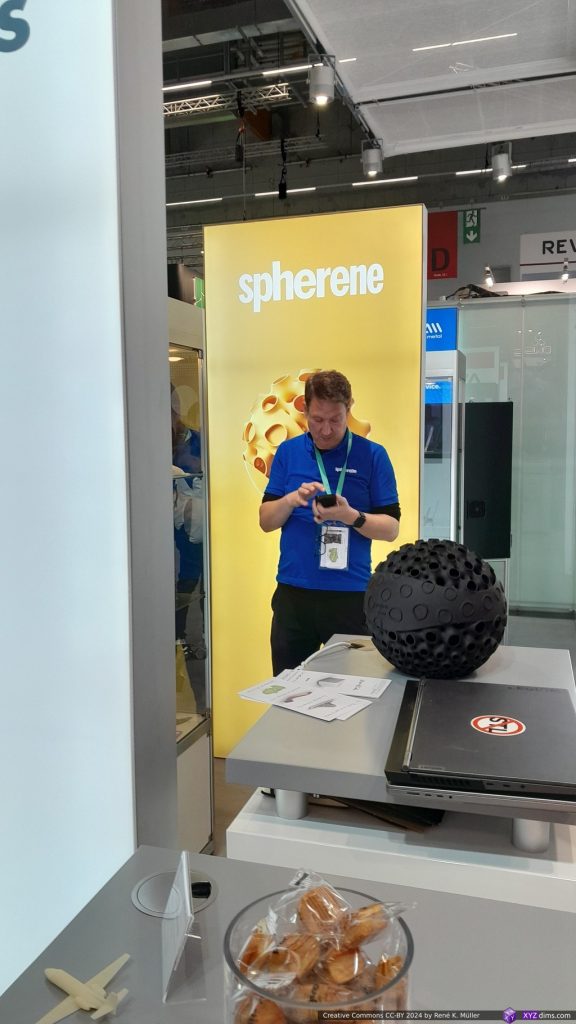
By chance I saw a small table printed with Spherene structure at the 3D Systems booth:
Spherene Side Table
Technology: Stereolithography (SLA)
Material: Accura® AMX Tough FR V0
Software: 3D Sprint®Long-term environmental stability (tested to 8 years indoor and 1.5 years outdoor mechanical performance per ASTM)
Designed by Peter Donders for:
– Material optimization
– Increased structural strength
– Customization and unique aestheticsThermoplastic-like mechanical performance including ductility and elongation at yield
Surface finish comparable to injection molded plastics
And here a brief feature from Formnext 2024 by AM:
See more at Spherene.ch, and also featured in the Joel Telling (3D Printing Nerd) Formnext 2024 stream.
Stratasys
The grumpy grandfather of 3D Printing:
- grumpy, because of the patent collection which caused the 20 year delay for others to be able to adapt major extrusion technologies, once they expired the “3D printing era” actually started with affordable 3d printers (MakerBot, Ultimaker, Prusa, and all the chinese replicates) and many prosumer derivates
- grandfather, because it’s truly the beginning of extrusion-based 3D printing / additive manufacturing
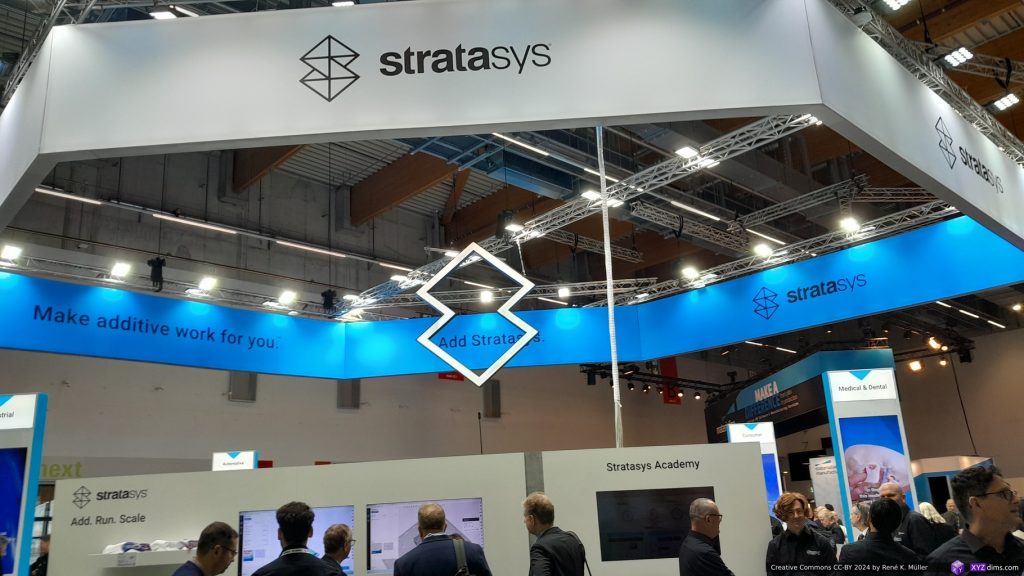
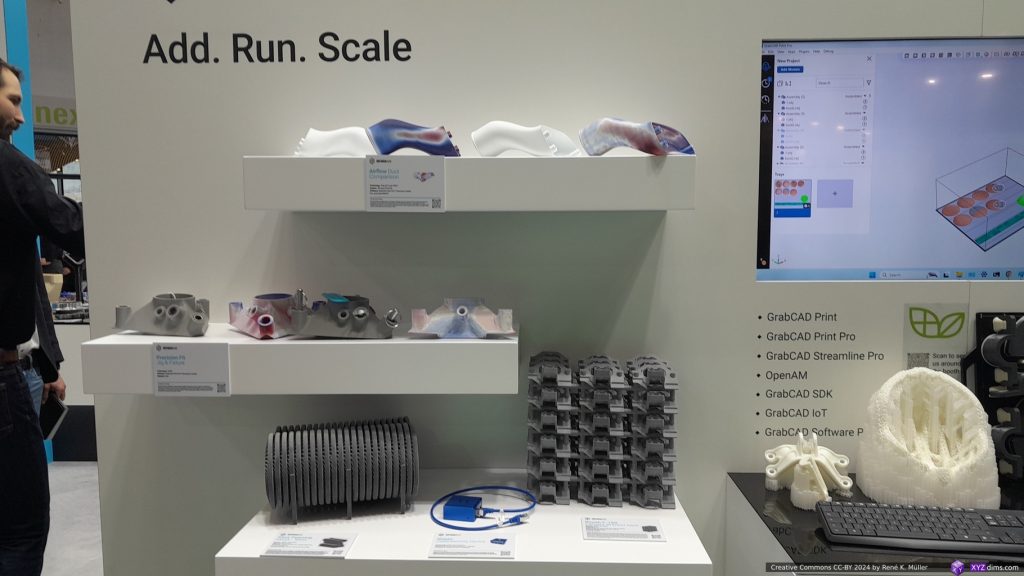
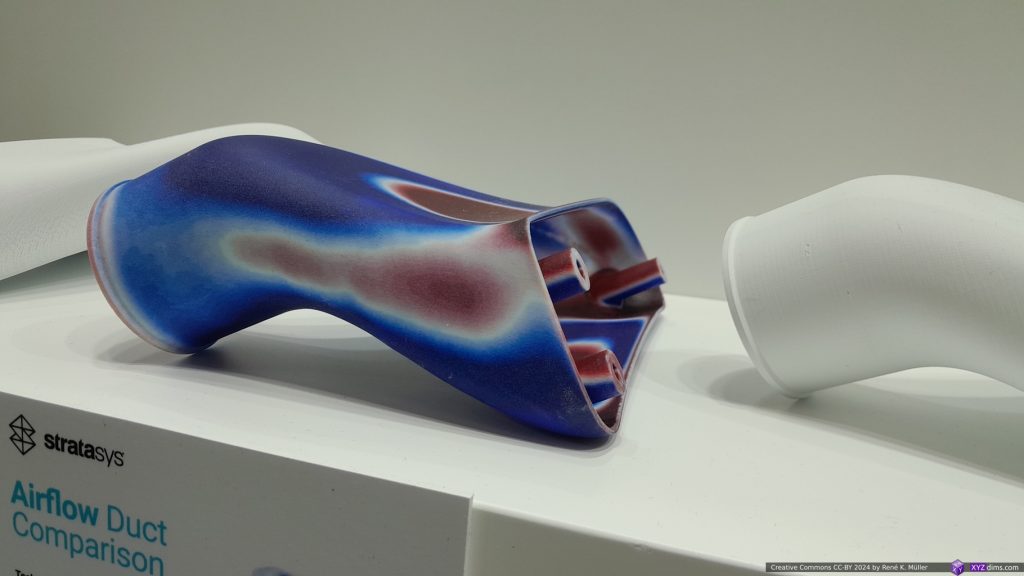
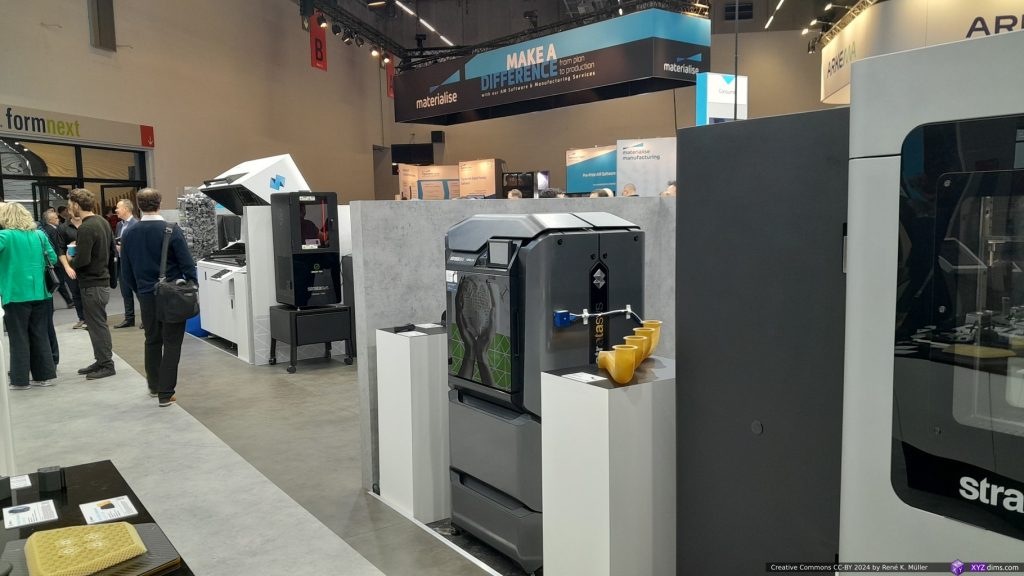
See more at Stratasys.com
Chinese Maker Source
A couple of chinese manufacturers providing DIY 3D printer parts:
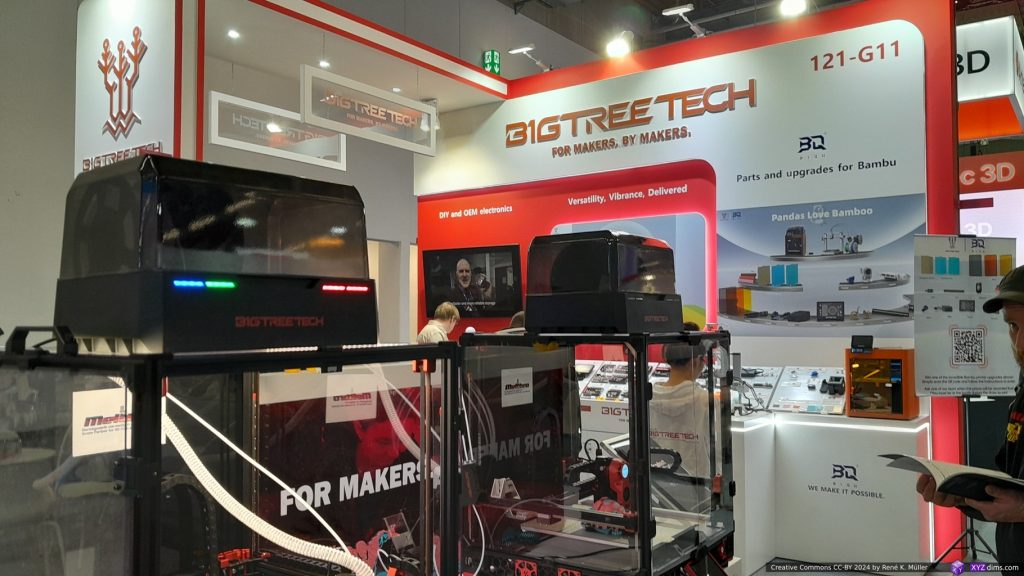
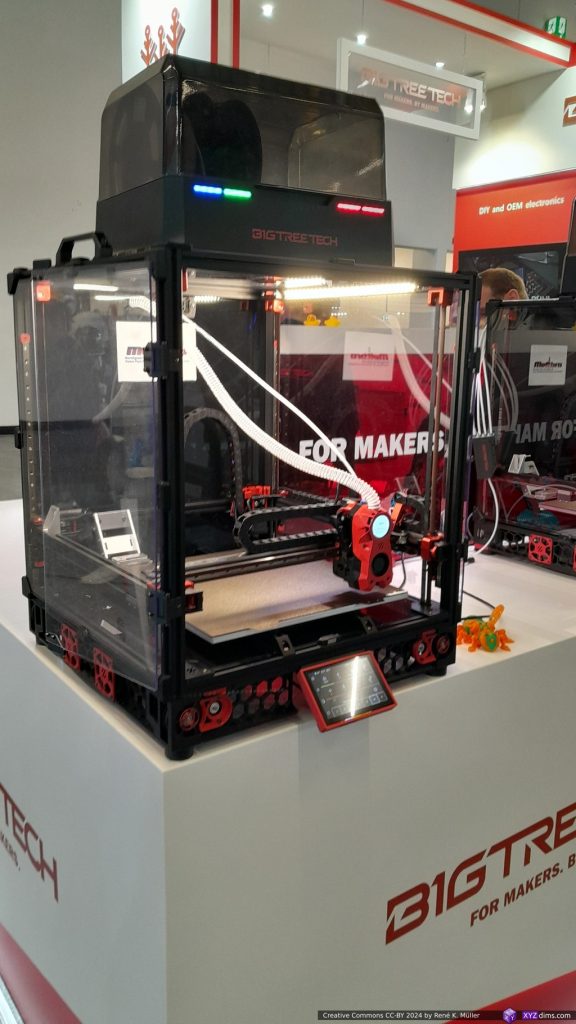
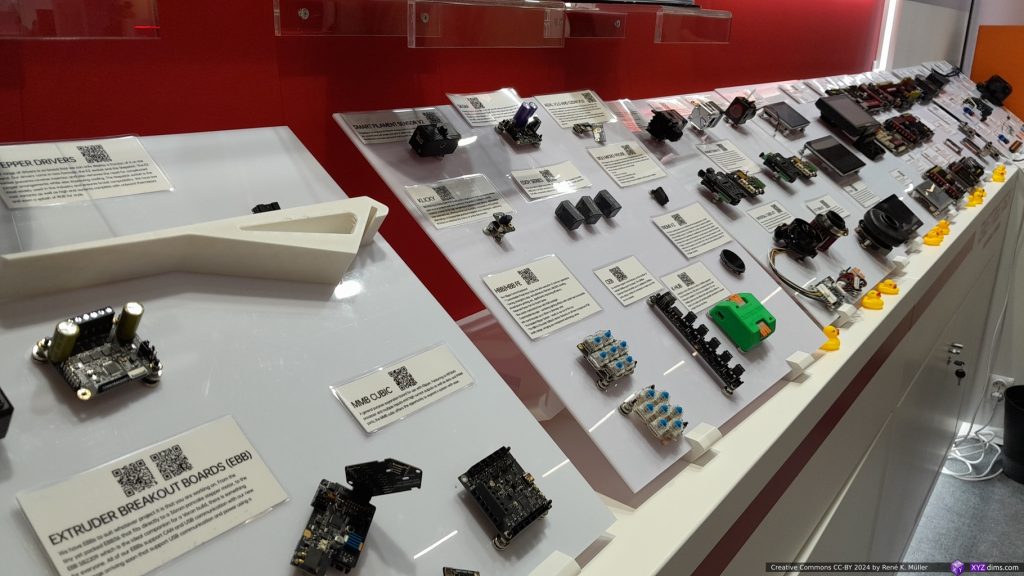
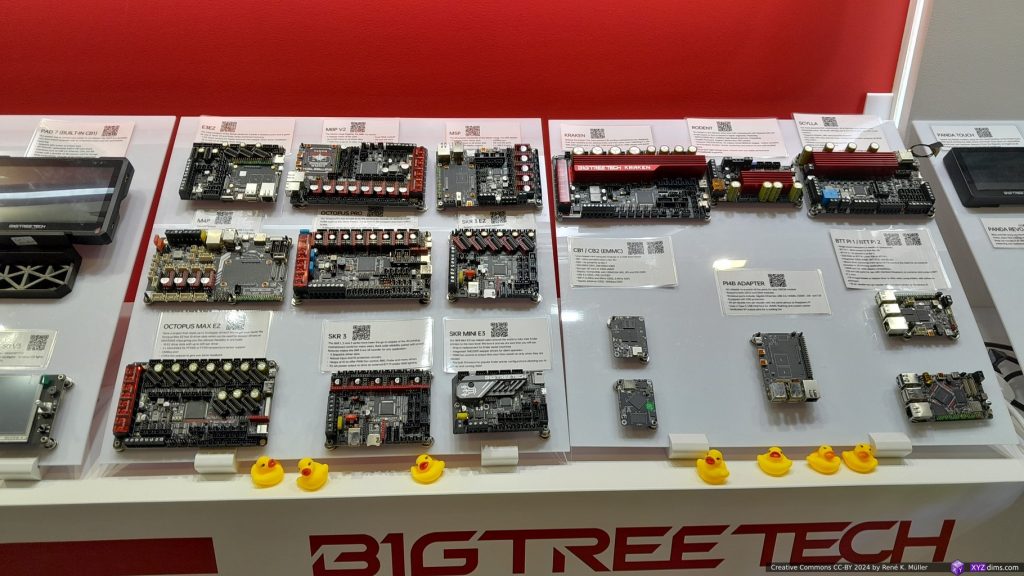
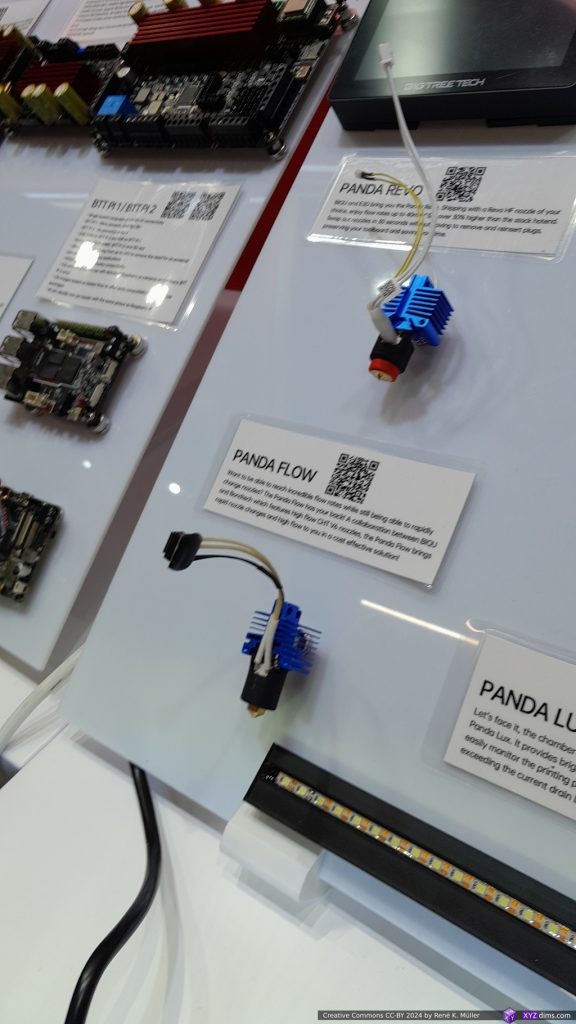
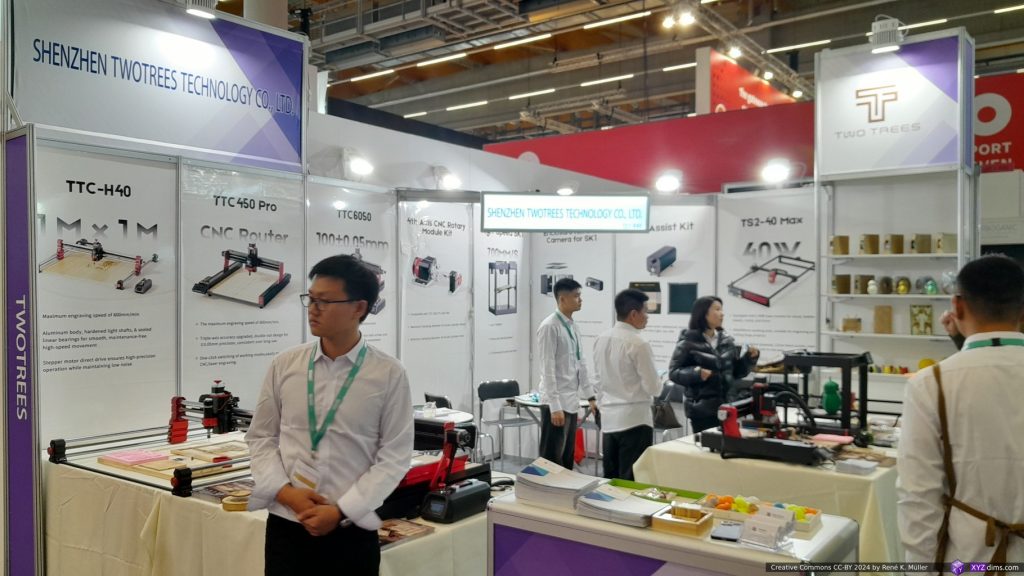
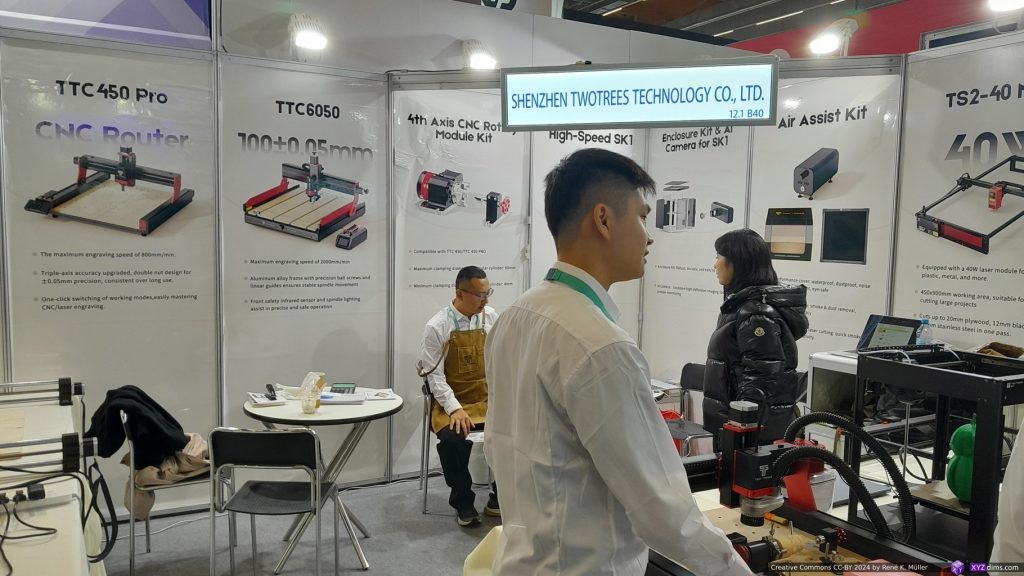
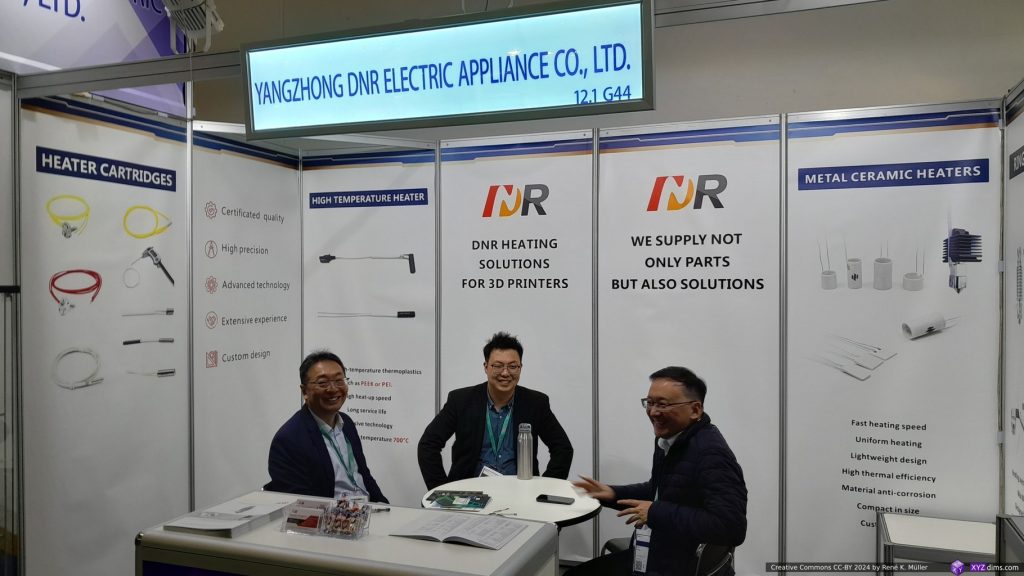
See more at
WASP
WASP has been around for quite a while with their expertise to extrude clay with their Delta printers but also industrial robots:
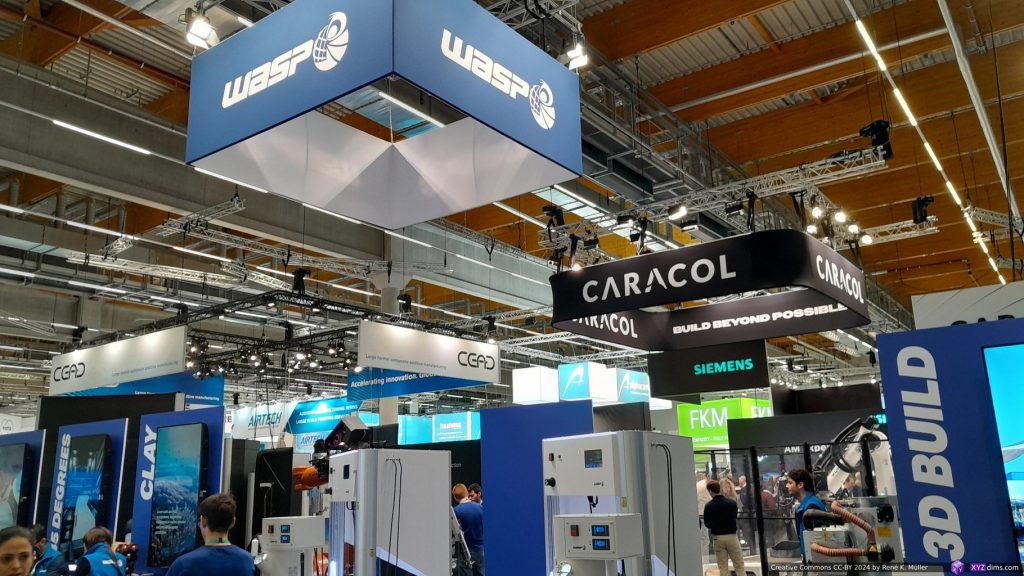
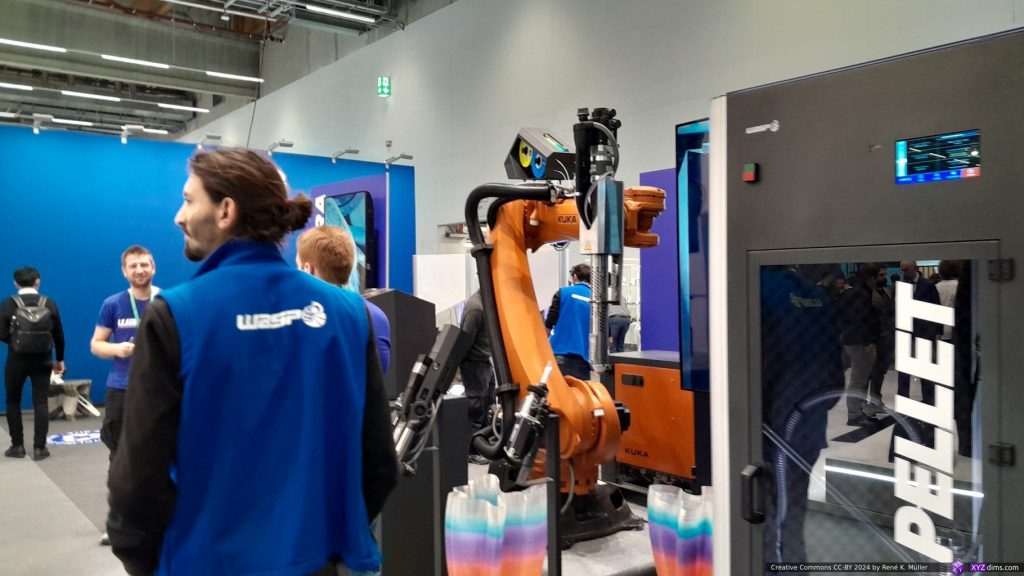


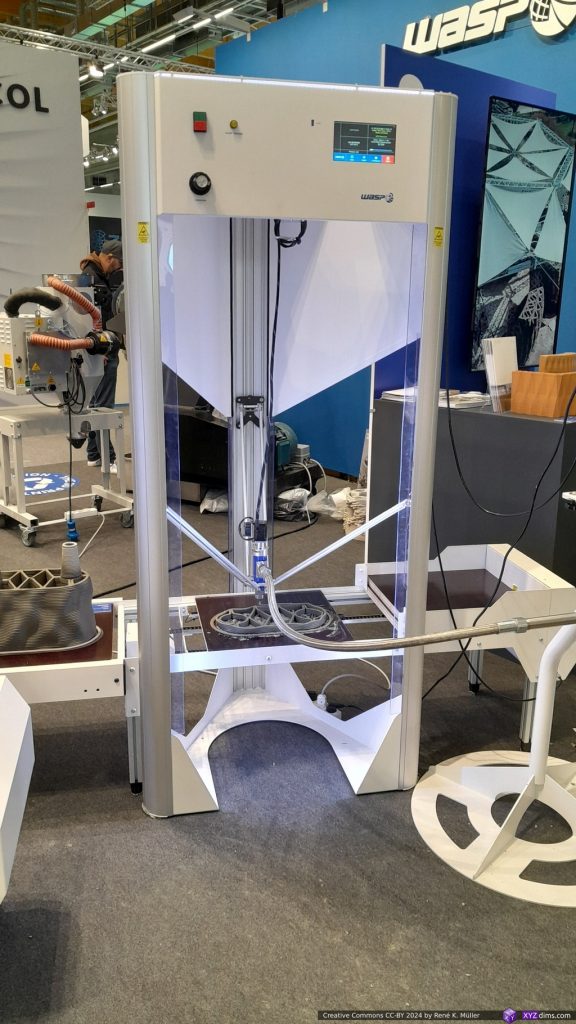
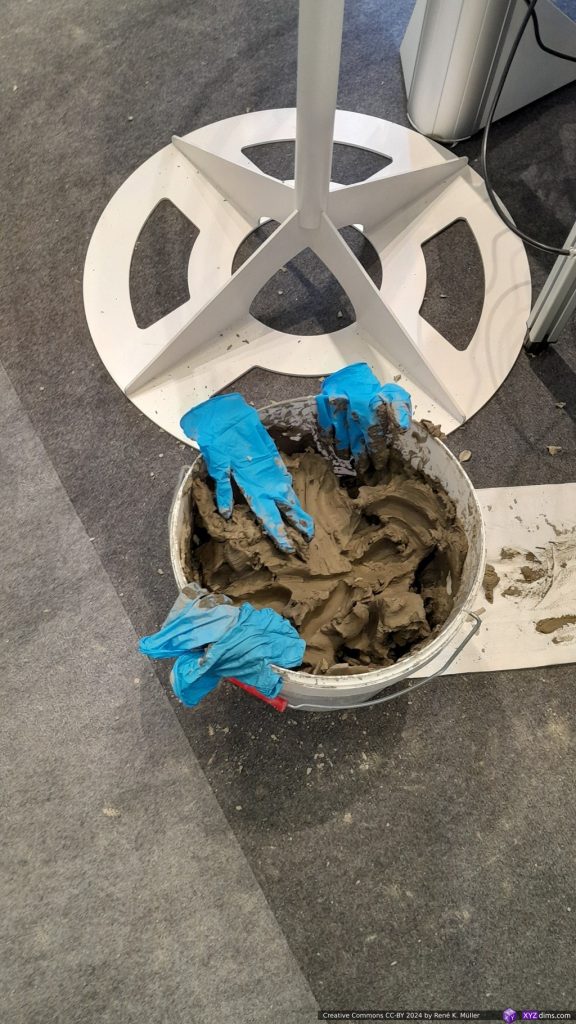
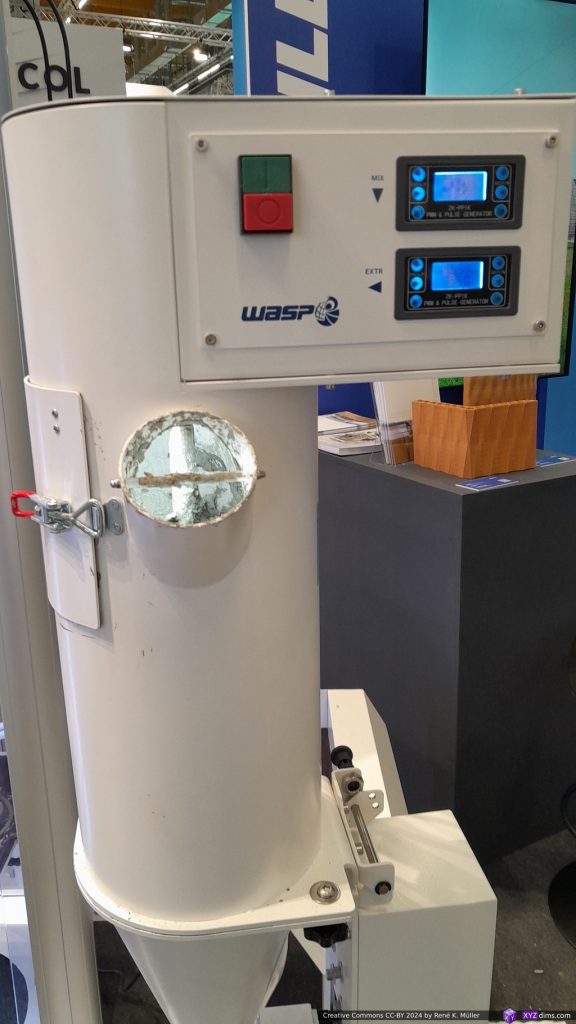

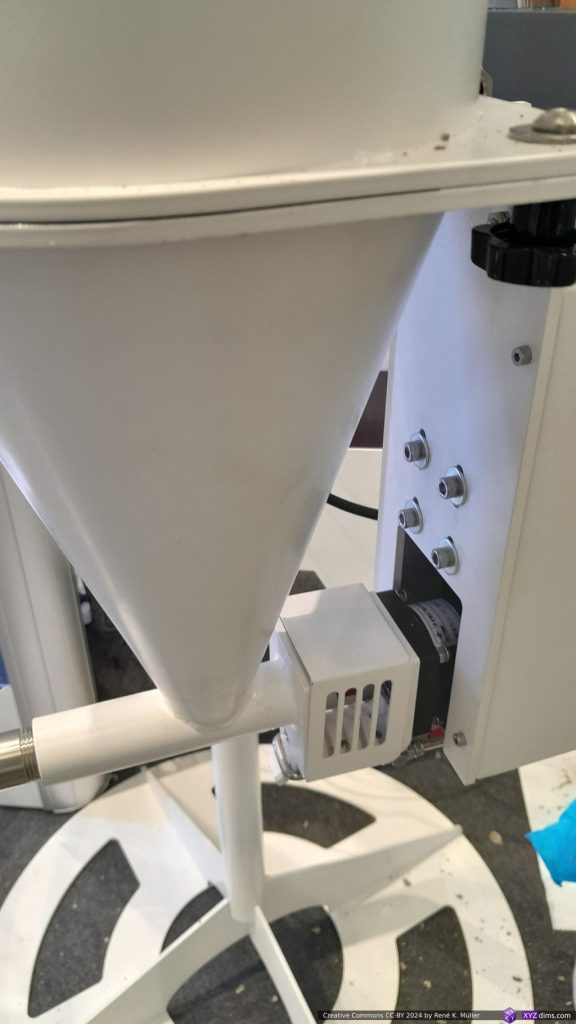



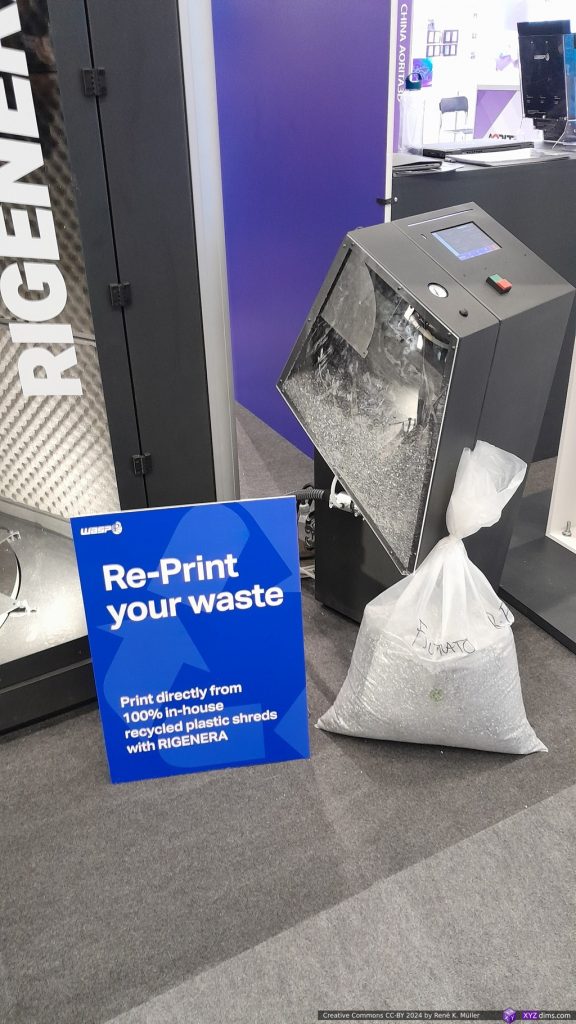
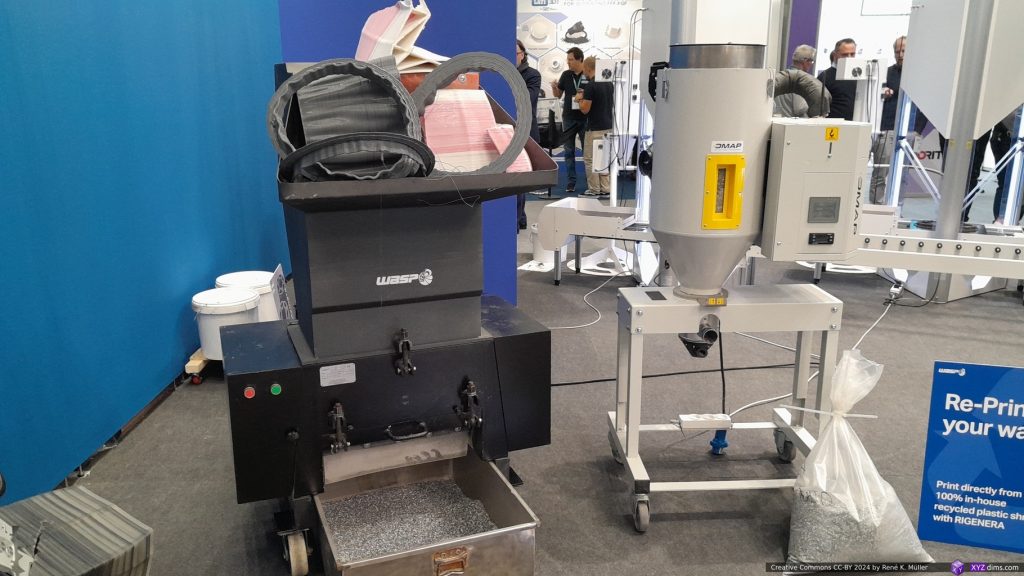
See more at 3D Wasp.com
Modix
Modix extended their offers from previous years with primary focus on cost-effective large build volume FDM/FFF printers, e.g up to 2m in Z:
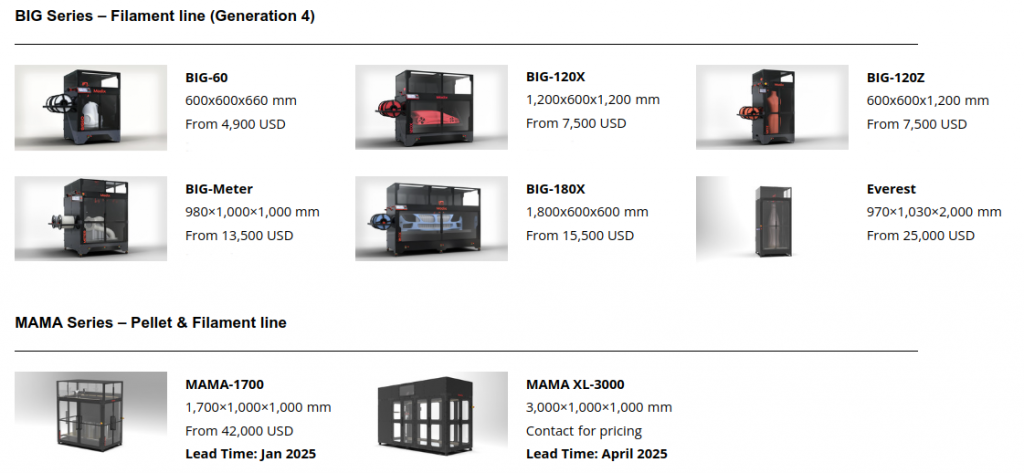
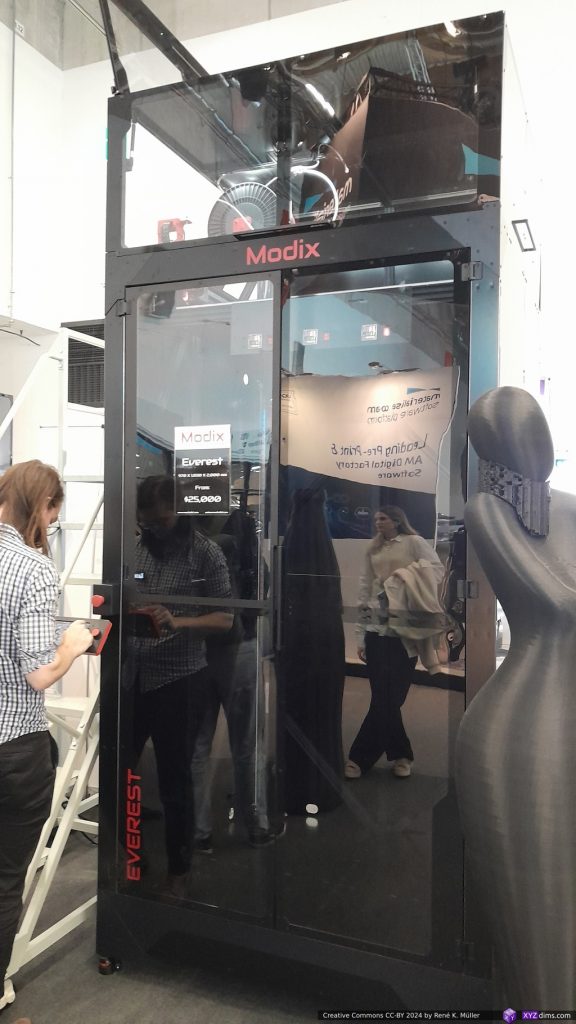
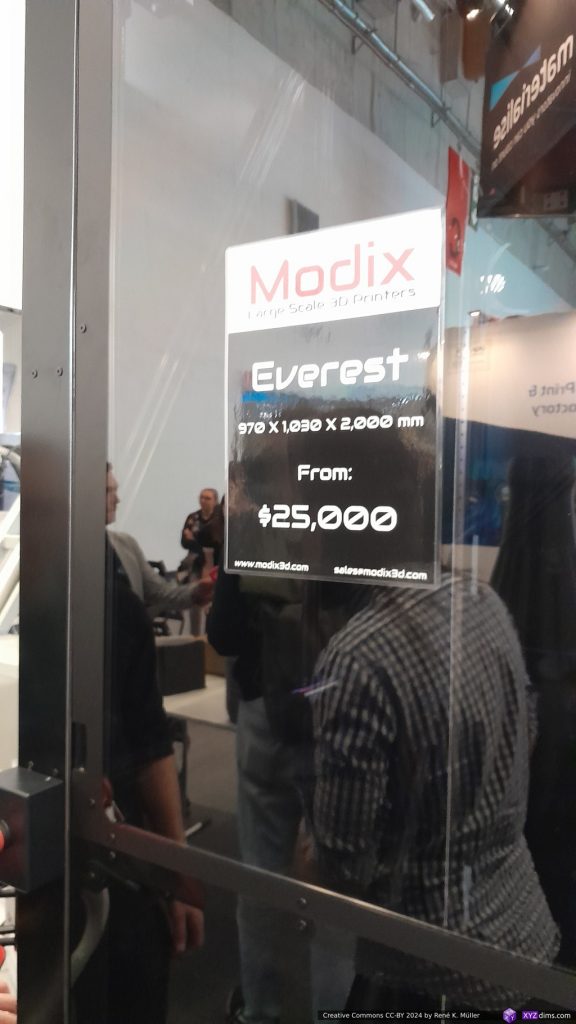

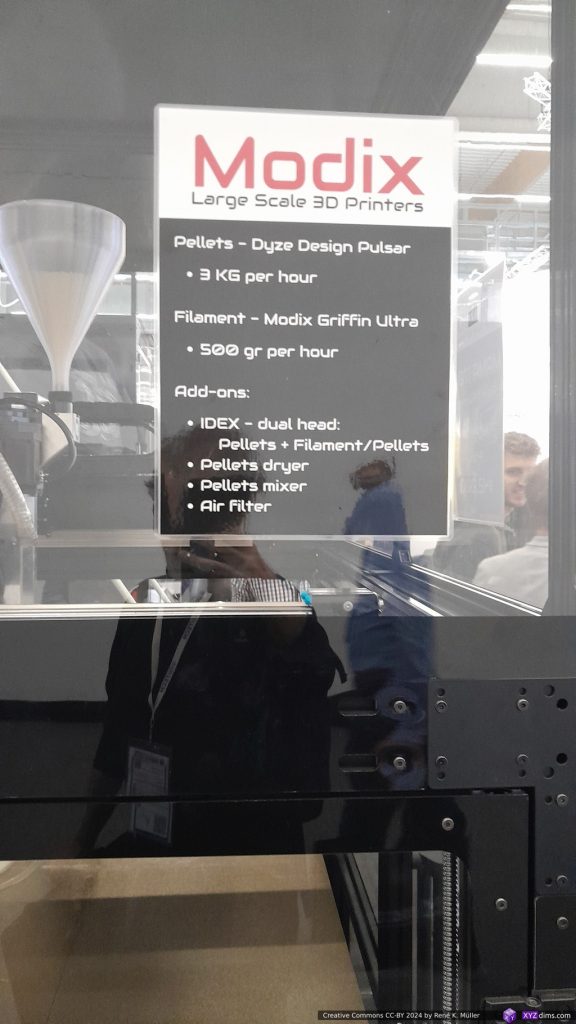
See more at Modix3d.com
Moxin (Huzhou) Tech. Co. Ltd.
The cylindrical shape of a 3D printer caught my attention, and on the 2nd sight I saw it was a Positron-like setup of printing upside down, the Kokoni Sota printer:
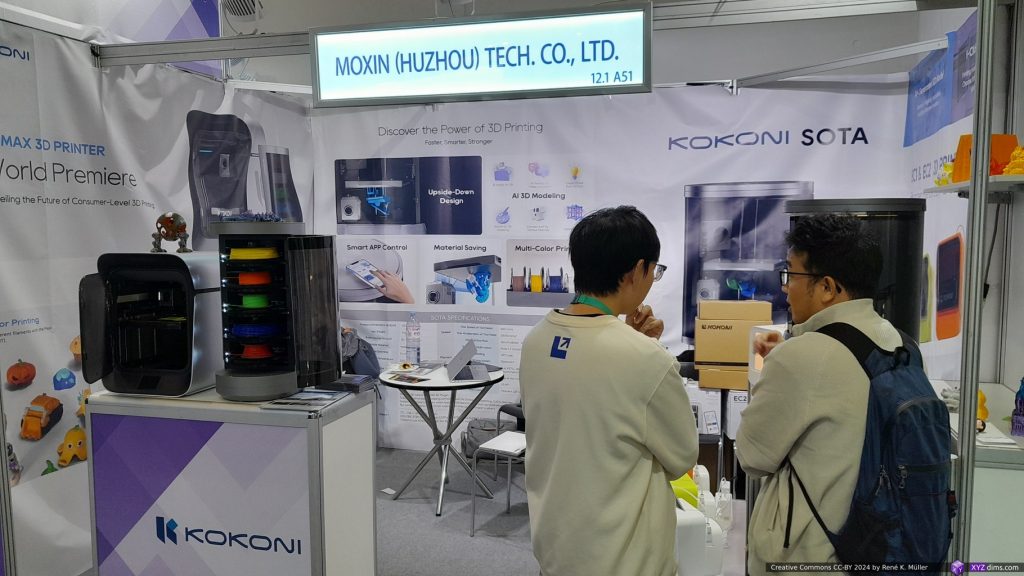
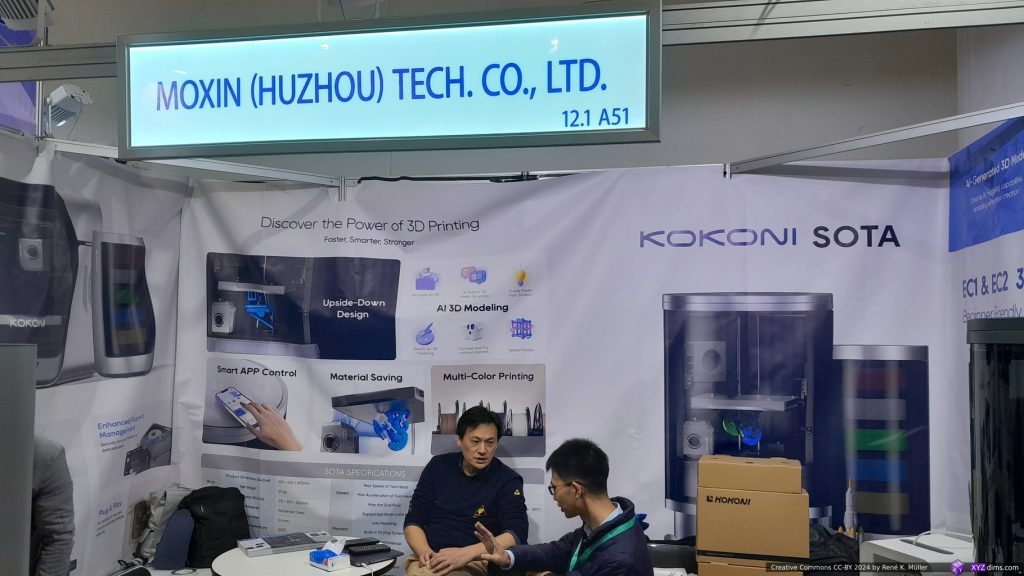
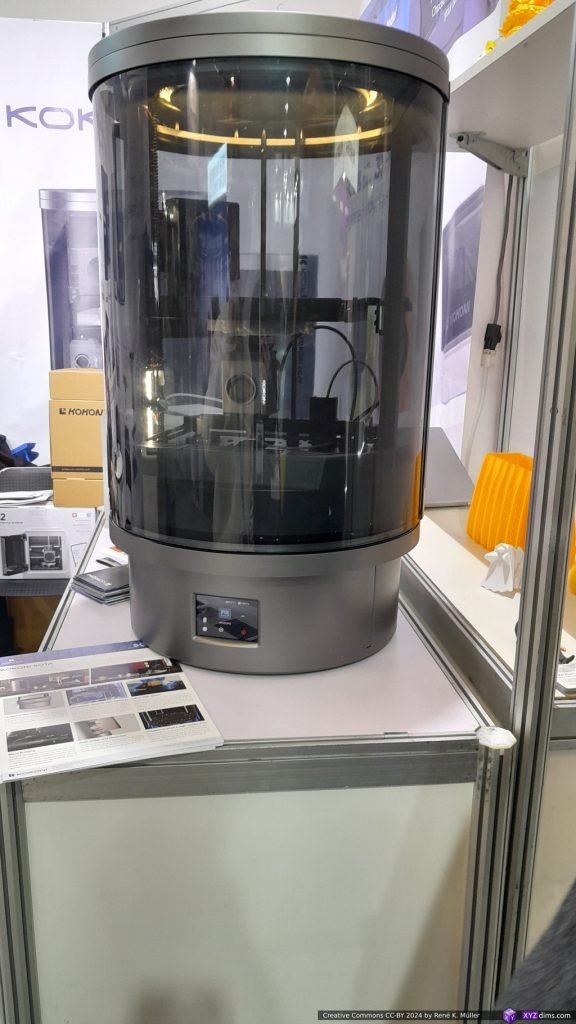
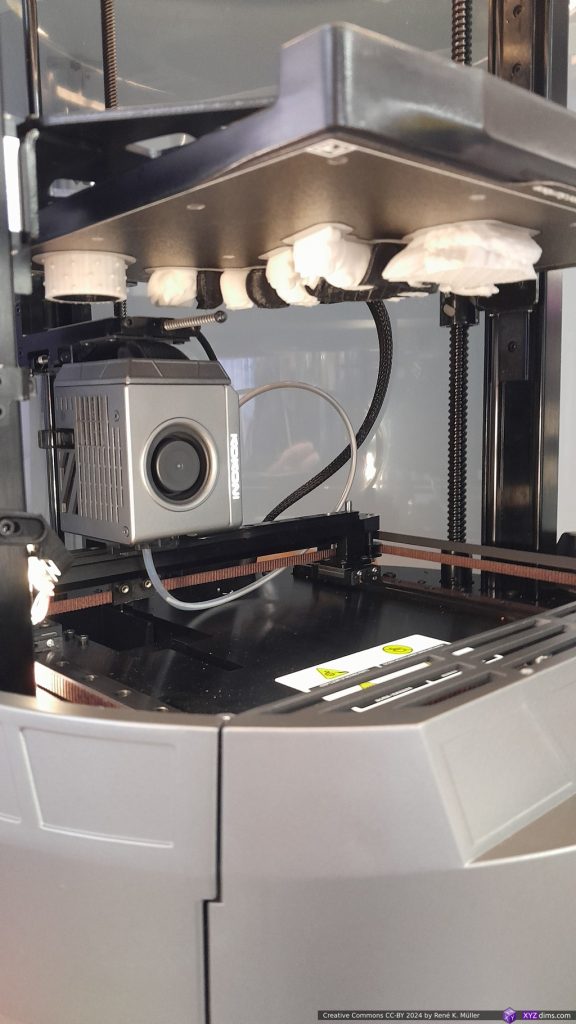
I briefly spoke with Tianrun Chen and he explained when printing upside down, less support material required, and therefore developed their own support generation method which reduces material by 20-50%.
- 210x200x230mm build volume
- up to 300°C nozzle temperature
- optional multi material systems (also in cyndrical case)
See more at Kokoni3d.com
National Taiwan University of Science & Technology (NTUST)
The little booth, and the walls where full of large scale posters with a lot of information, so I stopped and began to absorb the information – in particular the mention of TPMS caught my attention.
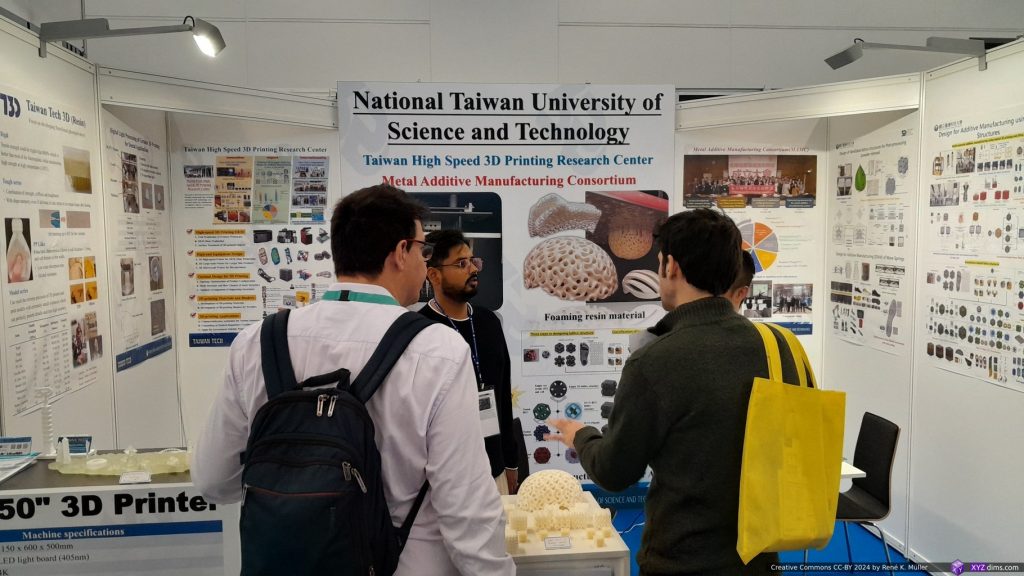
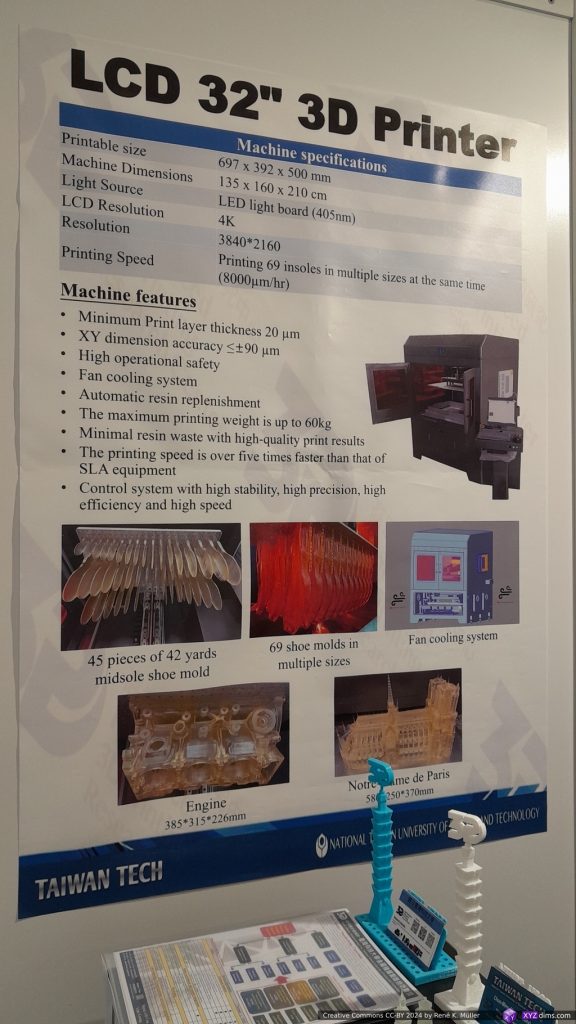
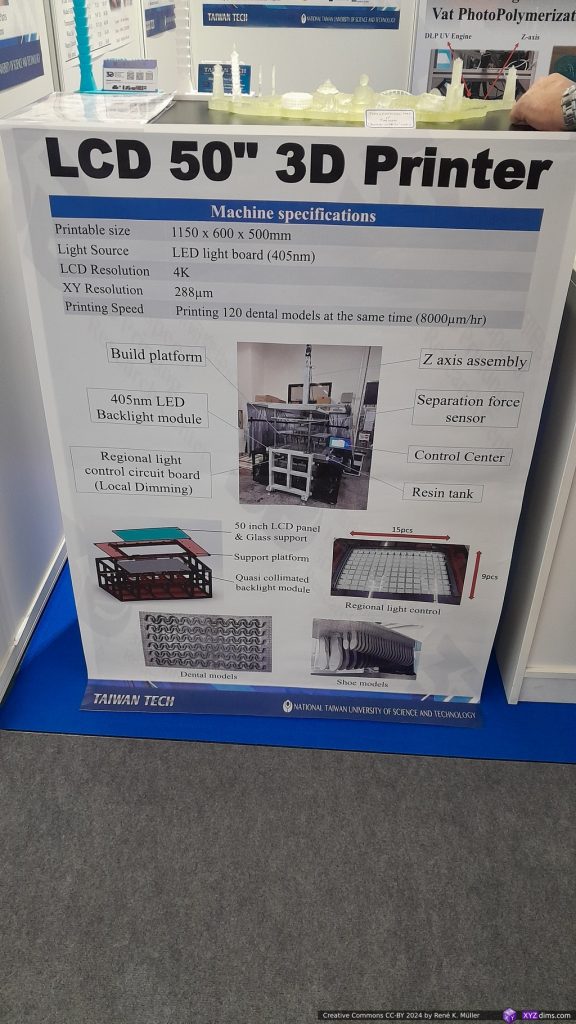
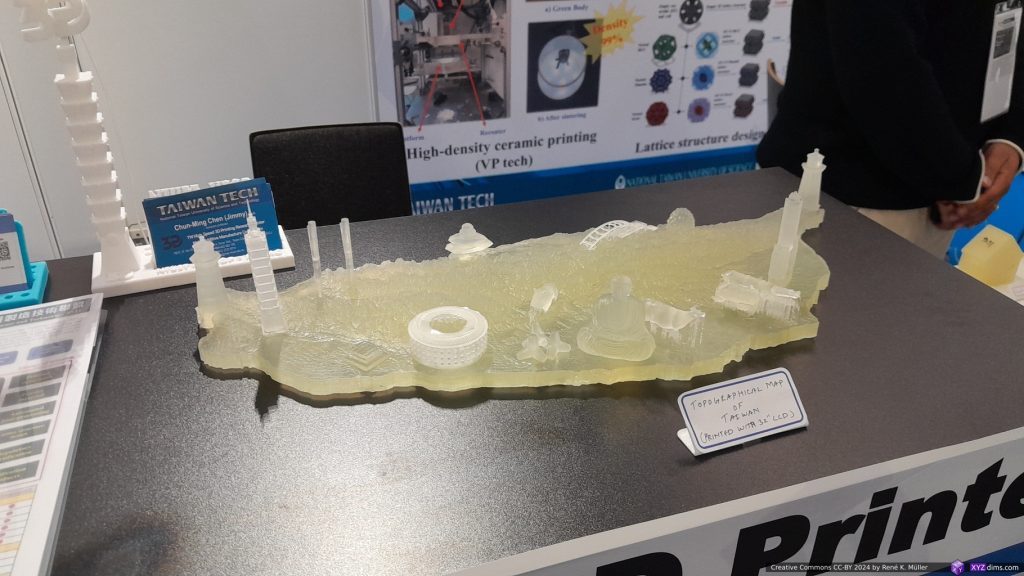
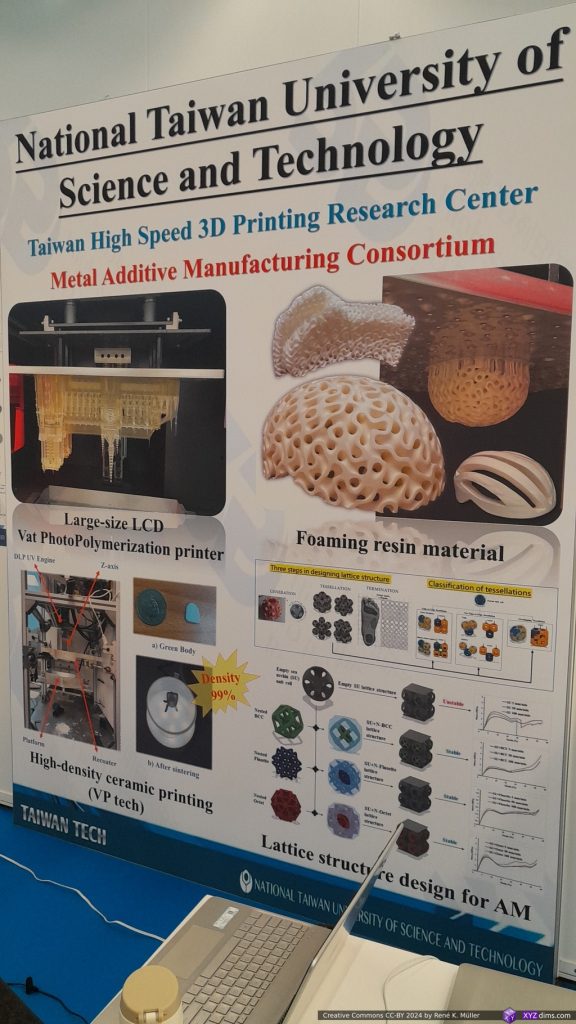

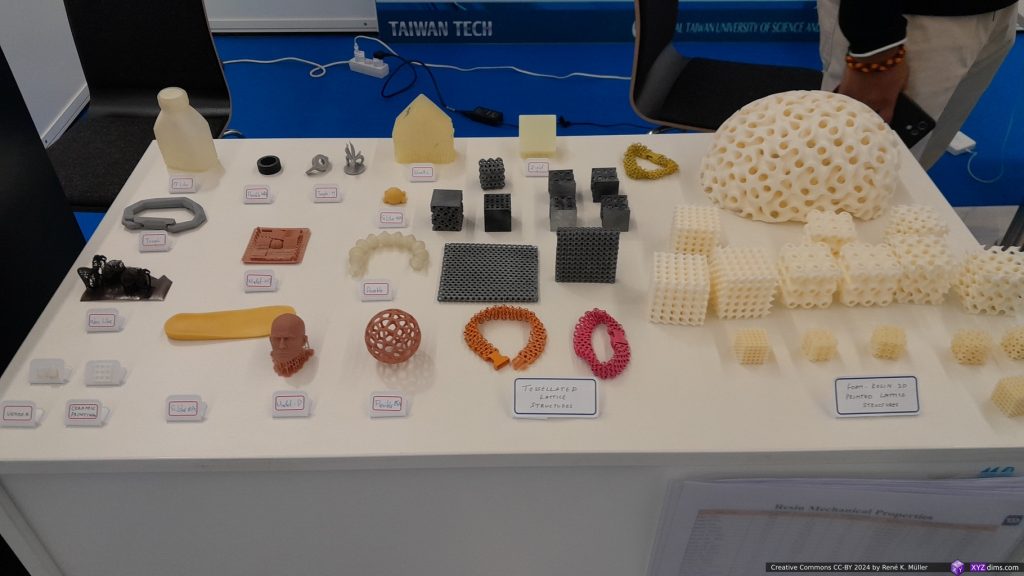
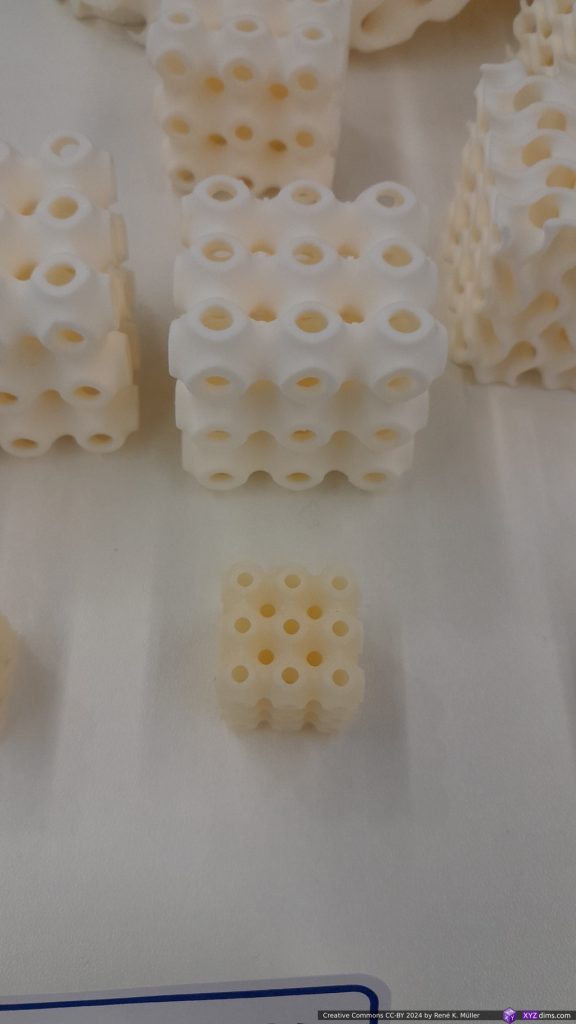
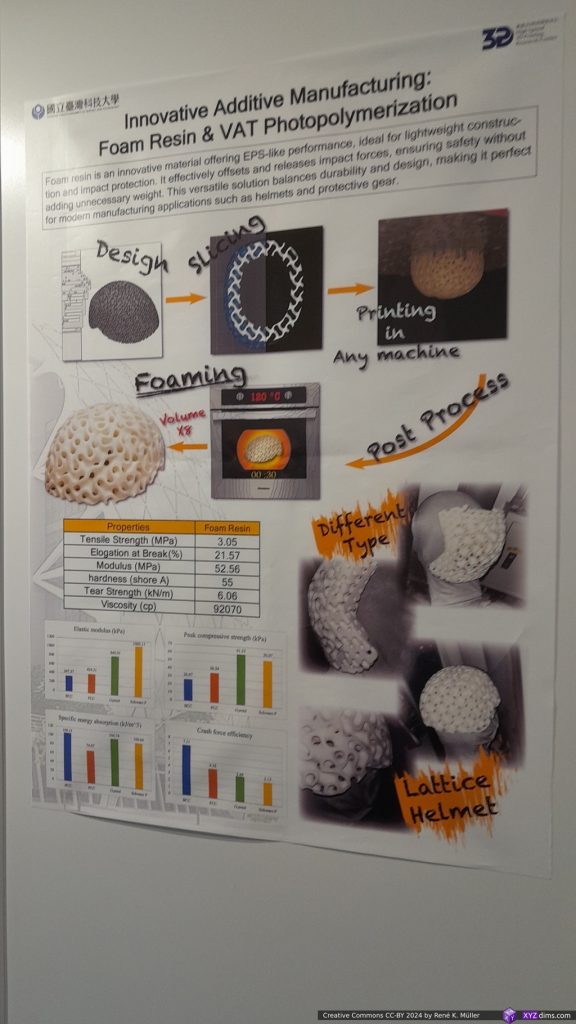
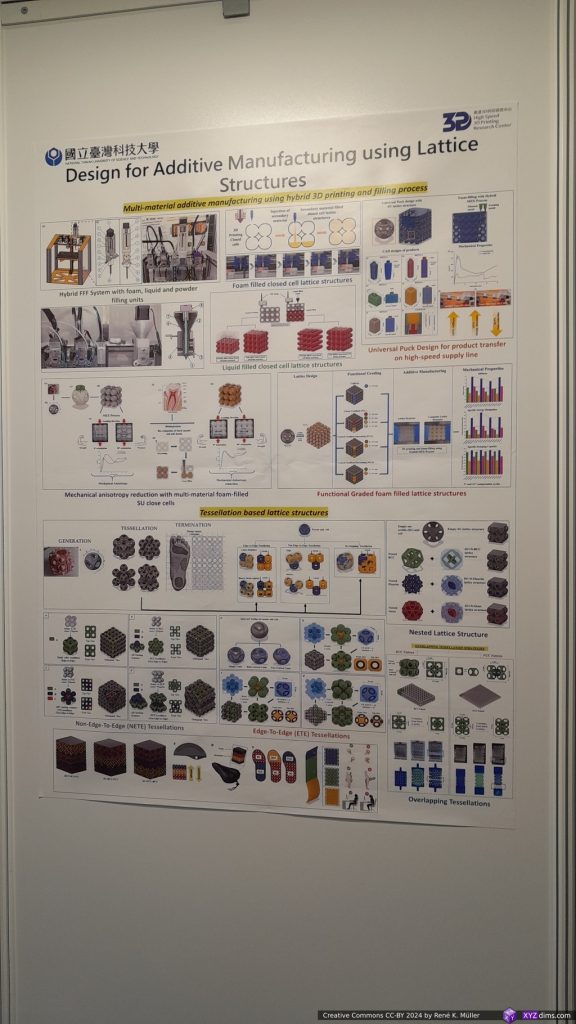
So, one of their invention is a resin which when it is baked at 120°C it increases in size XYZ 2x – therefore in volume 8x – which they named “Foaming Resin Printing“, the sample prints like the bike helmet or even the small TPMS Schwarz P cube was incredible light compared to its size.
Another invention is printing TPMS like Schwarz P and then fill the partial closed P cells with a foaming agent, they call this process “Multi-Material Additive Manufacturing using Hybrid 3D Printing and Filling Process” (see non-free paper) – in case of the Schwarz P TPMS the cells are interconnected and spherical, so the agent flows into all captivities quickly as “Liquid Filled Closed Cell Lattice Structures” – and reduces print time while increase stiffness / strength – kind of combining Additive Manufacturing with Mold Injection method.
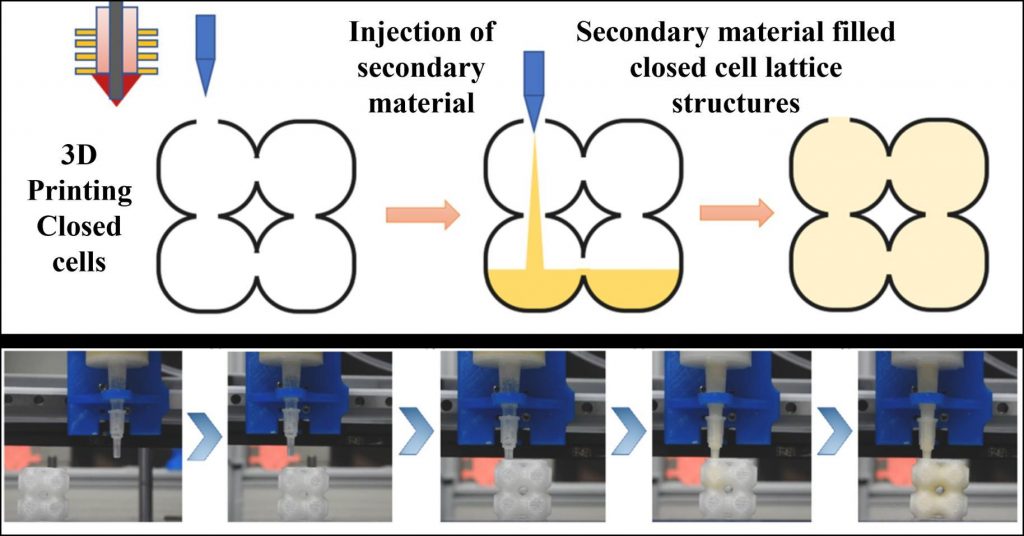
Another achievement is their 32″ (697x392x500mm build volume) and 50″ (1,150x600x500mm build volume) large LCD/MSLA resin printers, with new film coating of better release of the cured layers, although we couldn’t get into the deep details of it. See this non-free paper and this paper for details about the 32″ resin printer.
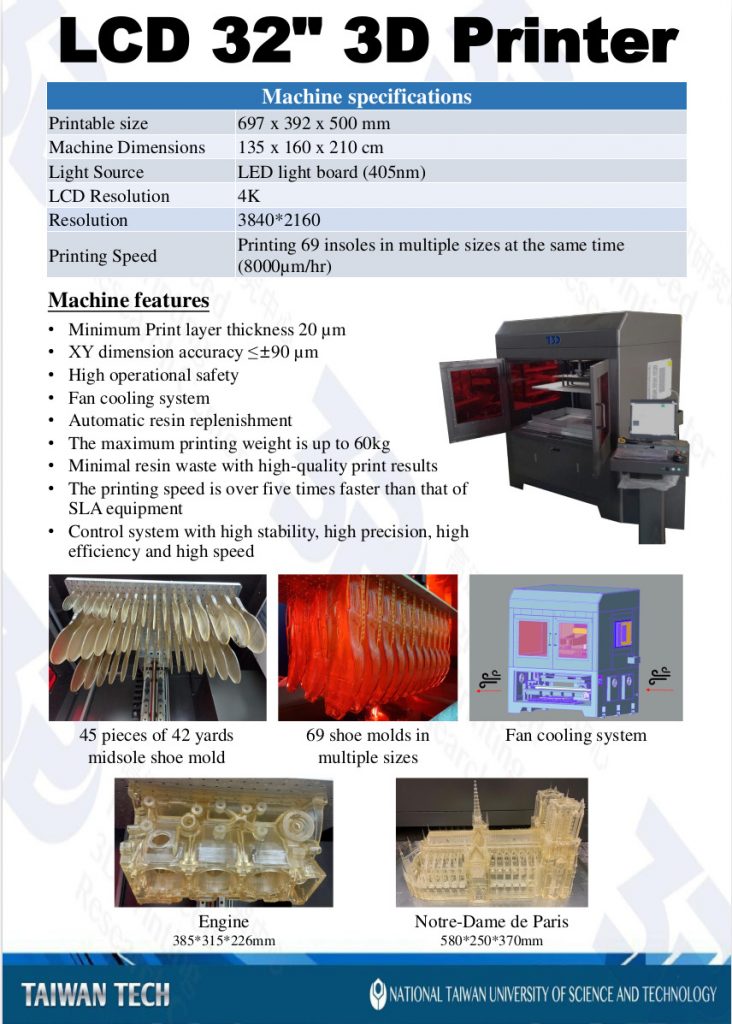
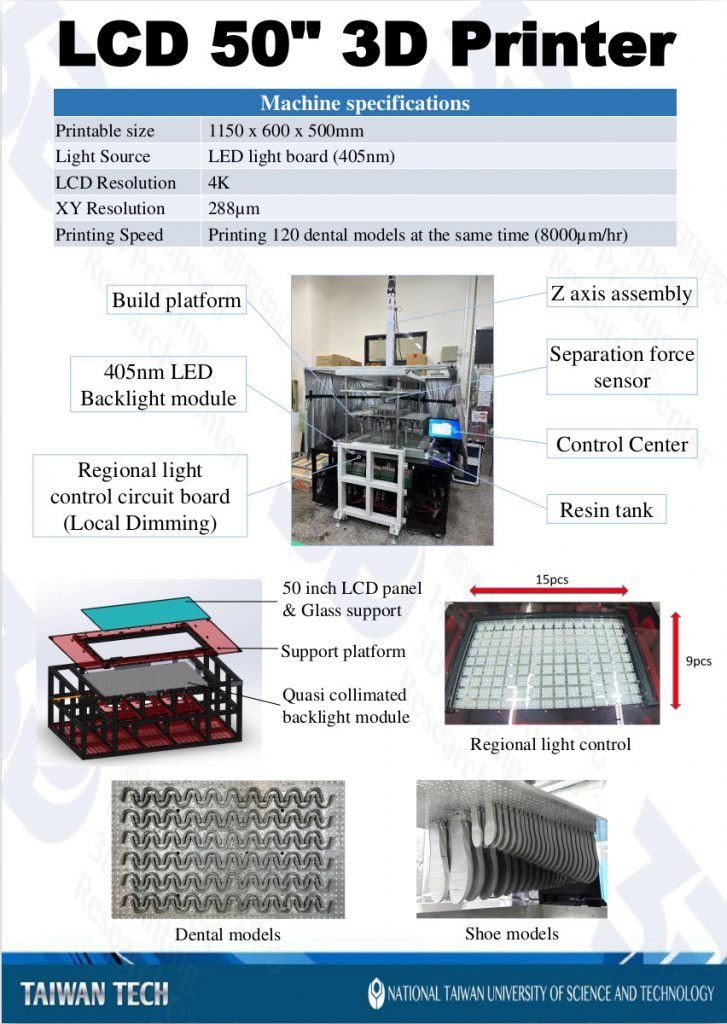
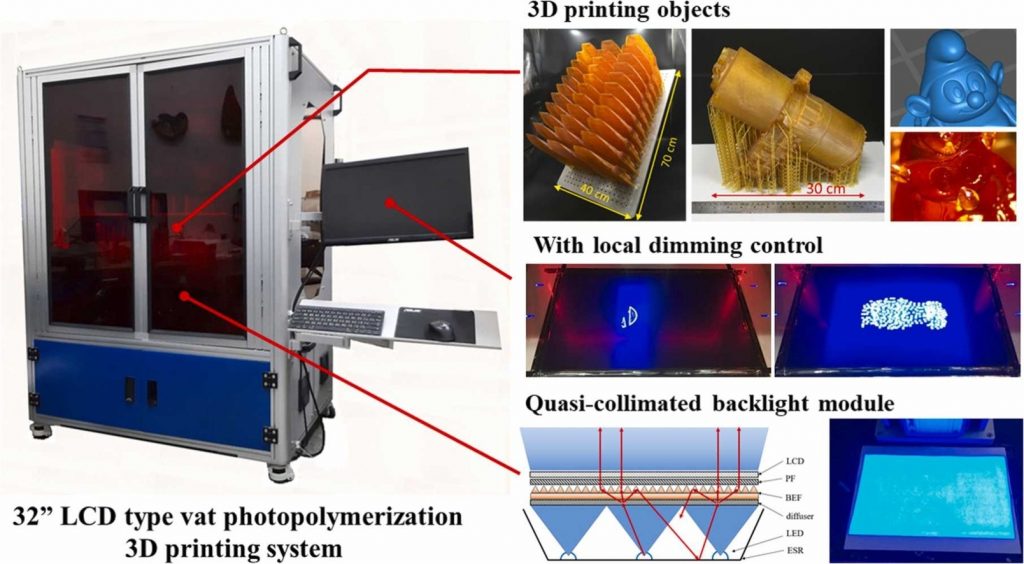
I could easily spent an hour to explore their different projects and the benefits of those 3 distinct inventions alone. See more at NTUST.edu.tw and its High Speed Printing research center, in particular follow Mayur Prajapati.
TUM (Technical University of Munich)
The TUM had a very prominent and large booth with many departments and many samples shown:
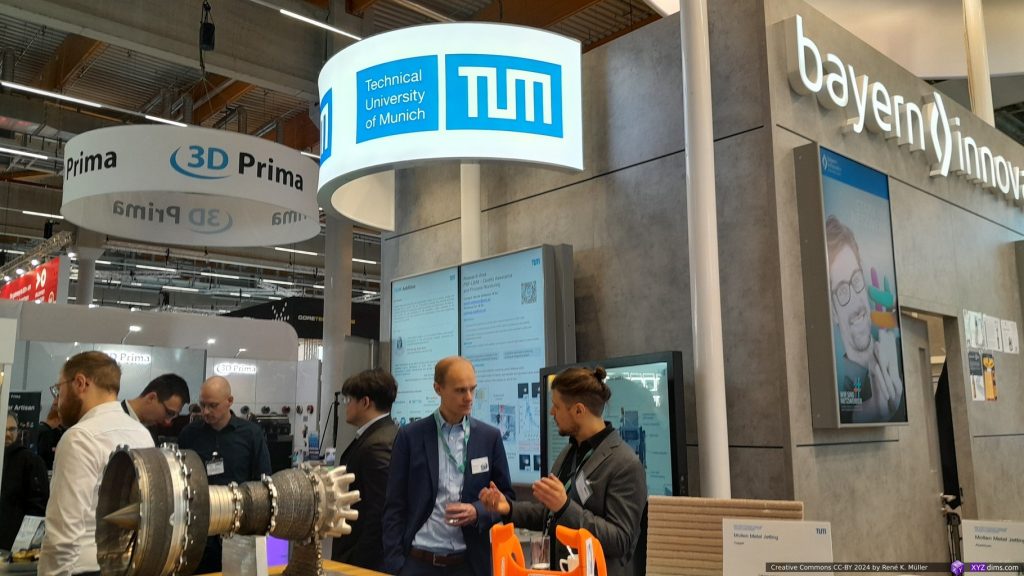
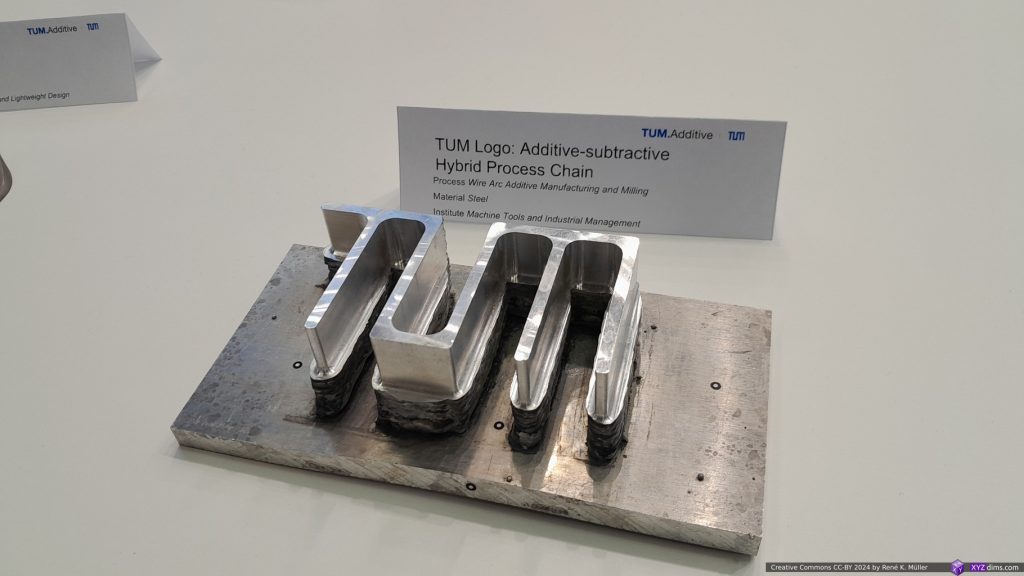
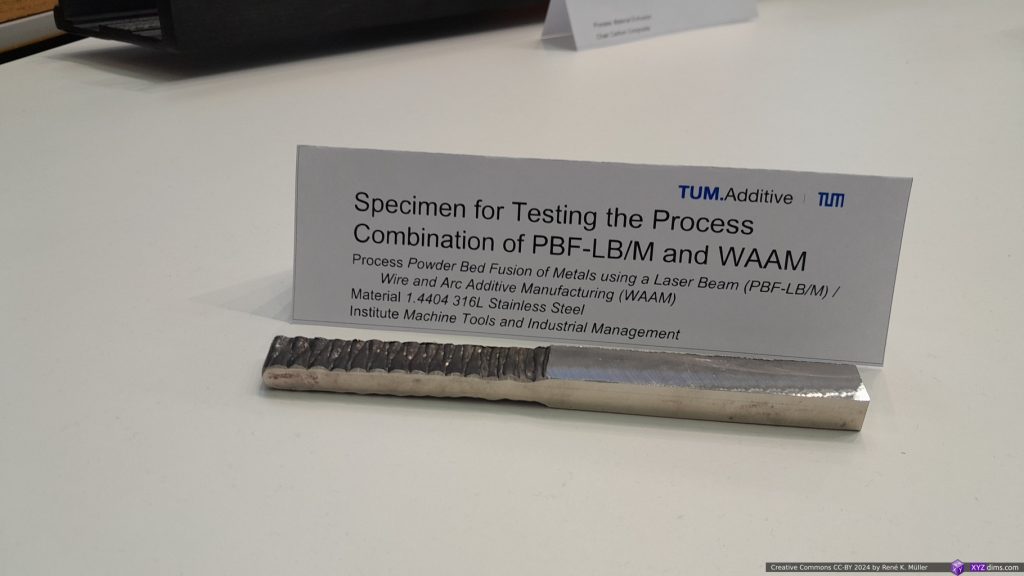
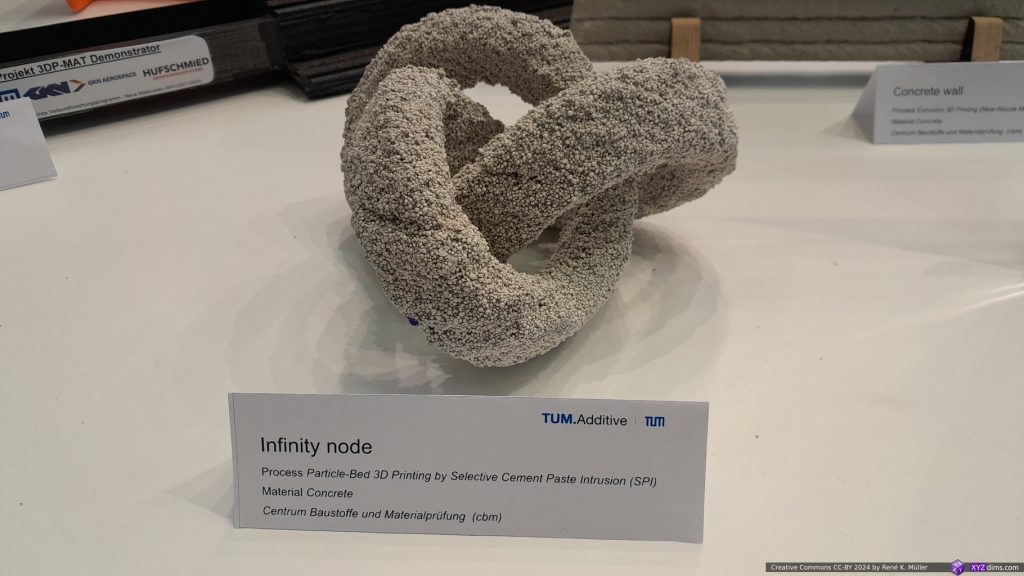

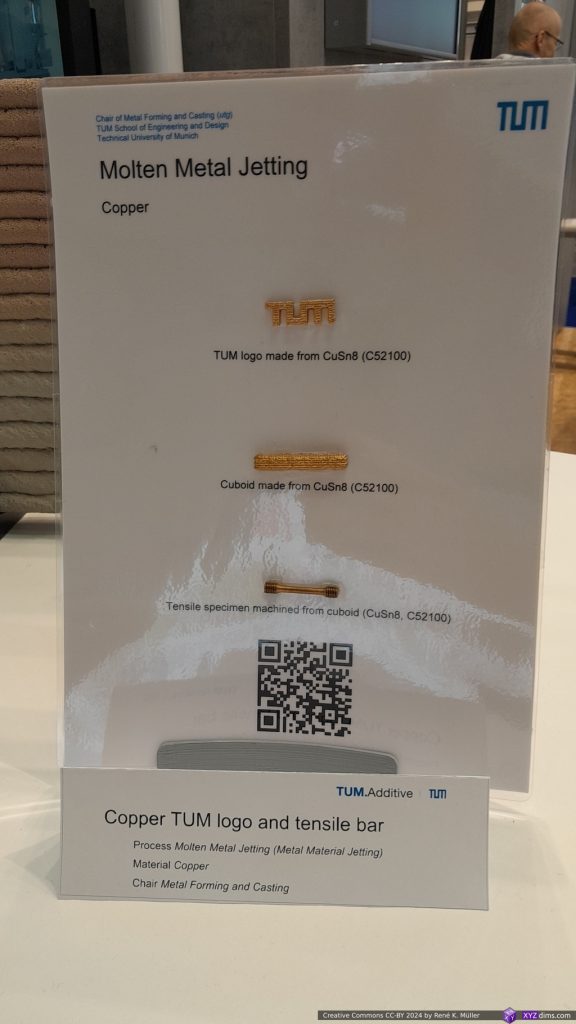
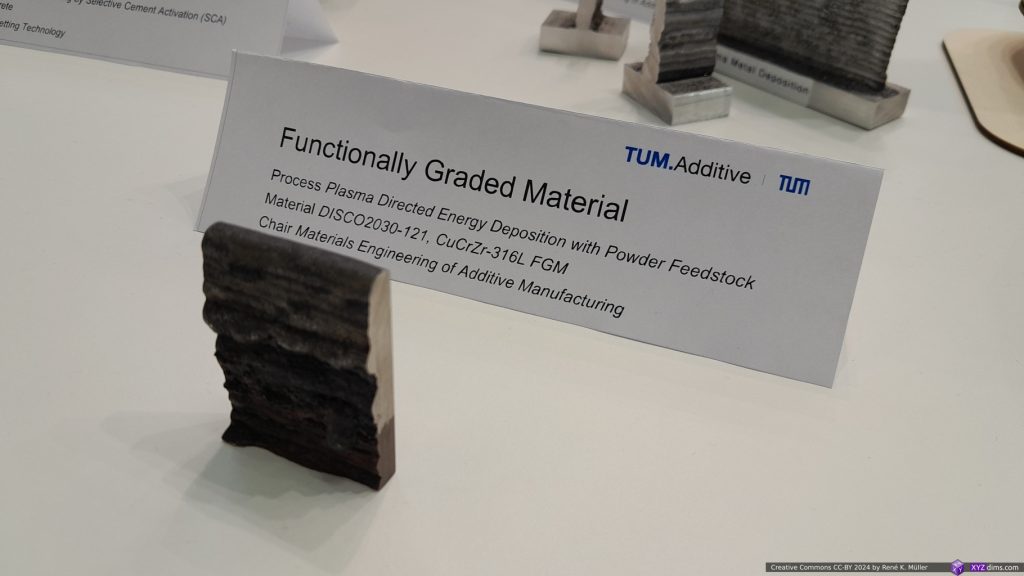
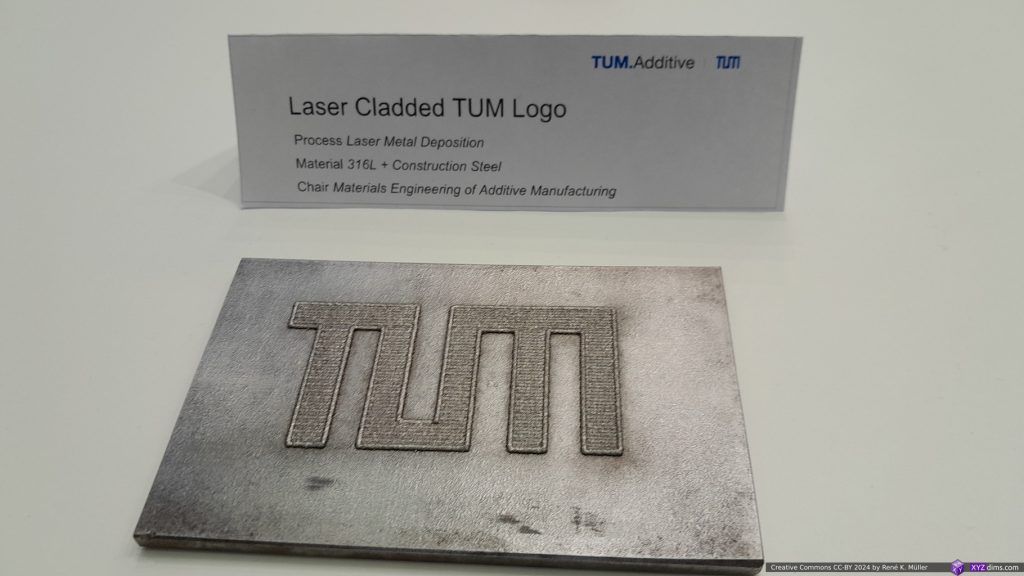
What caught my attention was the “Infinity Node” made from ~1mm gravel, it was printed using SLS-like printing: Particle-Bed 3D Printing by Selective Cement Paste Intrusion (SPI), using concrete as a binder to connect the small gravel together. The “Force-flow Optimized Node” (brown triangular truss shape) was done using Particle-Bed 3D printing by Selective Cement Activation (SCA).
The other samples were “Molten Metal Jetting” (Copper), “Functional Graded Material” using Plasma Directed Energy Deposition with Powder Feedstock, and “Laser Cladded TUM Logo” using Laser Metal Deposition (316L + Construction Steel).
See more at TUM Additive
Quantica
Quantica caught my attention 2-3 years ago, also at the Formnext, as I saw the modular fully voxel-exact jetting of material. Their core business was their printhead “NovoJetTM” able to print high viscous materials, something other jetting printheads would not able to do.
This year I talked to Sven, and he explained to me that they broaden their application areas like exact glue jetting and other high viscous materials, as some industries saw their printheads as high precision material deposition, outside of the “3D printing / Additive Manufacturing” use cases – quite interesting how their core expertise found other applications.
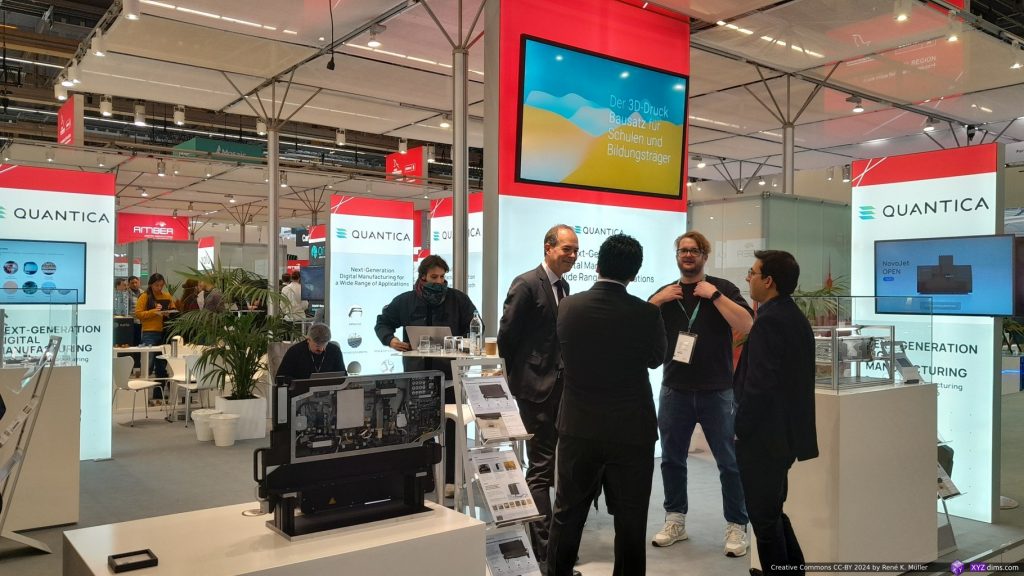
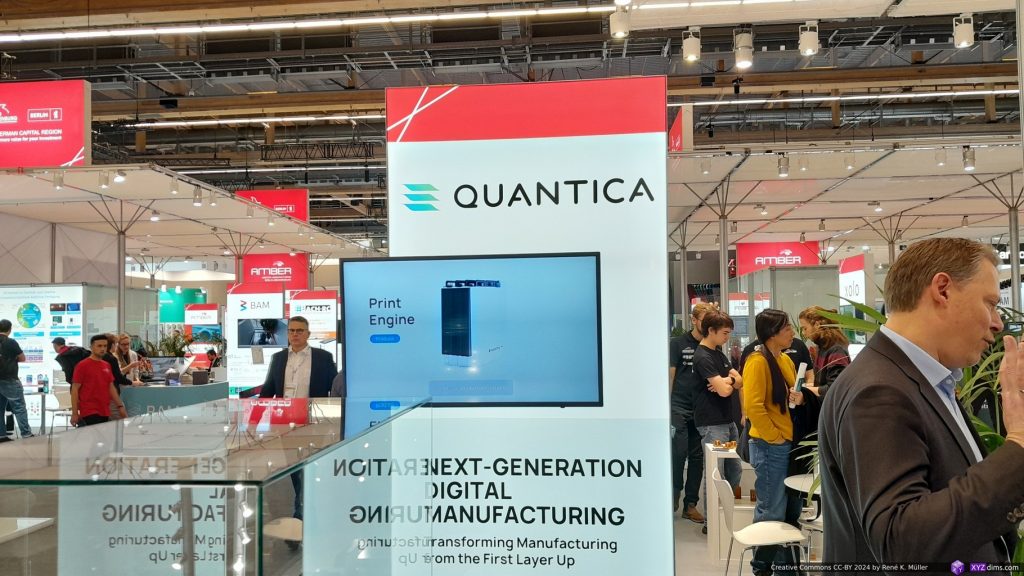
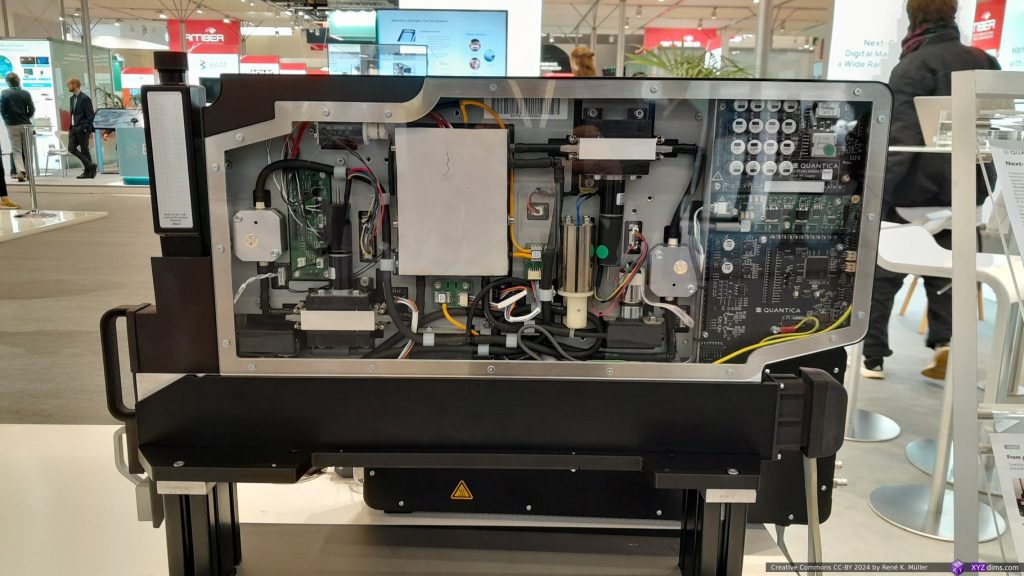
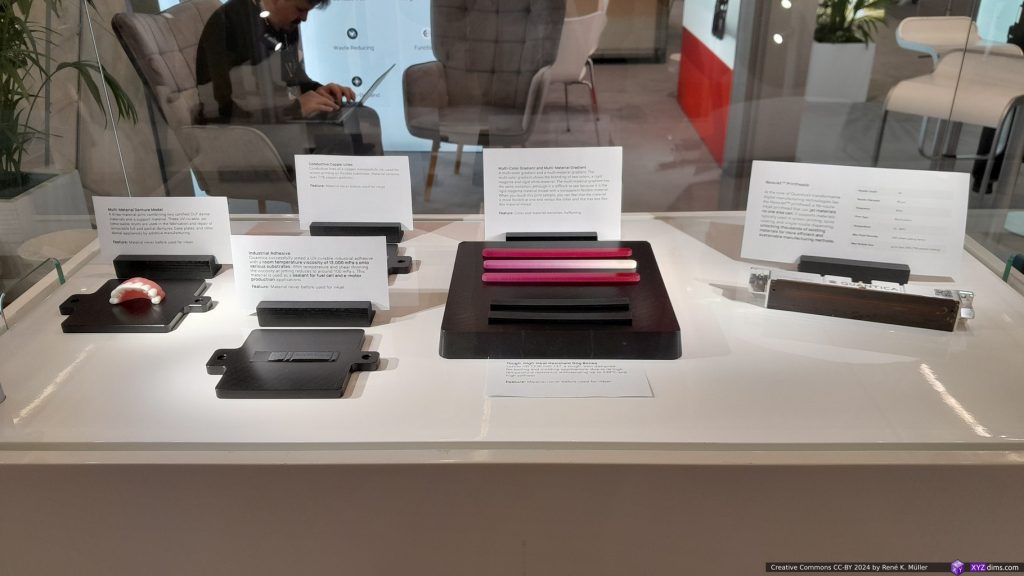
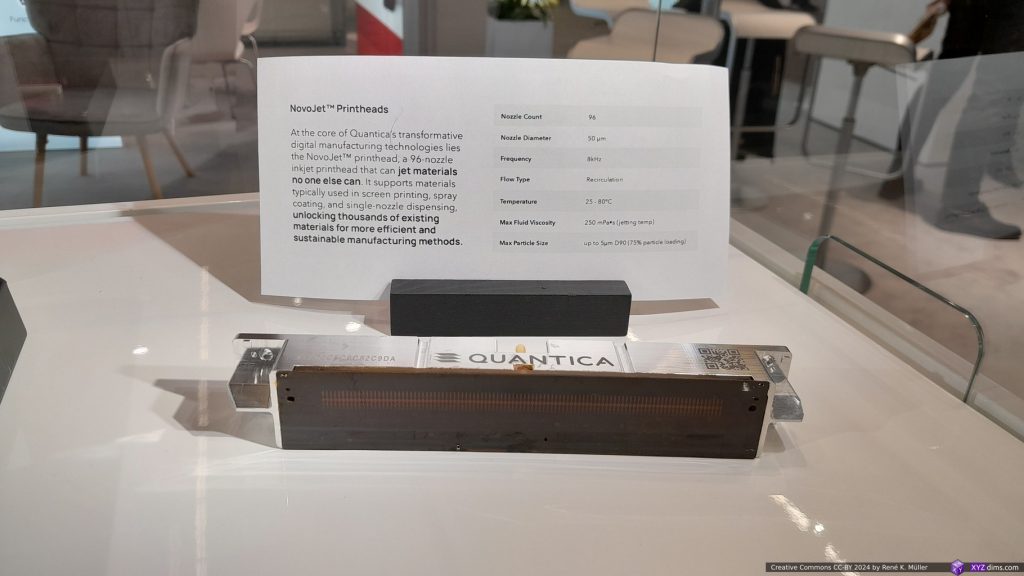
Again I asked for some 3D printed samples, and again I was denied any like the past 2 years (!!) – they said they don’t have any (or very few) but just for internal use; my main interest is to observe the actual blend or non-blend and then 3D dithering of materials and colors on drop level in order to explore new applications.
See more at Quantica.io
Xolo with Xube2 & Xell Printer
An interesting approach, new to me, is Xolography, spatial printing in a resin – first a light sheet is established in the Z plane of 50um thickness, and then XY image is projected into the volume, different color/wavelength for each, and where the Z plane and the XY image light meet, there the photopolymerization takes place; it only works with highly transparent resins, more precisely dual-color photoinitiator (DCPIs), as otherwise the Z plane won’t reach all XY 2D image.

- first wavelength (375 or 405 nm, UV light) activates the dormant initiator by triggering a spiropyran photoswitch (Z plane)
- second visible wavelength (450-700 nm, visible light) excites the benzophenone component to initiate polymerization (XY plane)
So far they reached 50x89mm XY size, yet any size in Z including continuous Z printing.
They claim “no layer lines”, and told me they project a “video”, yet, a video has also n-amount of images e.g. a certain frame rate. What they rather mean is a continuous Z motion while they project their Z sliced XY images, and because the Z motion is continuous, the “layers” rather blend together and get smoothed out. They also don’t need any support structures, as the cured/solidified structure stays in-place and doesn’t sink.
Their requirement of highly transparent resin they derive one of their main use cases: 3D printed optics, and isotropic properties (angle independent strength, no deliminations), other resins they developed are bio-compatible and even soft and gel-like – quite an impressive achievement.
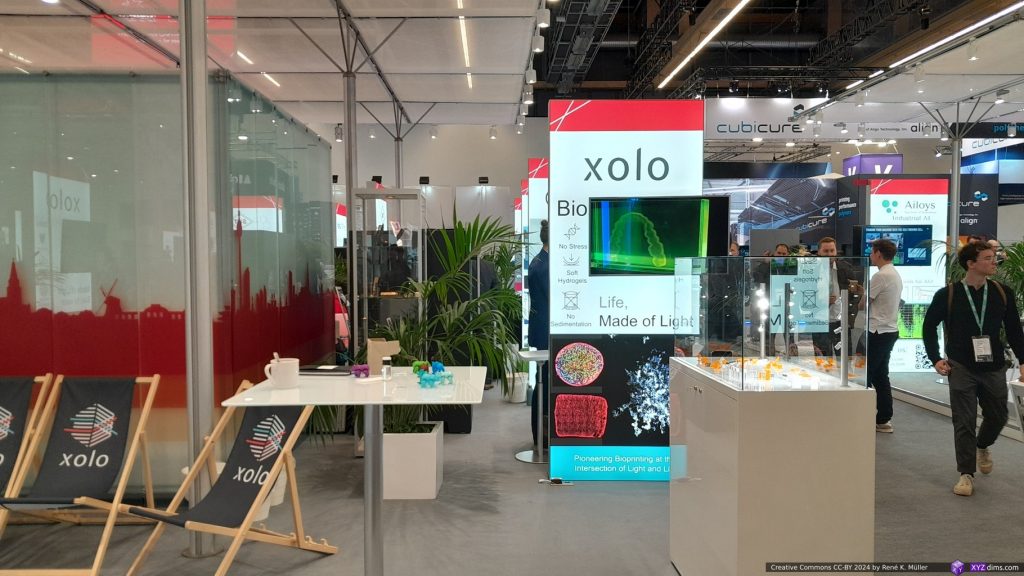
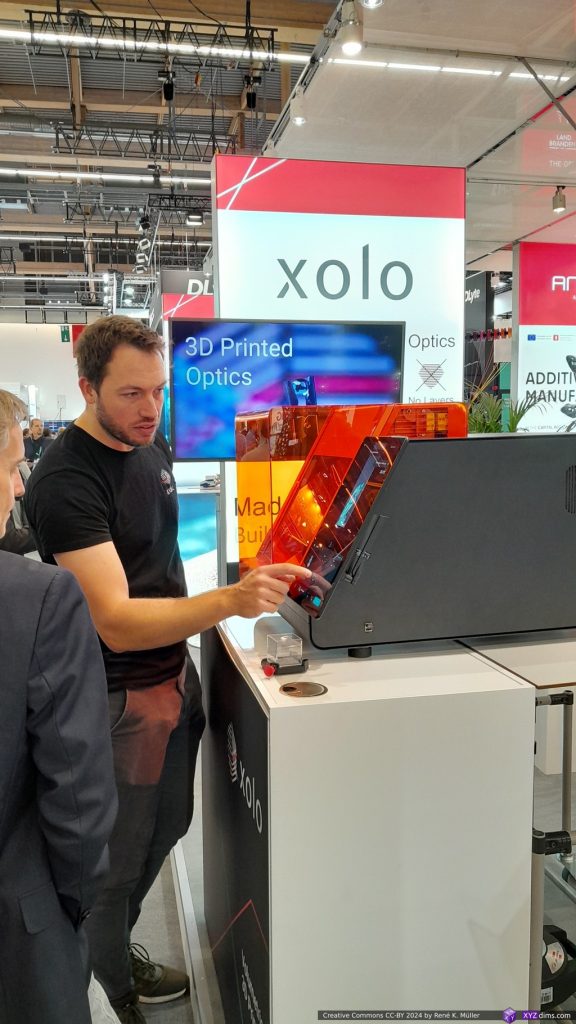
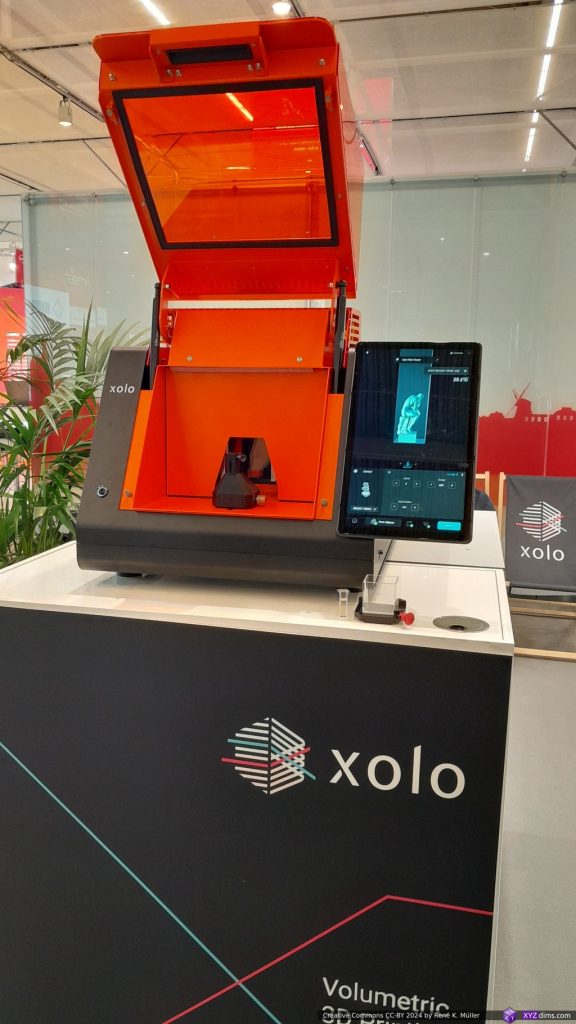
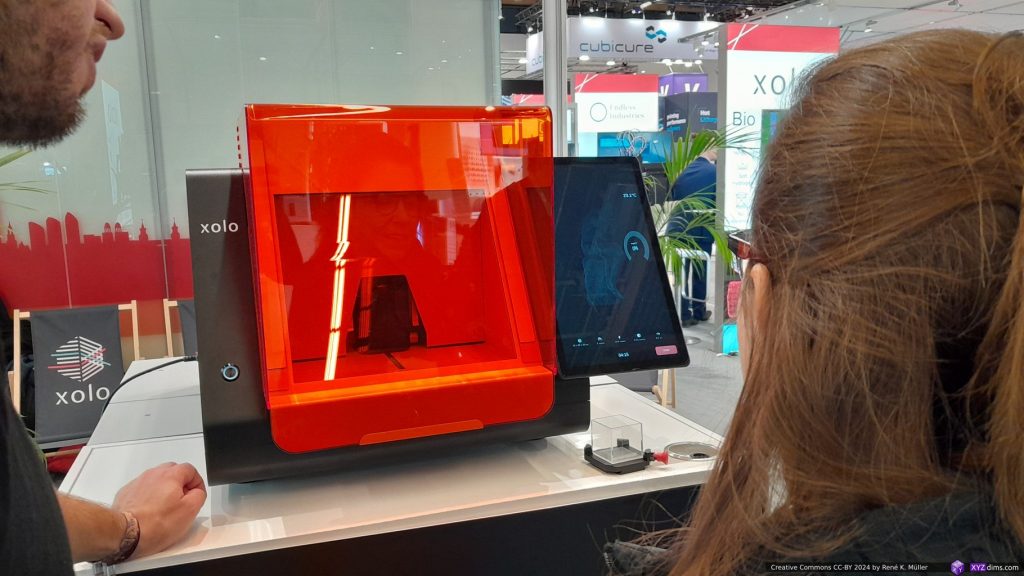
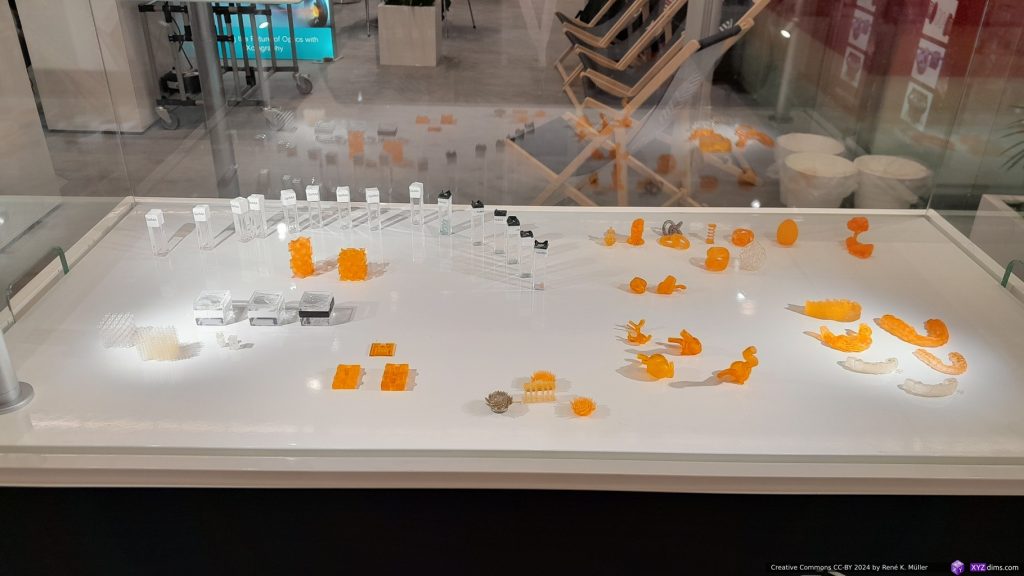
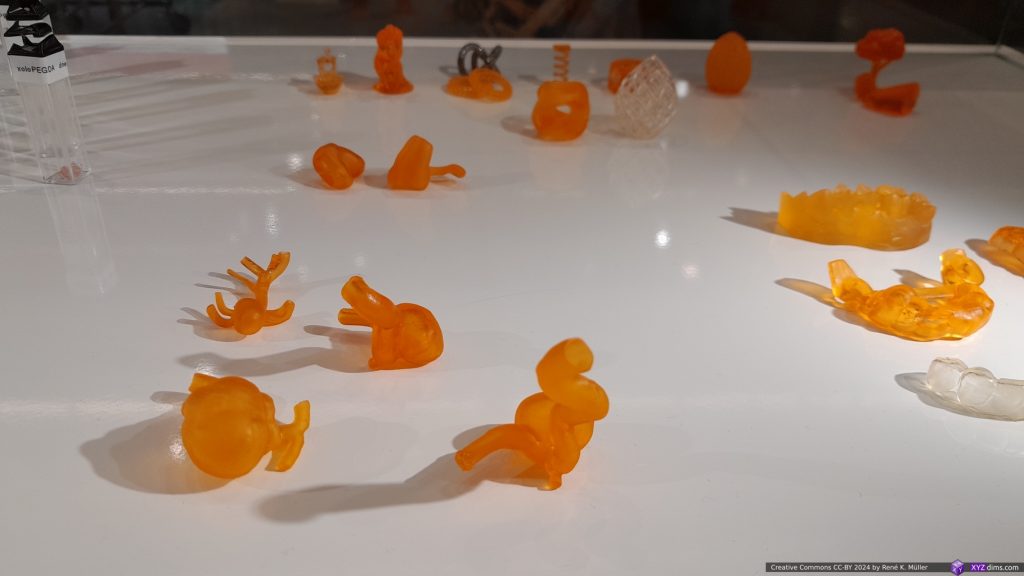
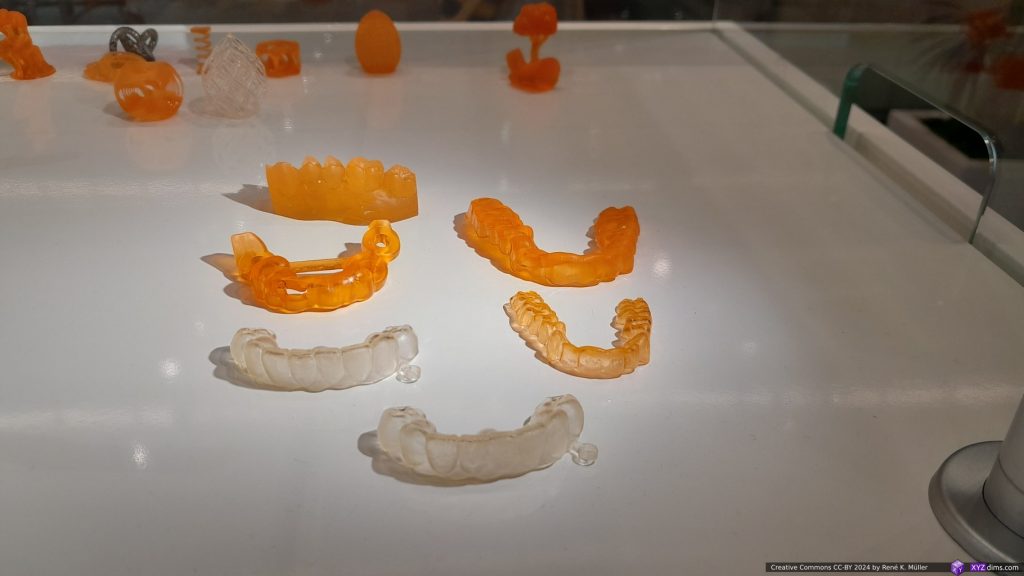
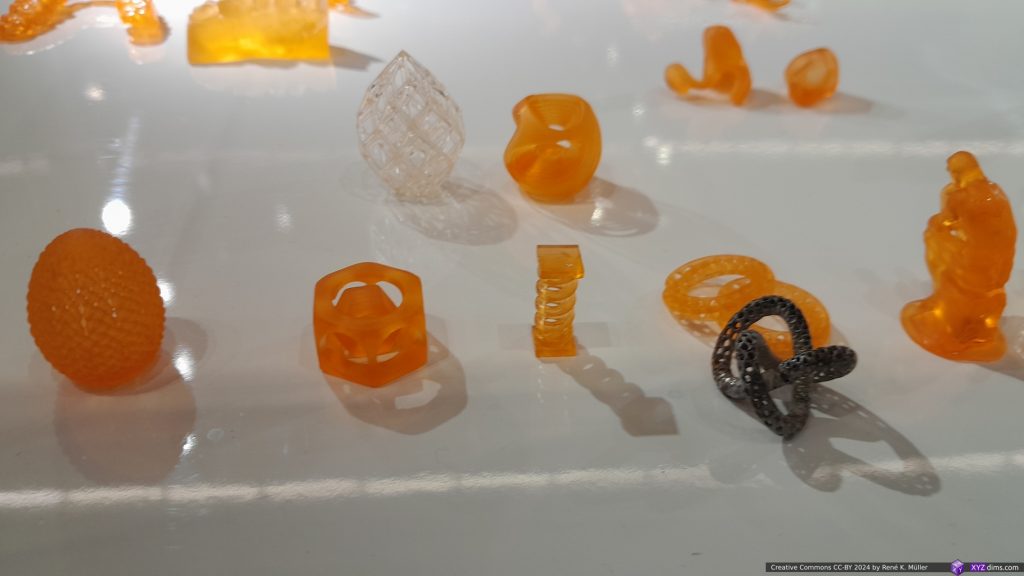
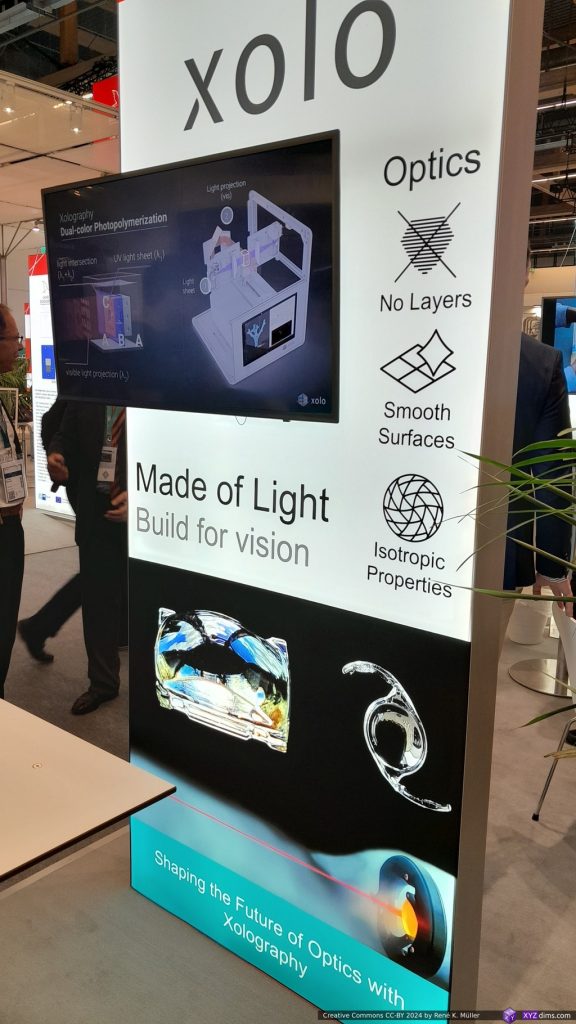
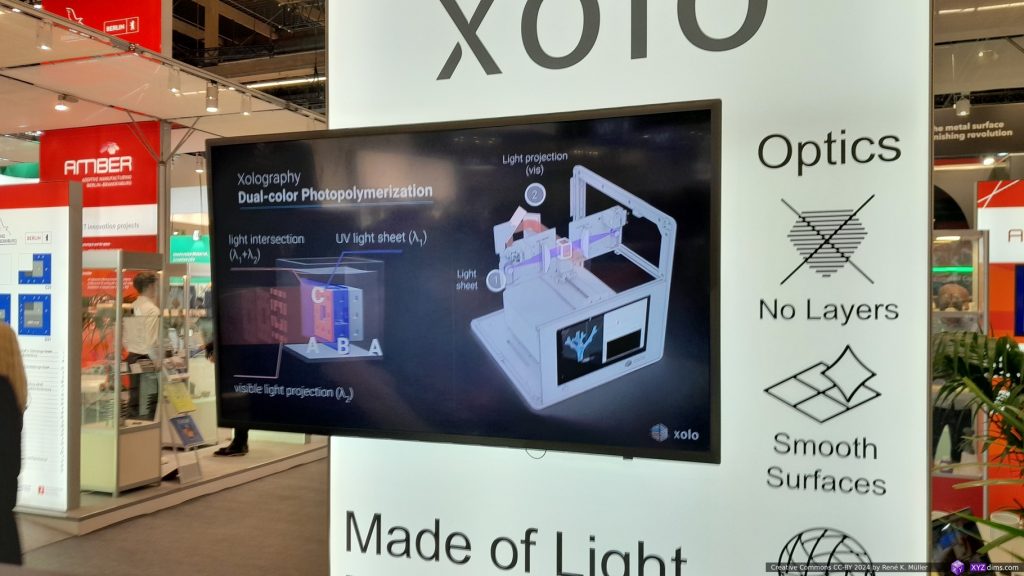
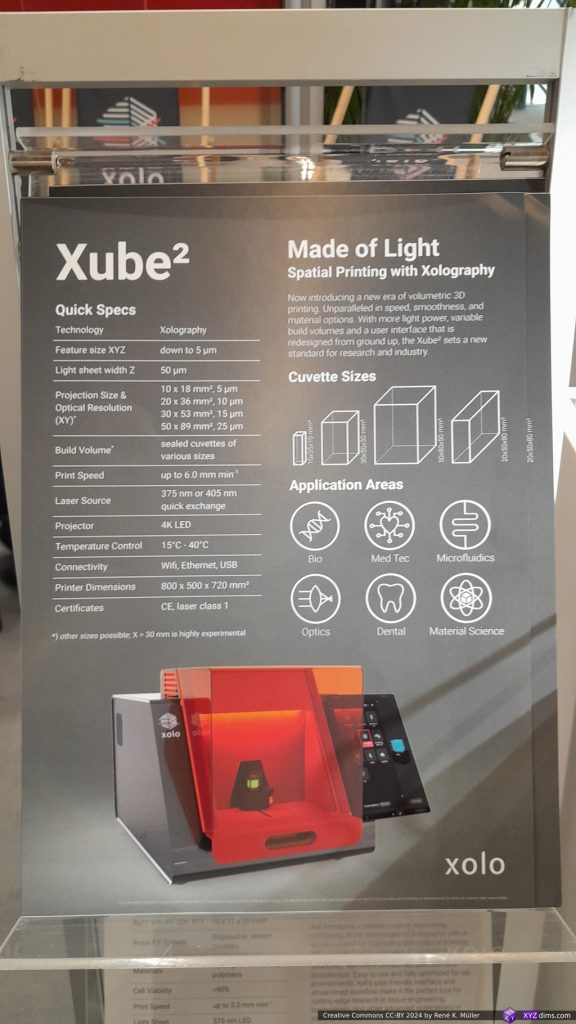
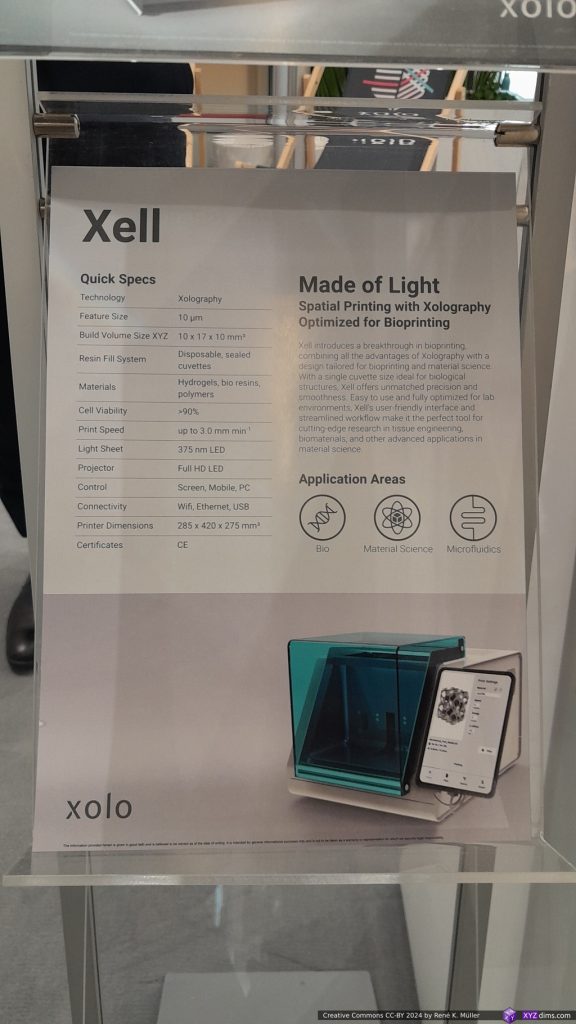
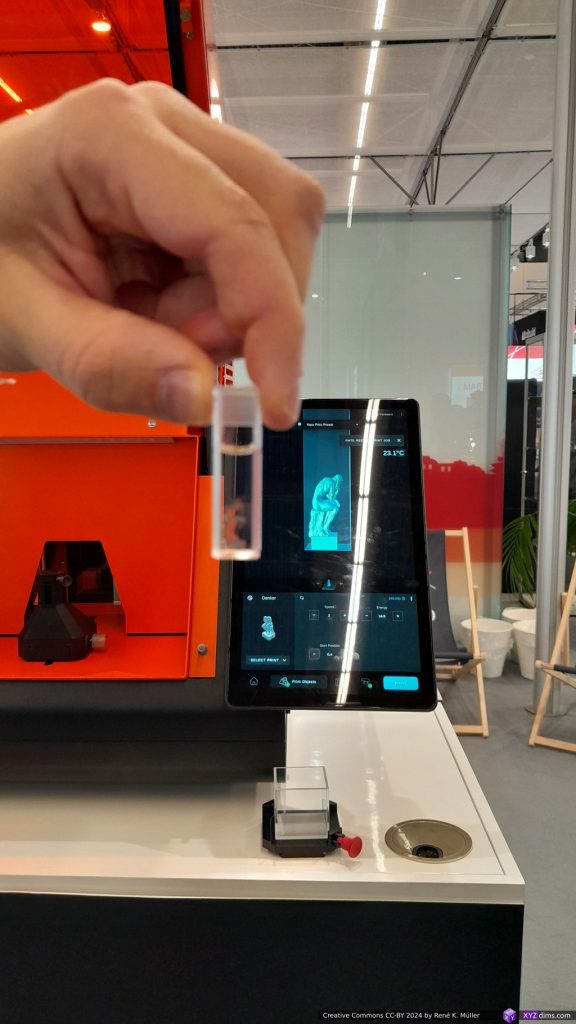
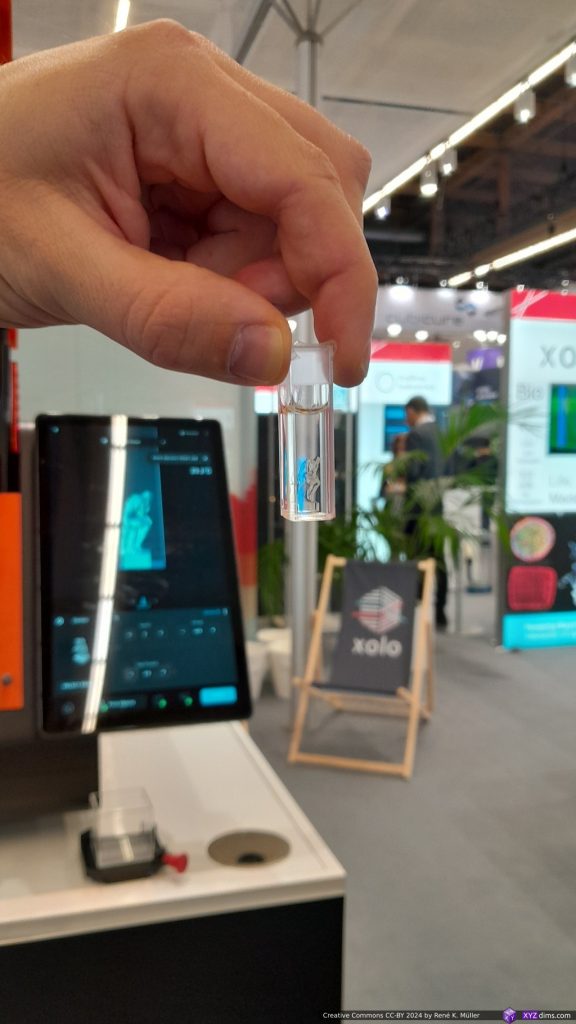
Currently they have two machines available:
- Xube2: 10x18mm (@5um feature resolution) up to 50x89mm (@25um feature resolution) x80mm, apprx. 6mm/min in Z, feature size 5-25um as mentioned, although 50um lightsheet width/thickness, so the “feature size” more applies to XY than Z
- Xell: 10x17x10mm build volume, @10um feature size
This process has been new to me as mentioned, but while researching I realized it has been around since 2020 or so, when this paper was published.
See more at Xolo3d.com; see also a section of Joel Telling (3D Printing Nerd) Formnext 2024 stream.
Asahi Kasei
They showed a bio-attributed Cellulose Nano Fiber (CNF) made from cotton fibres, and then reinforced polyamide PA66 into a filament named CNF/ECONYL® Polymer with extended heat resistance, strength (performing better than carbon fiber), smoothness and formability – actual details of measurements are missing to backup those claims – according their announcement the material becomes available in Q3 2025.
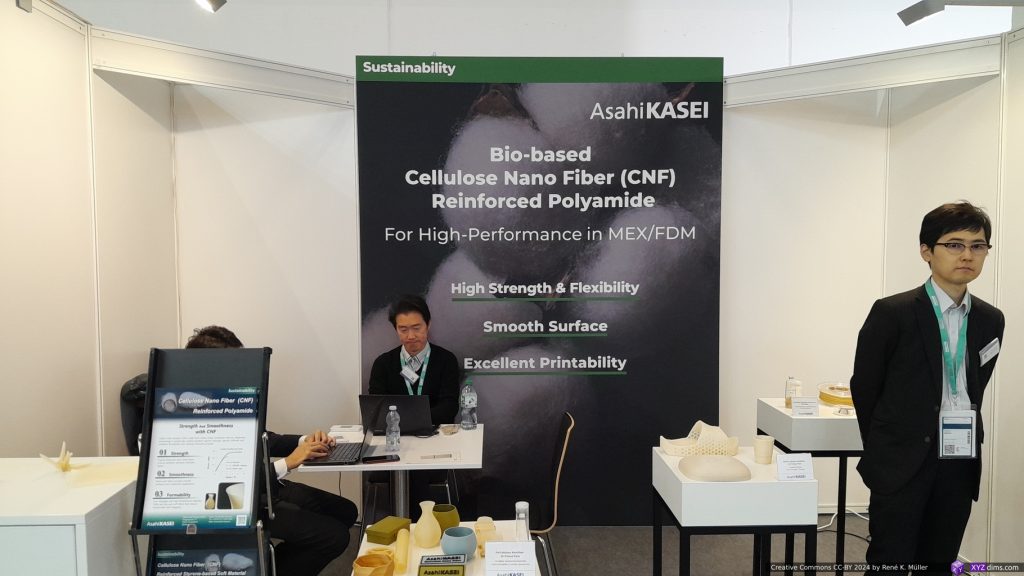
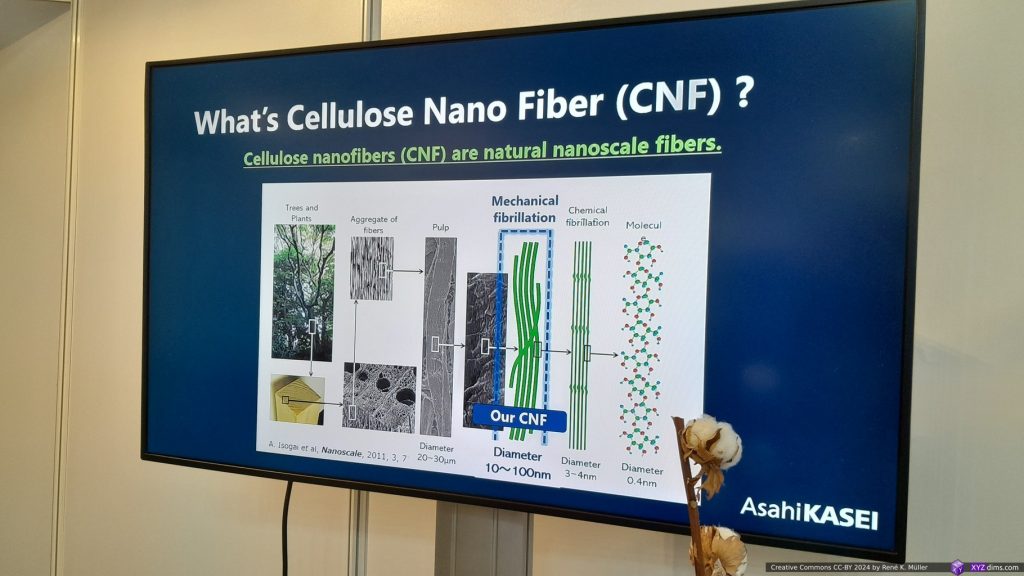
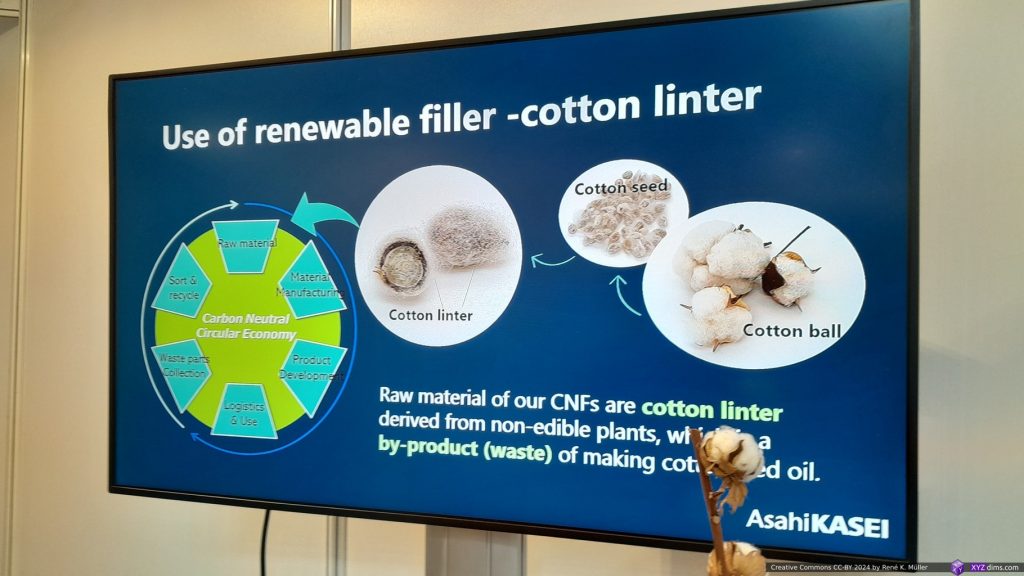
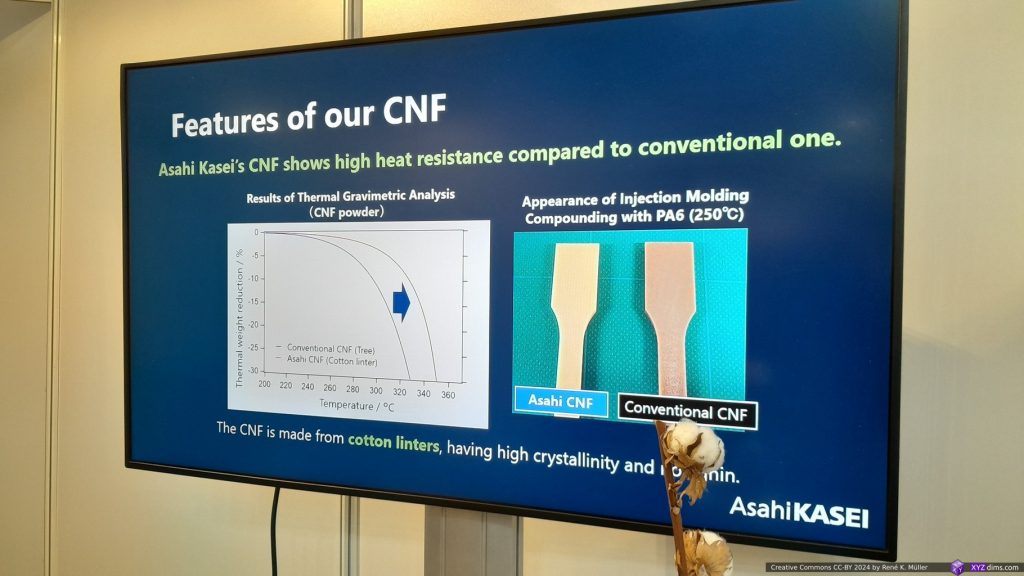
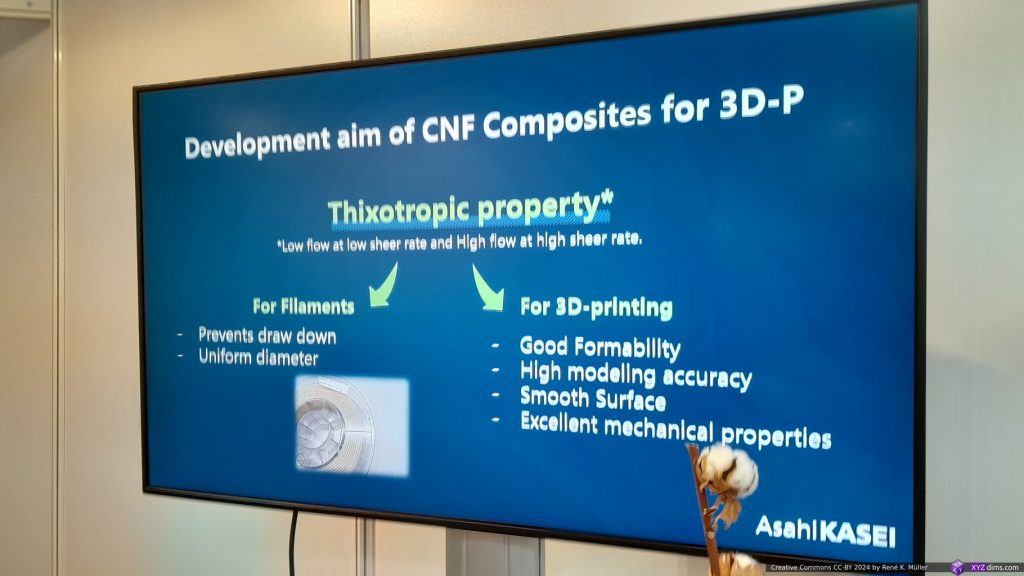
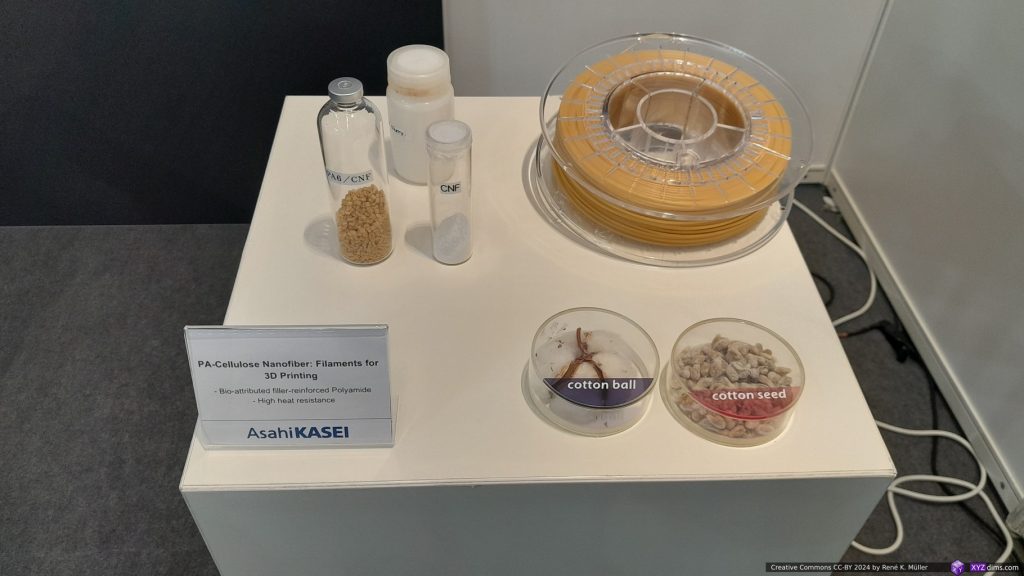
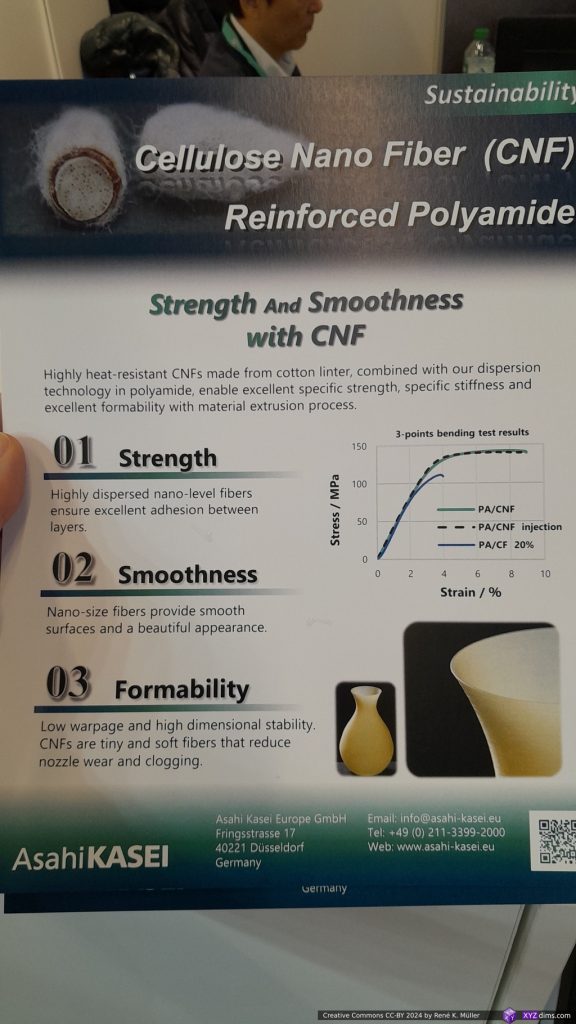
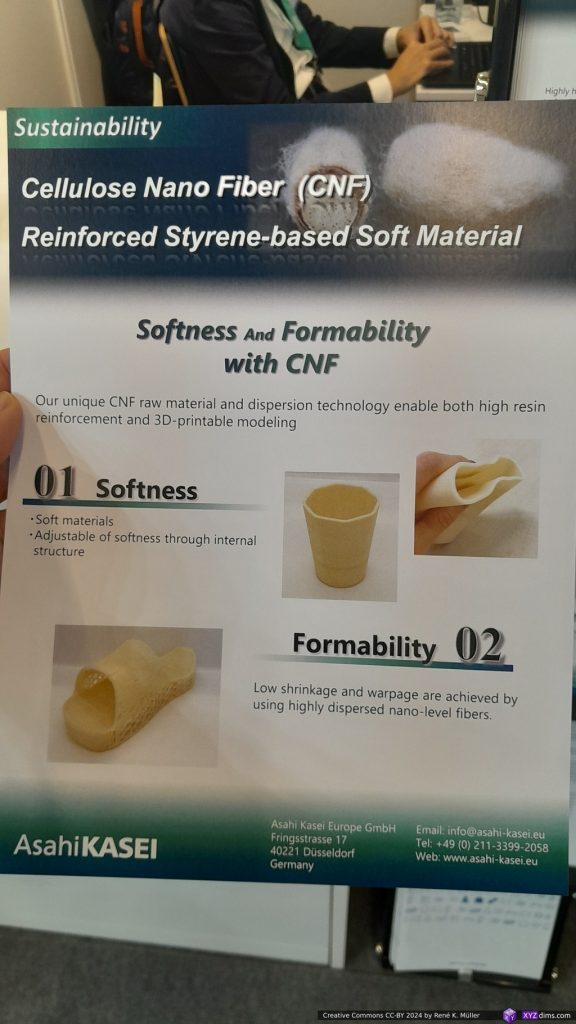
While their booth has been very small and unassuming, the company has nearly 50,000 employees world-wide.
See more at Asahi KASEI and especially this announcement.
Genera
As far I saw they are one of few which makes resin printers which print, wash and cure in the same machine (Genera G3), where as their G1+F1 and G2+F2 they call “glove free process with shuttle technology and automated post-processing”, where the build plate is carried over in an encasing “glove free” to wash and cure station (F1 respectively F2).
- Genera G1 + F1: 134 x 76 x 140mm build volume @70um pixel resolution
- Genera G2 + F2: same as G1 plus automatic platform change for queued printing
- 153-384 x 87-216 x 320mm build volume (@40, 70 or 100um pixel resolution)
- Genera G3: same as G2 but has F2 integrated, print, wash & cure in one machine
- 268-384 x 153-216 x 320mm build volume (@70, 100um pixel resolution)

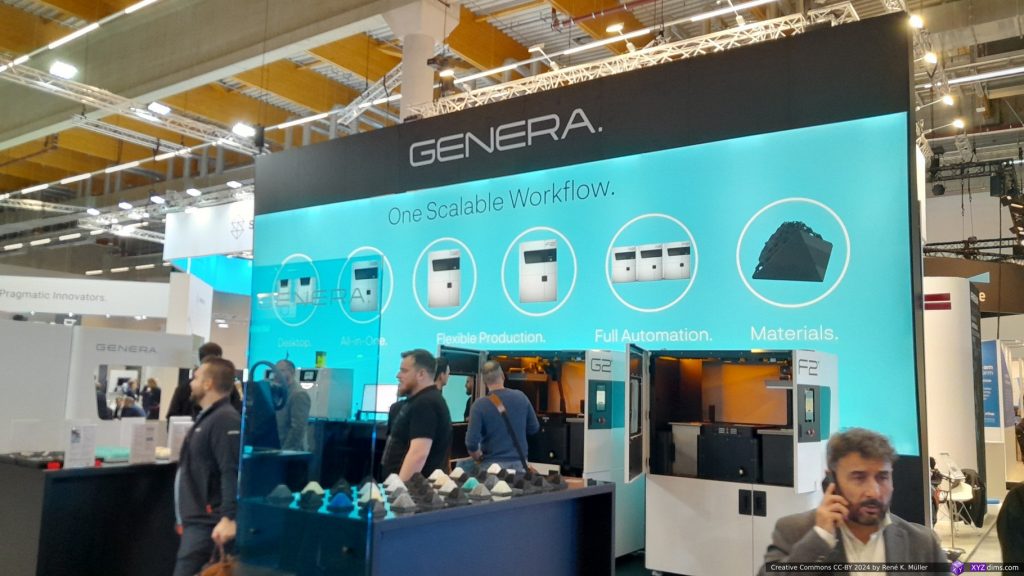
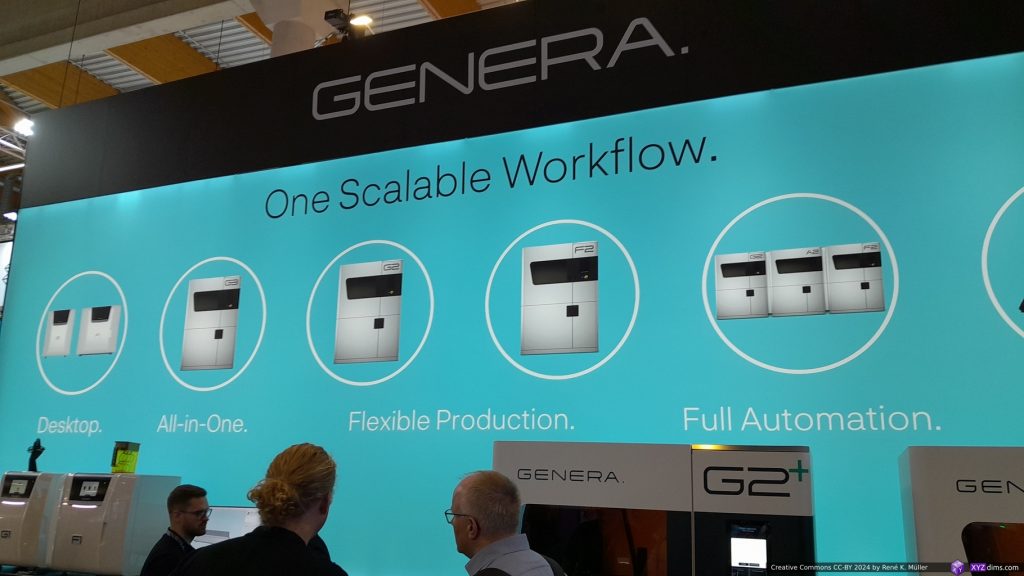
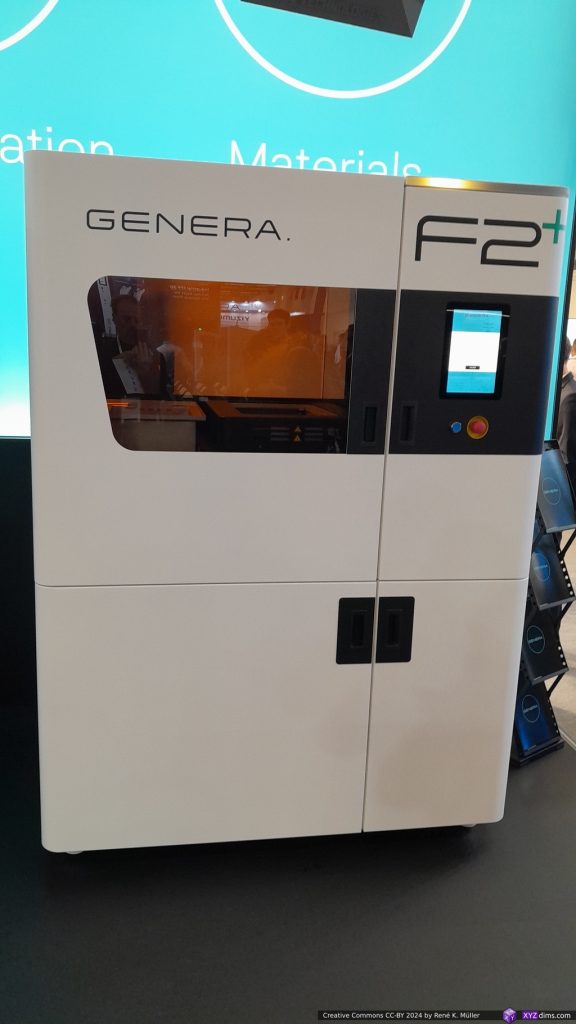
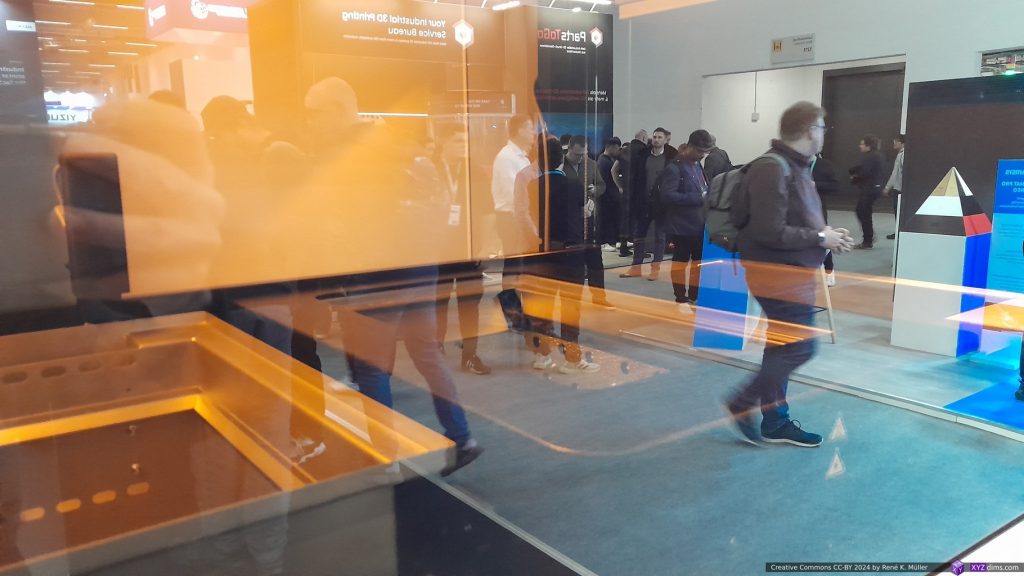
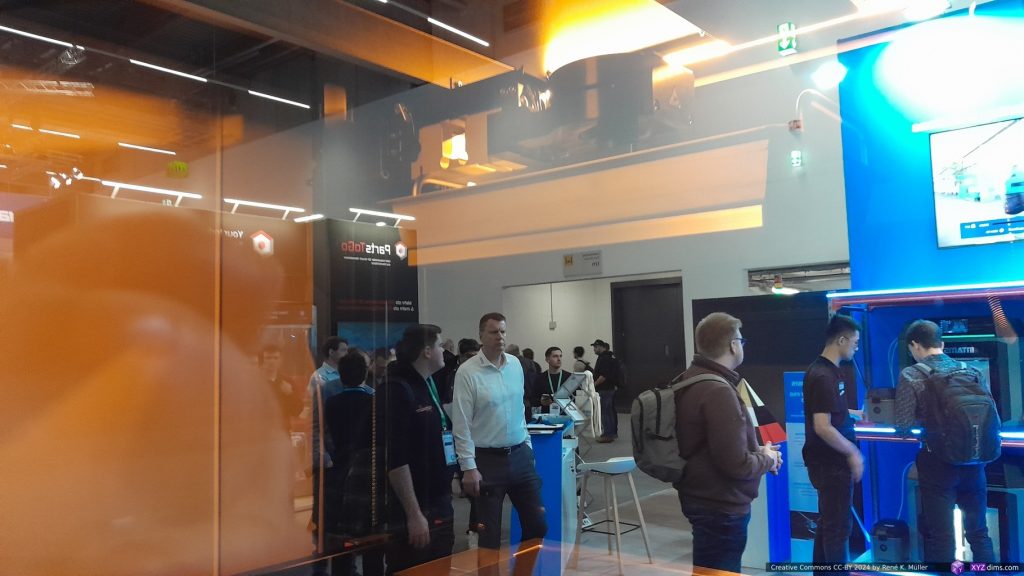
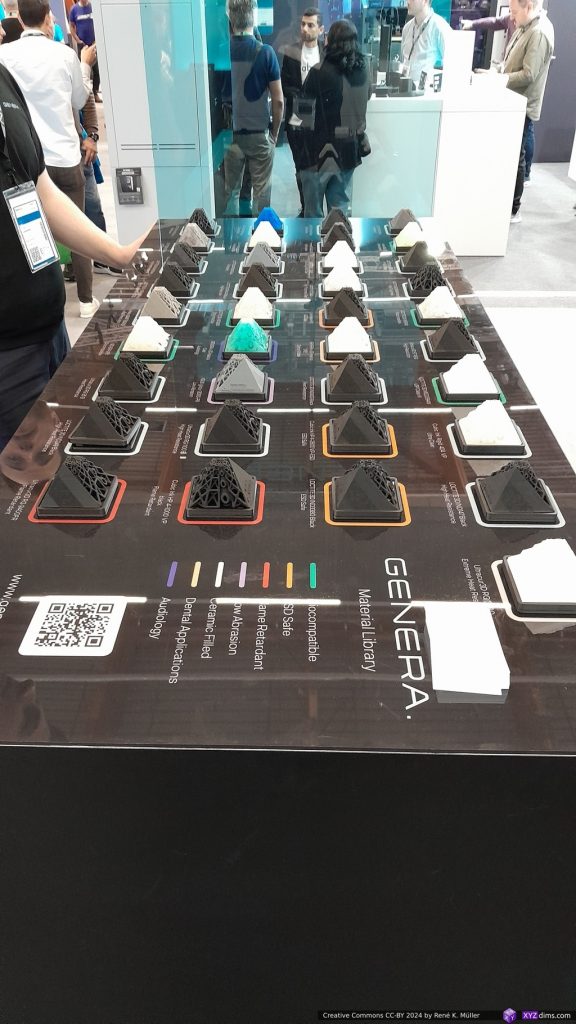
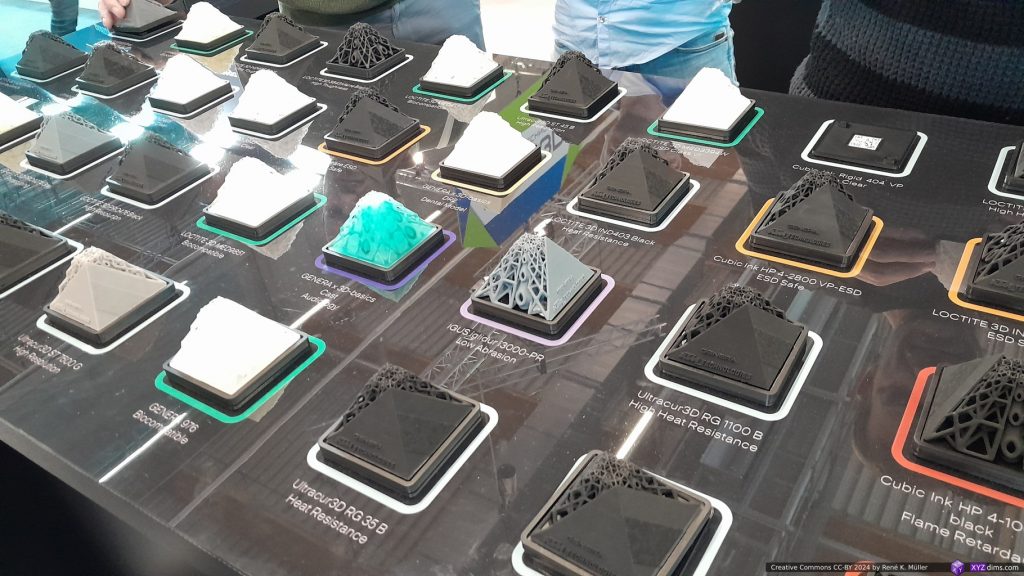
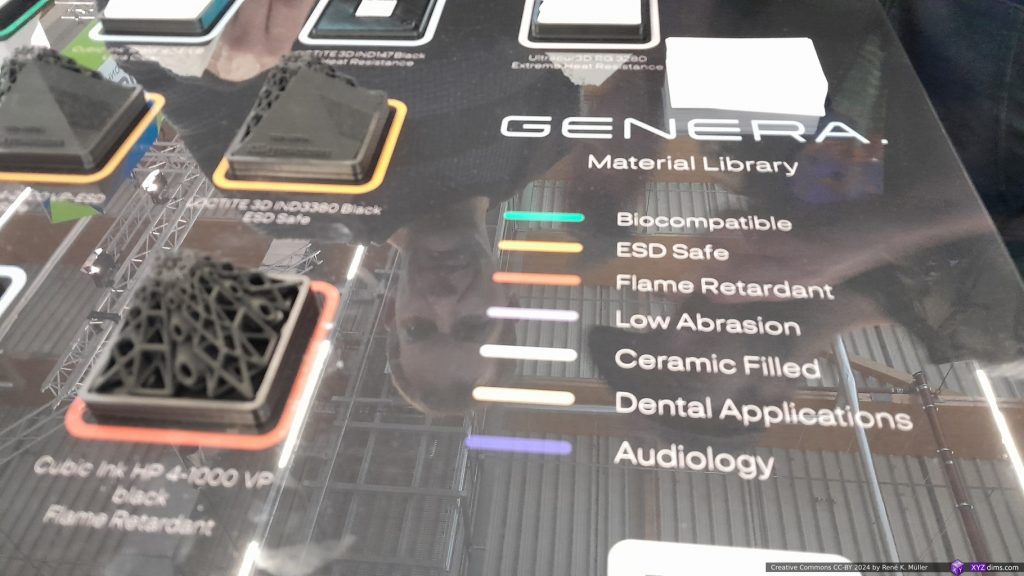
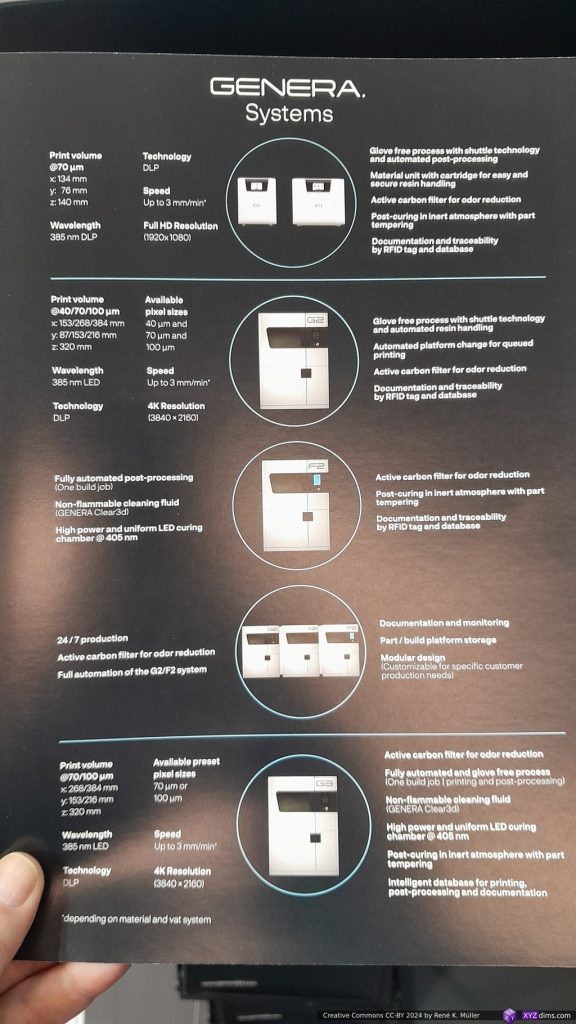
See more at Genera3d.com
Meltio
Printing metal poses the biggest challenge in my eyes as you have to put immense amount of energy to deform metal, while maintain or desire high degree of precision. So Meltio focuses on Directed Energy Deposition (DED) and Wire-Laser Metal Deposition (W-LMD): stainless steel, carbon steel, titanium alloys, nickel alloys, copper and aluminium:
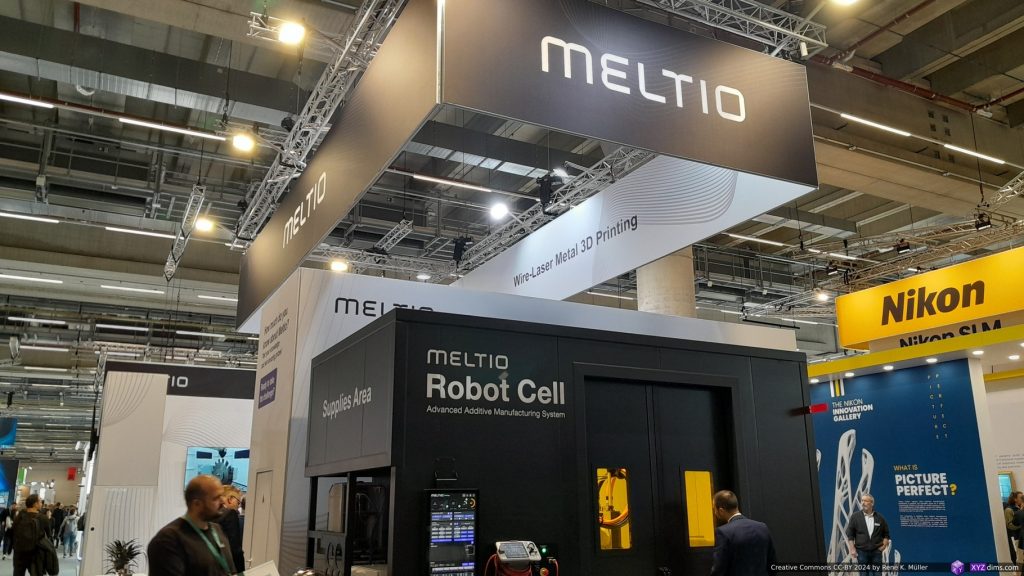
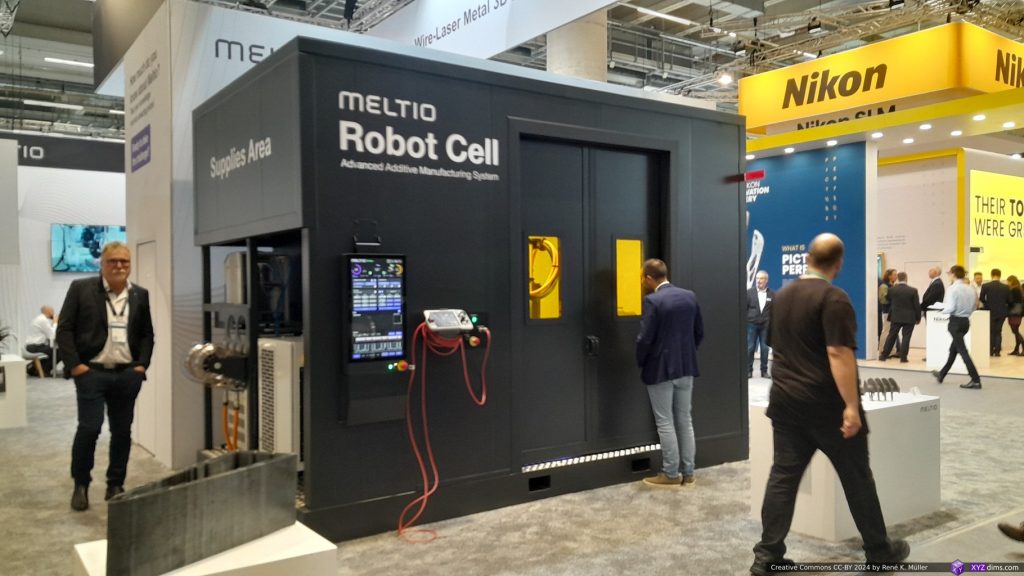
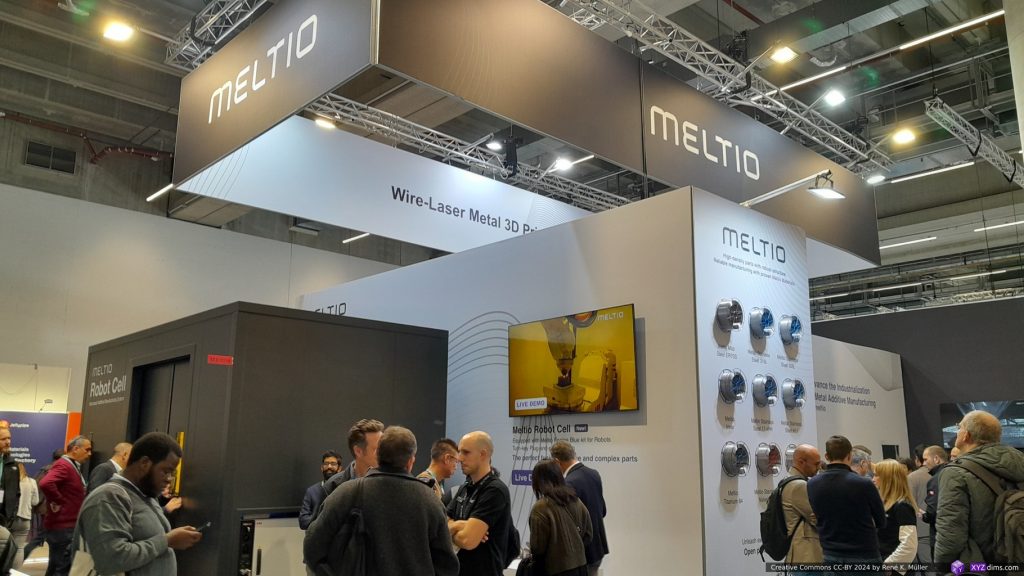
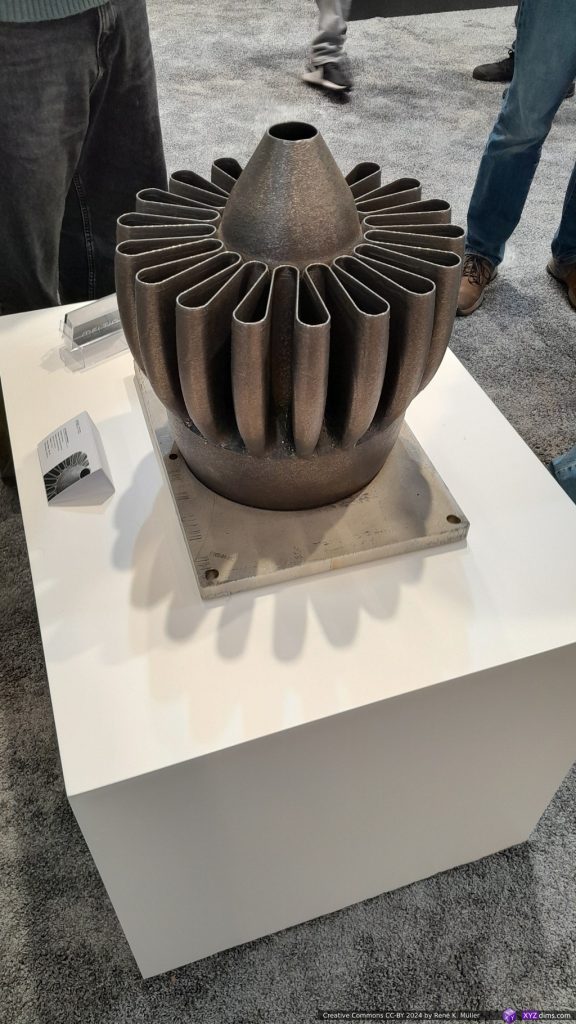
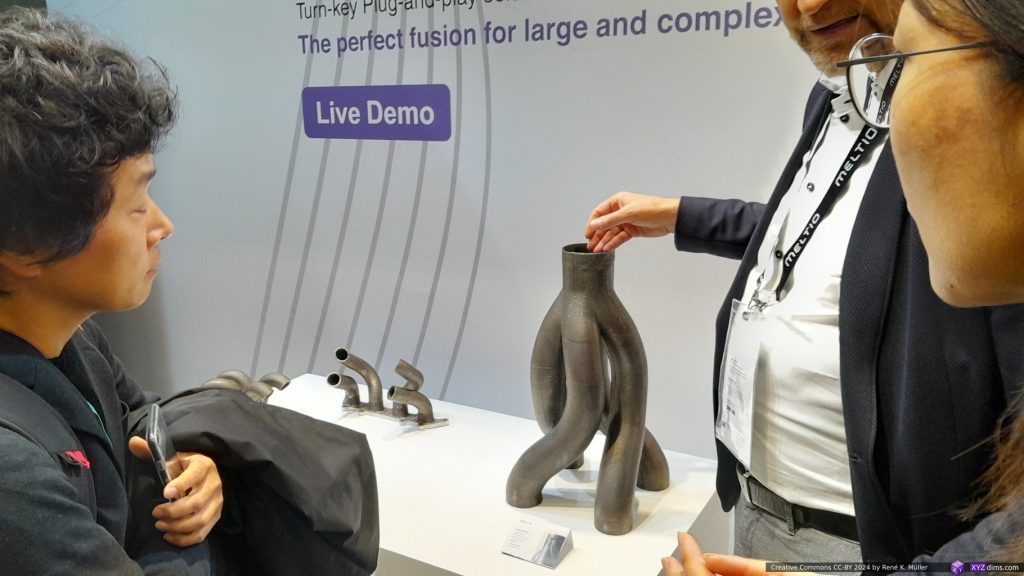

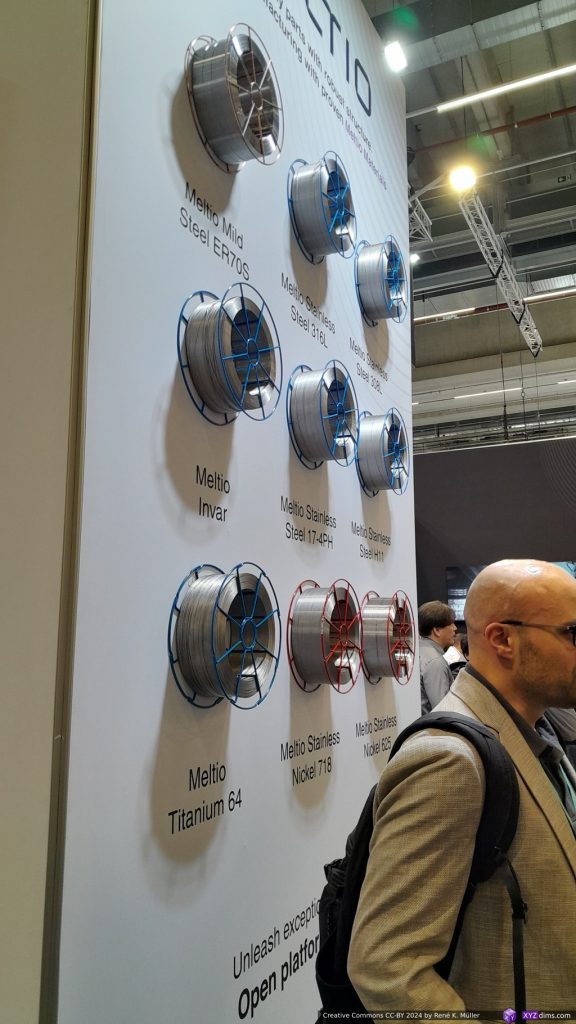
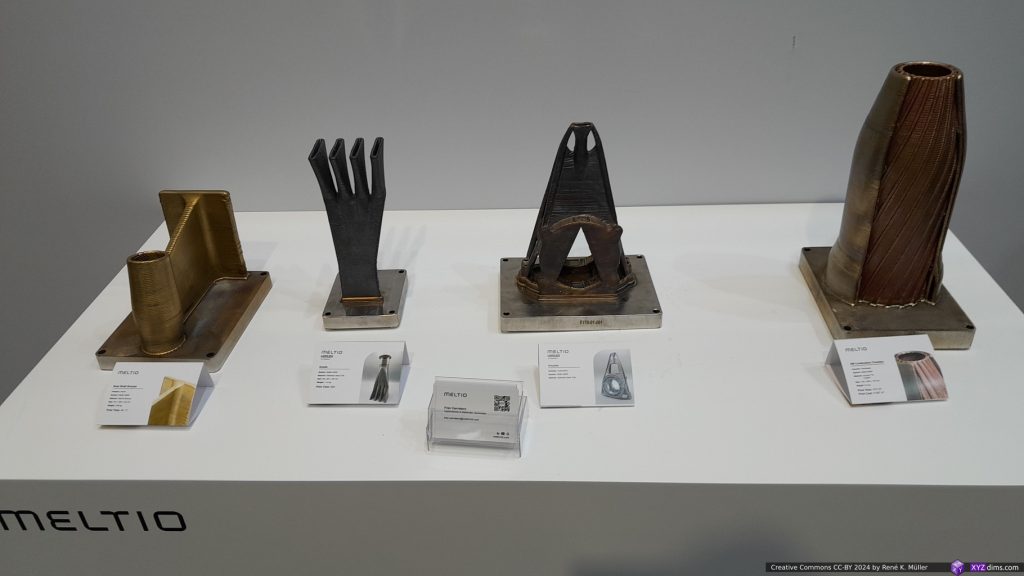

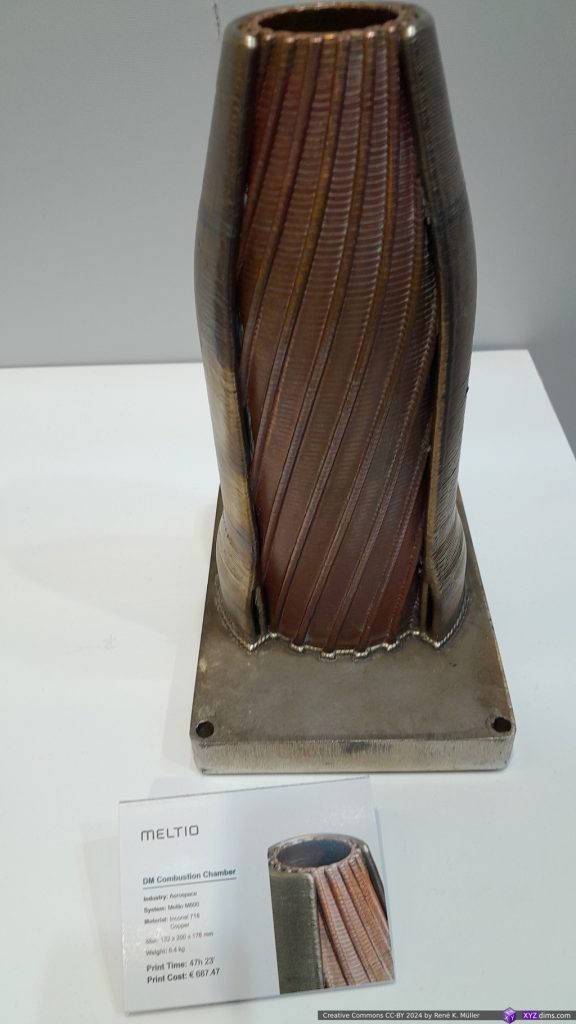
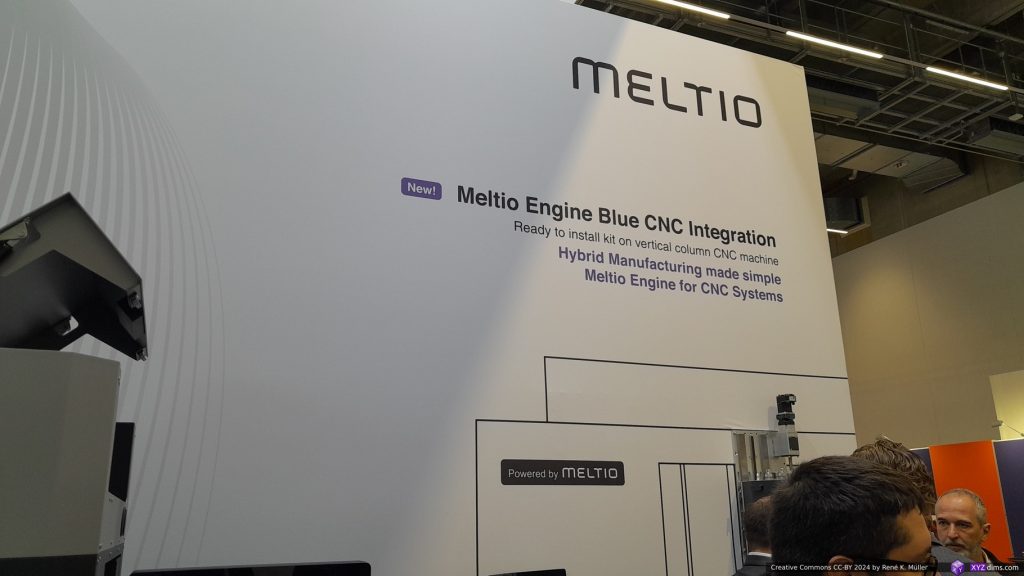

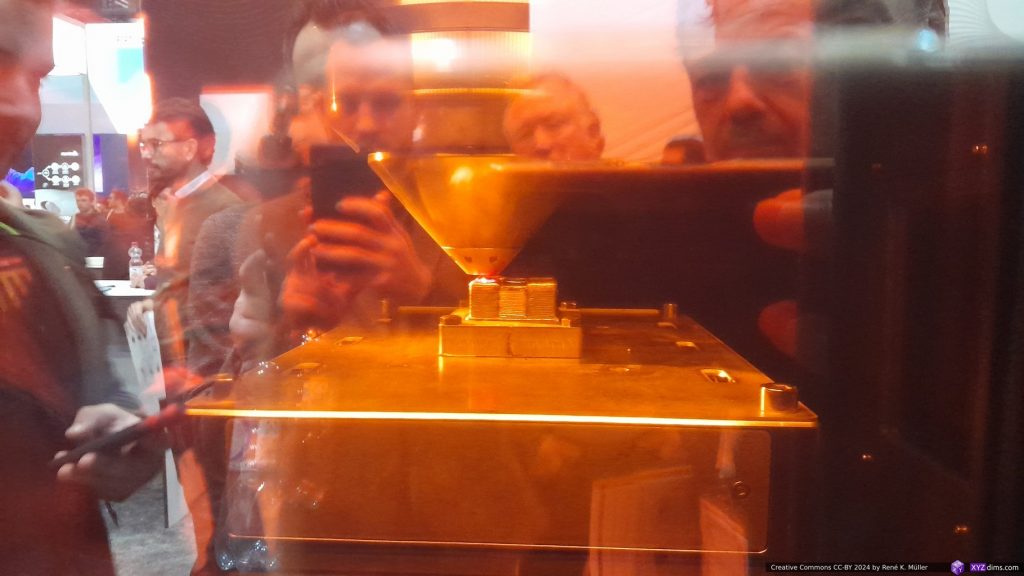
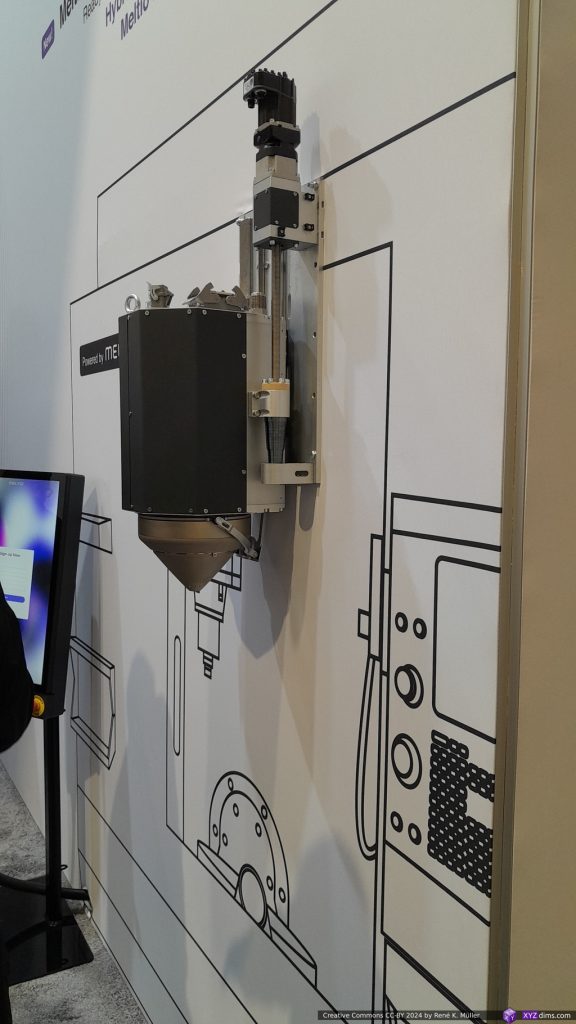
Their sample prints are massive, and quite rough compared (0.8-1.2mm wire diameter) to Selective Laser Melting (SLM, powder-based) models where we get 50um feature size.
Their “Engine Blue Integration Kit” integrates into existing CNC machines making it hybrid operation and achieve traditional CNC tolerances and feature size – one of the many examples where Additive & Subtractive Manufacturing are put together with their respective strengths.
See more at Meltio3d.com
Fraunhofer
Fraunhofer is a prominent research institute in Germany, with multiple booths displaying cutting edge AM methods – I didn’t have the time to dig deeper into their samples, somehow nothing stood out prominently, or it was vaguely explained at first sight unlike at other booths.
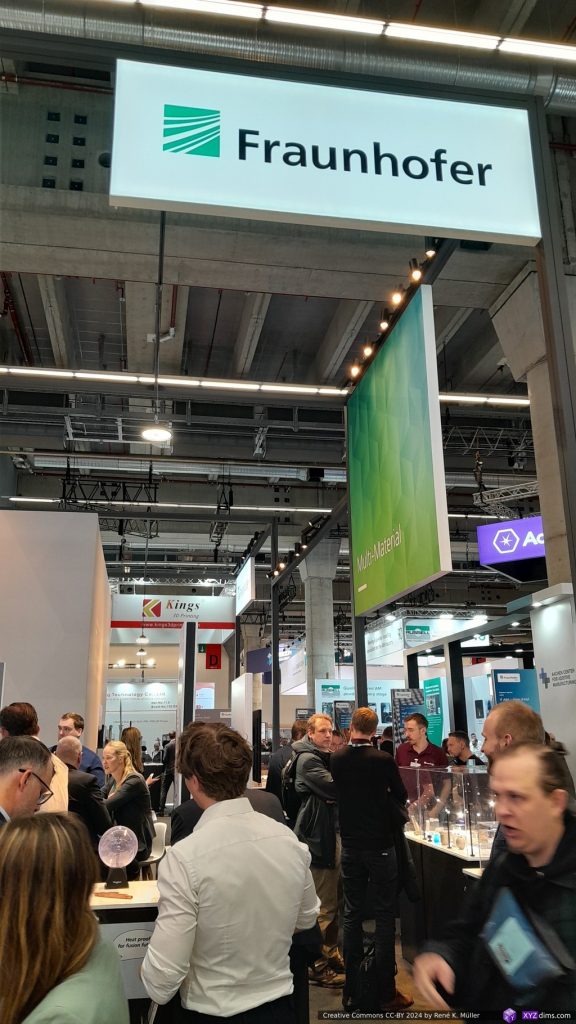
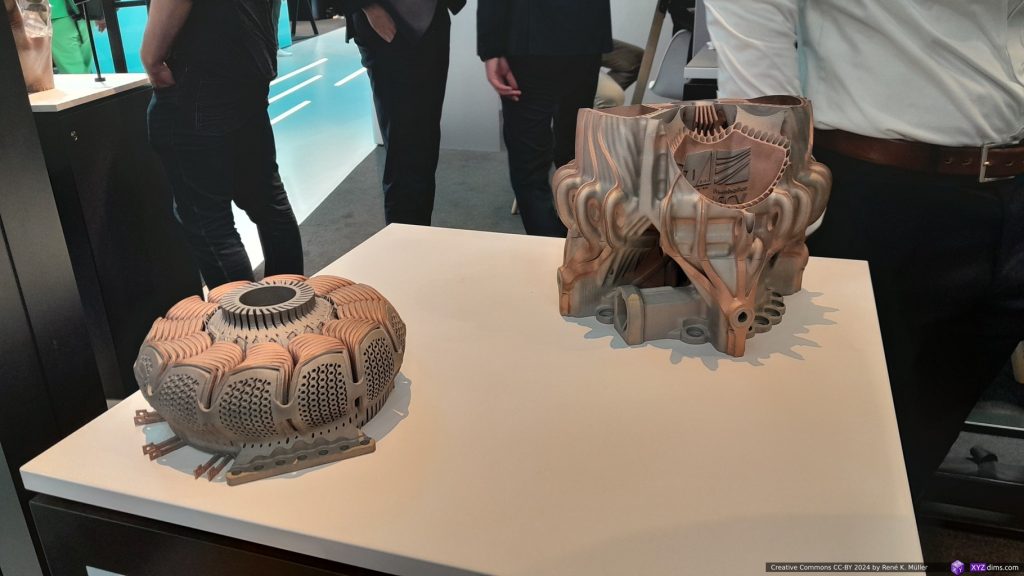
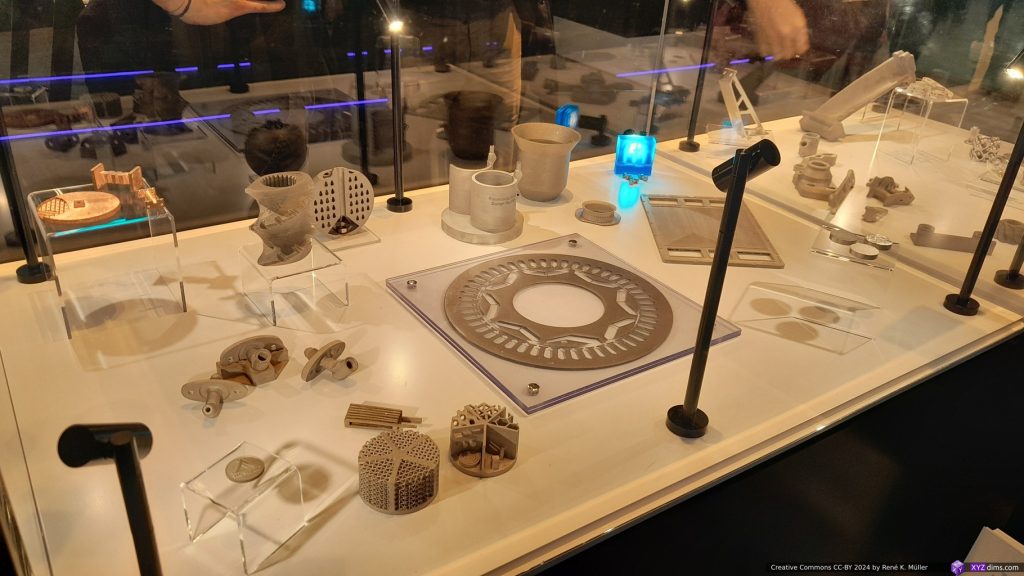
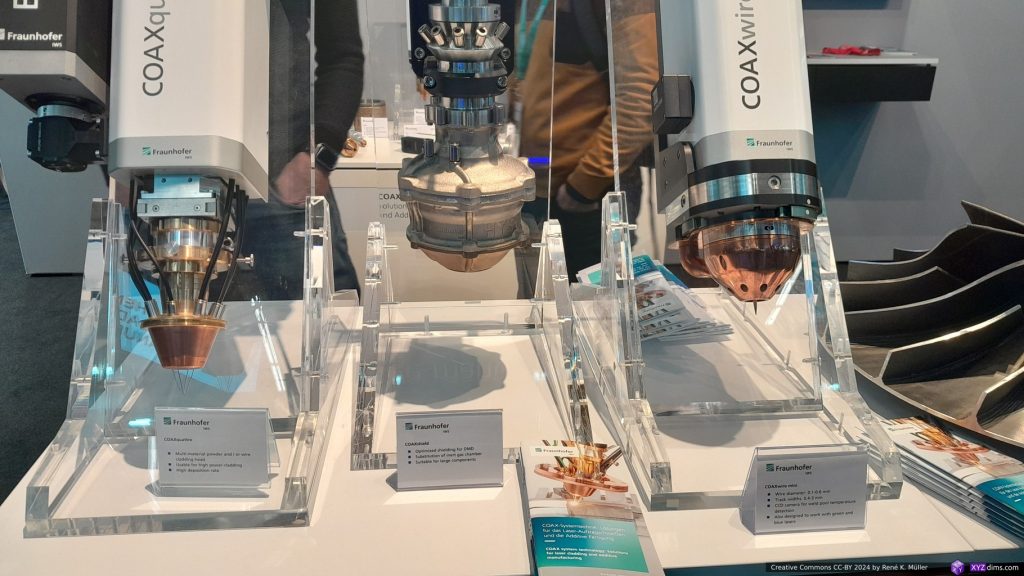
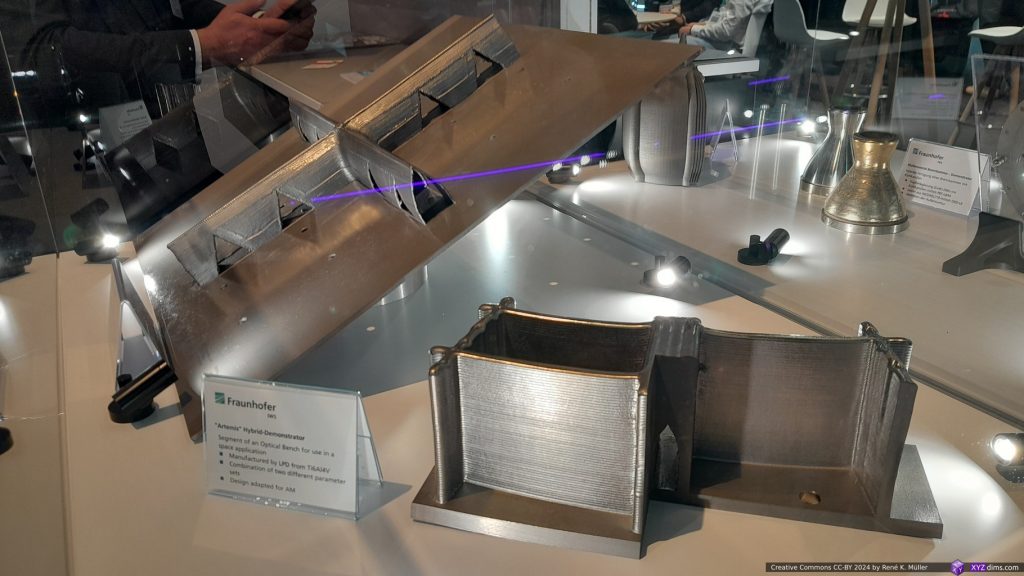
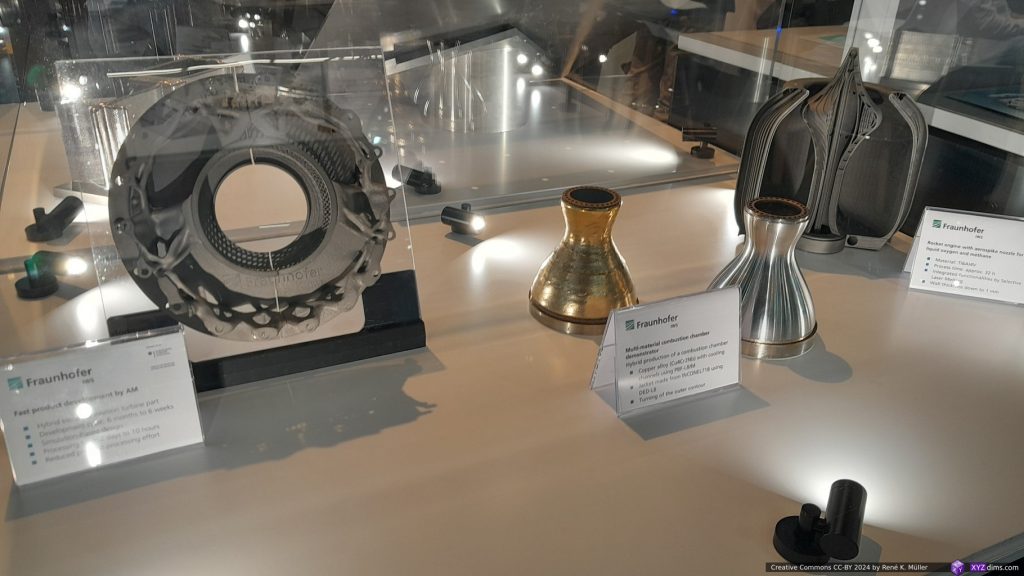
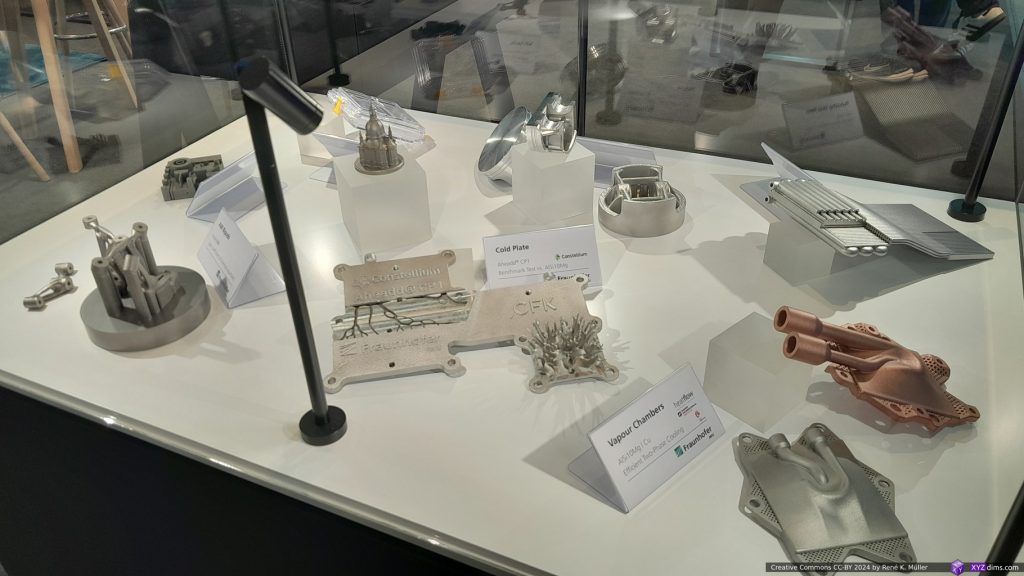
See more at Fraunhofer.de
Markforged
That booth was crowded most of the times, so I did only pass by – so far the FX10 caught briefly my attention:
- 375x300x300mm build volume
- FDM/FFF operating with
- Metal: Metal Fused Filament (MFFF) with sintering post-processing, or
- Composites: other composites incl. Continuous Carbon Fiber (CCF)
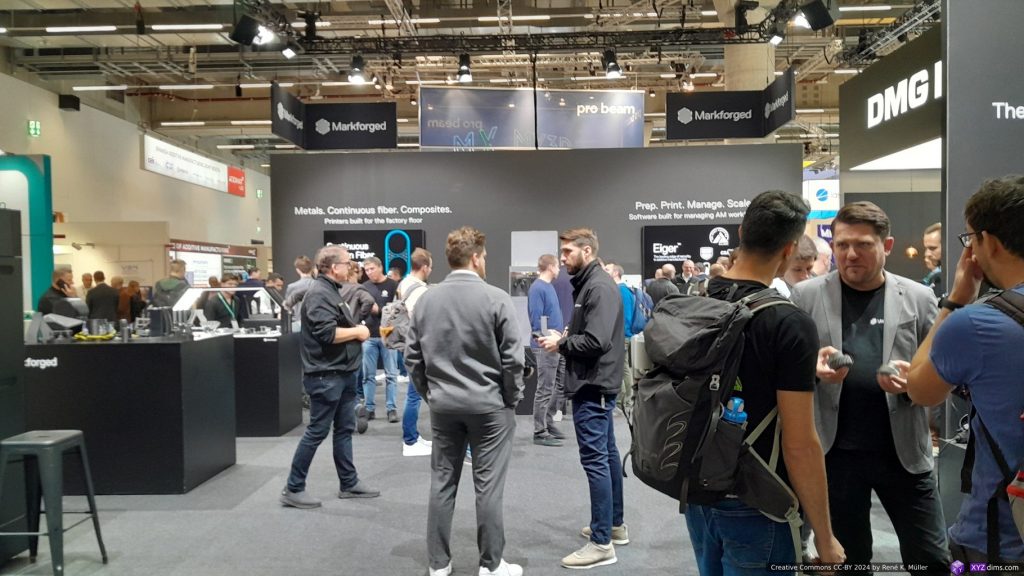
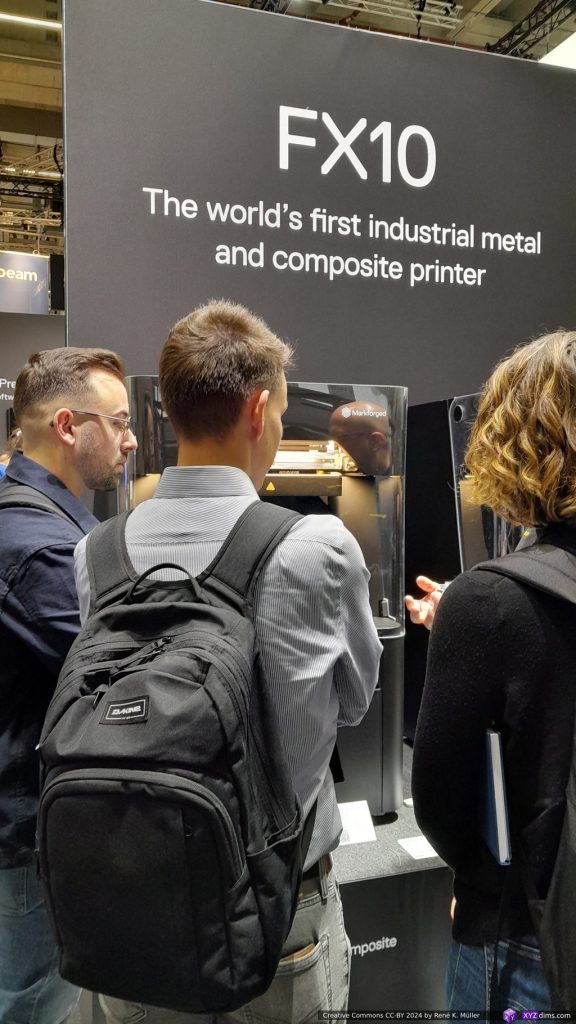
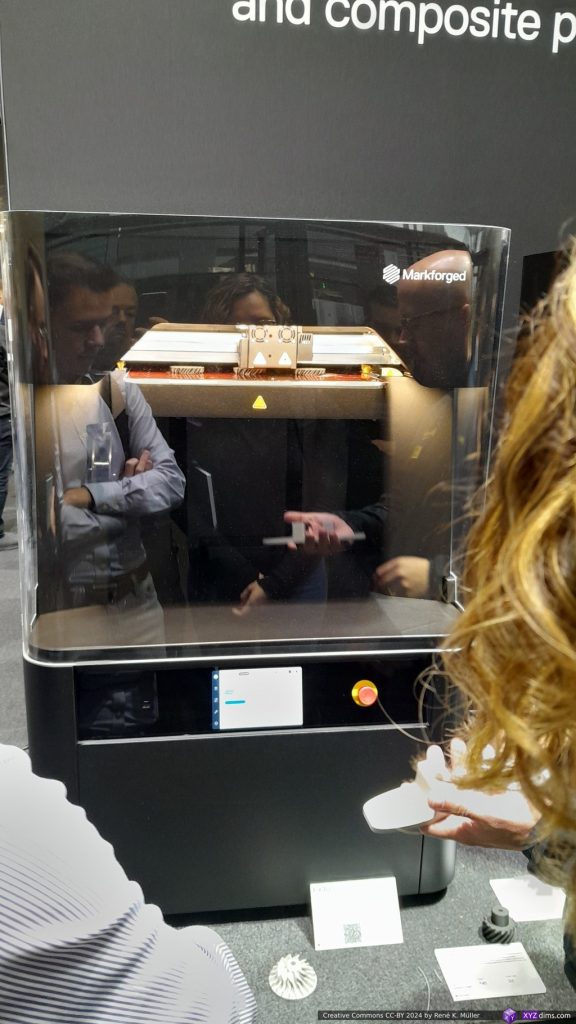
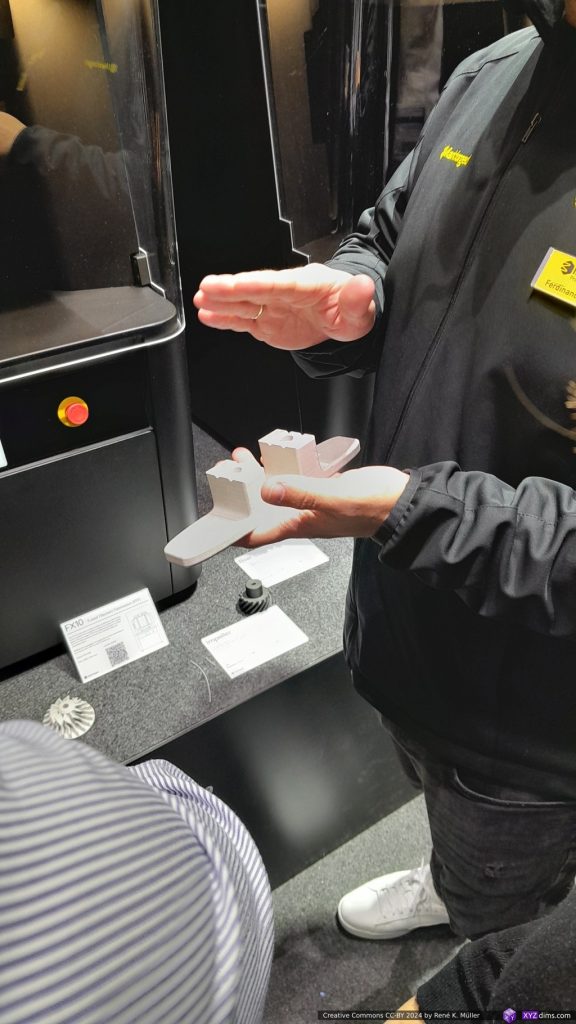
See more at Markforged.com
DMG Mori
Whenever I pass by their booth, the only thing I think is “car-sized 3D printers costing millions of EUR/USD”, it’s a different use-case from where I operate – as simple as that, and yet, still impressive what they achieved.
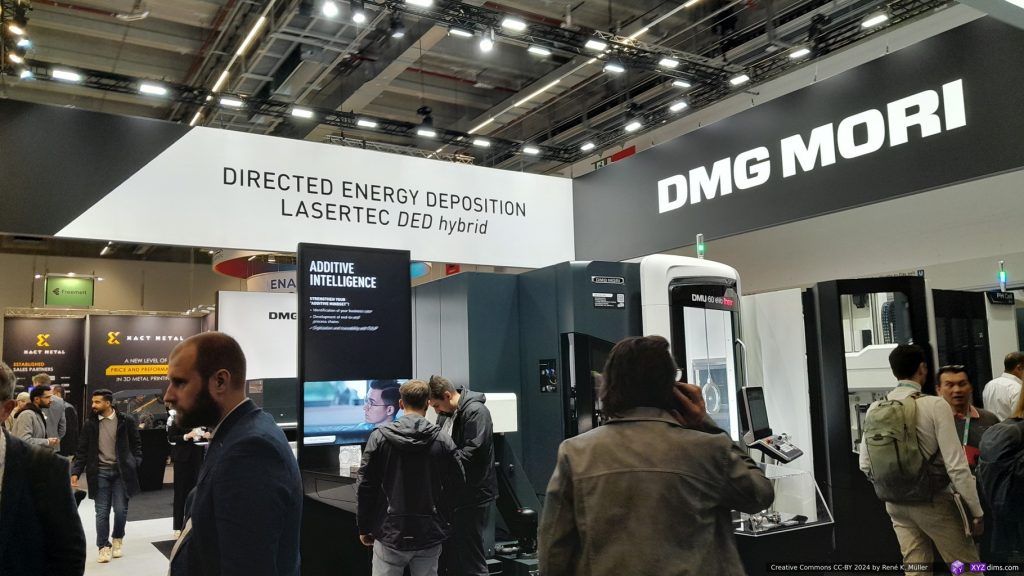
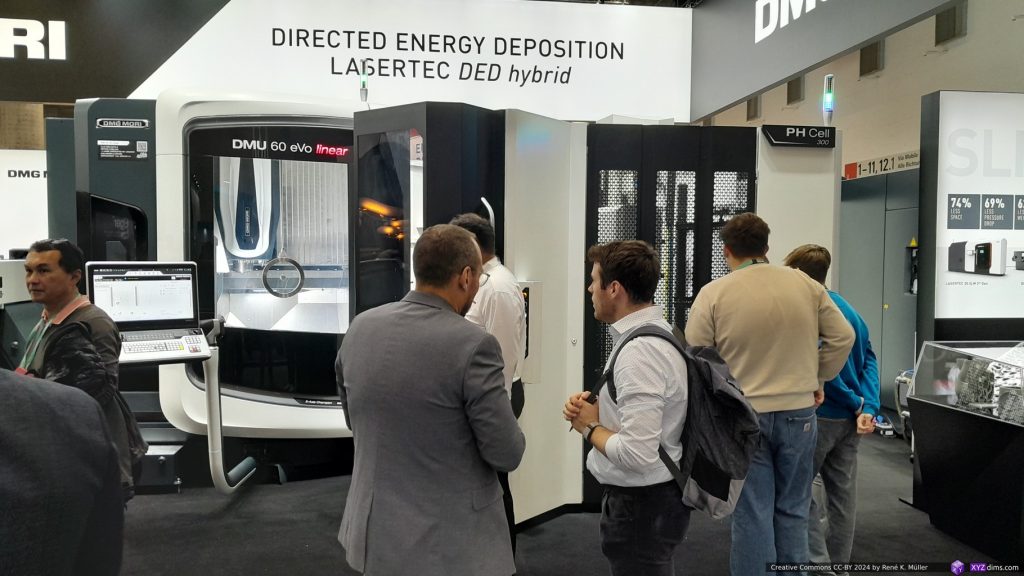
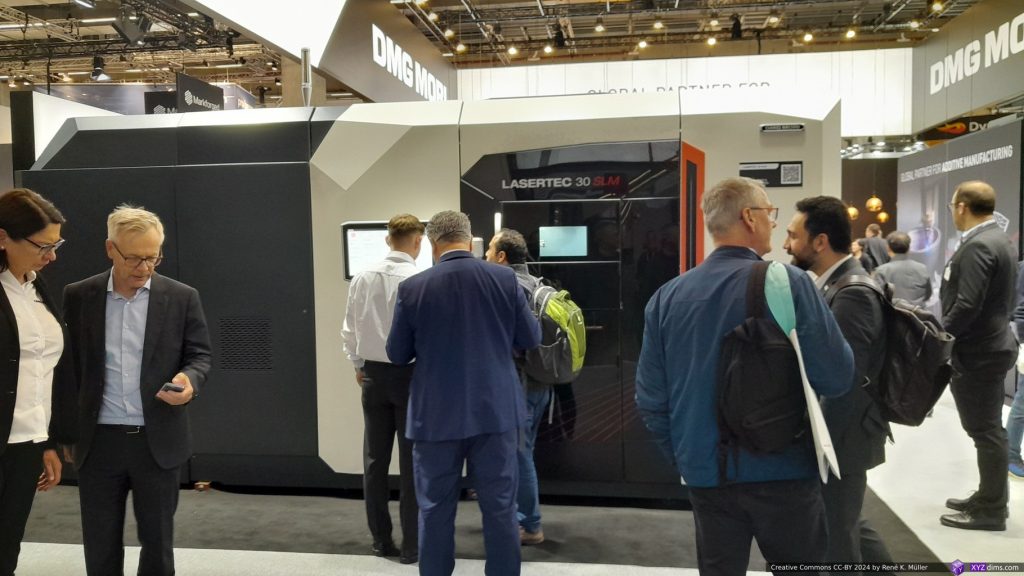
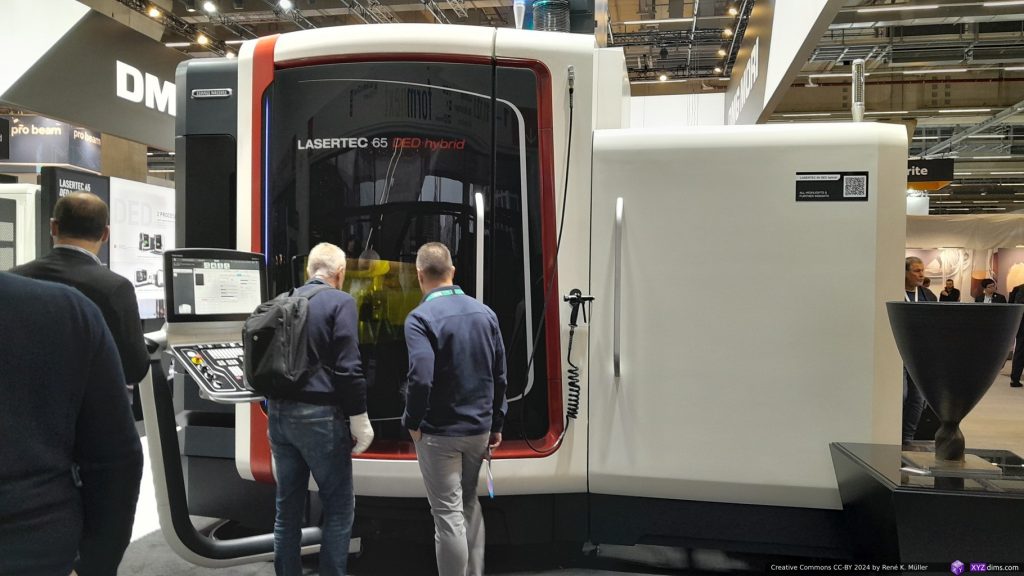
Btw, its name comes from multiple mergers: DMG (Deckel, Maho, Gildemeister) and Japan’s Mori Seiki – a blend of german and japanese workmanship.
See more at DMG MORI
Mosaic
A few years back in 2017 they released their Mosaic Palette, splicing (cutting and melding together) filaments ahead for a single filament yet achieving multi-color with a single nozzle without material waste. Meanwhile they massively scaled up their expertise and developed their own printers called Mosaic Element and print farm called Mosaic Array – and I admired the overall case design in simplicity how the filament cartridges are attached.
Element HT2 specs:
- nozzle up to 500°C
- build plate up to 120°C
- build chamber up to 80°C
- 350x350x350mm build volume
- up to 8 materials via filament cartridges
- price starting at EUR 9,500
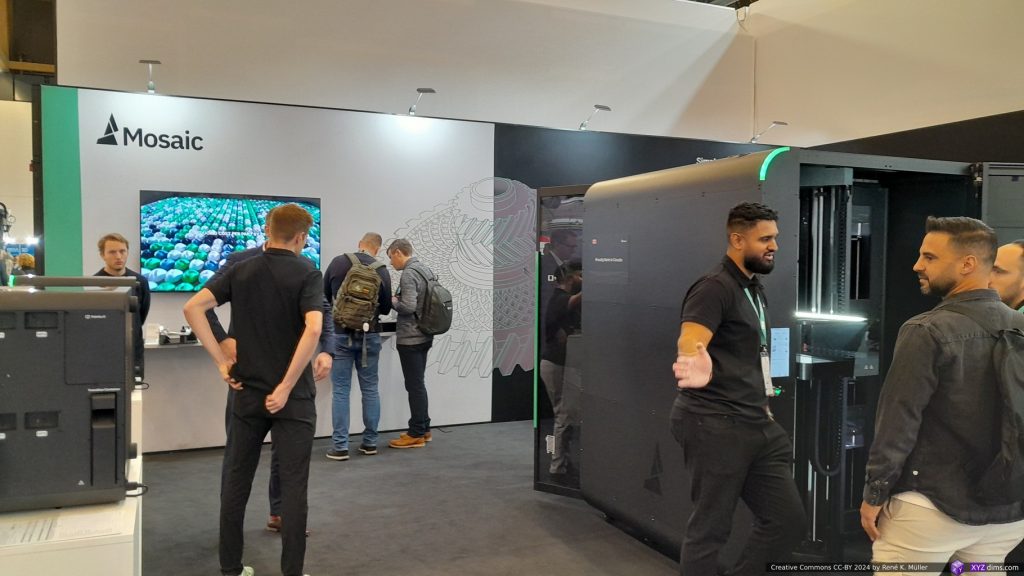
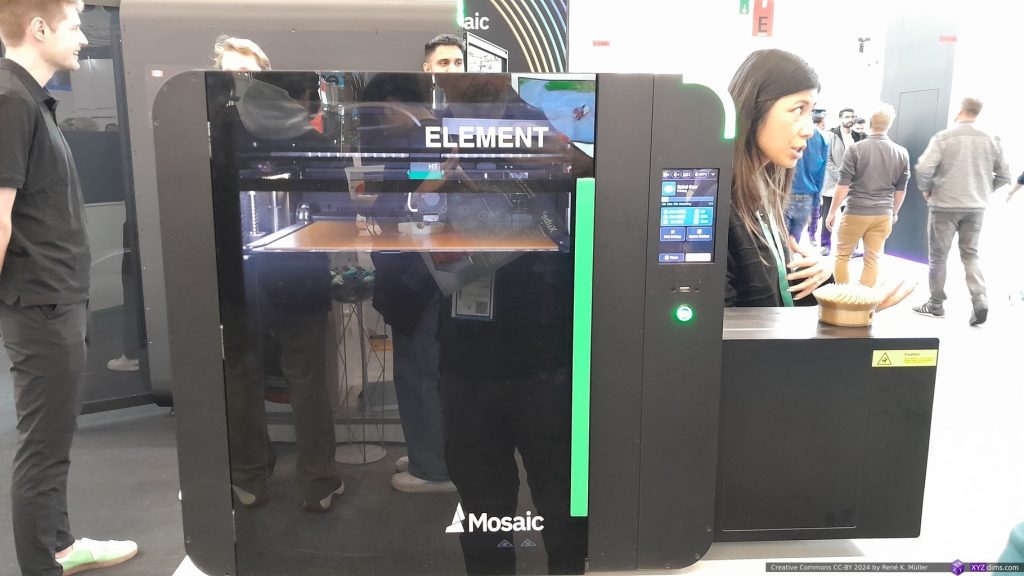
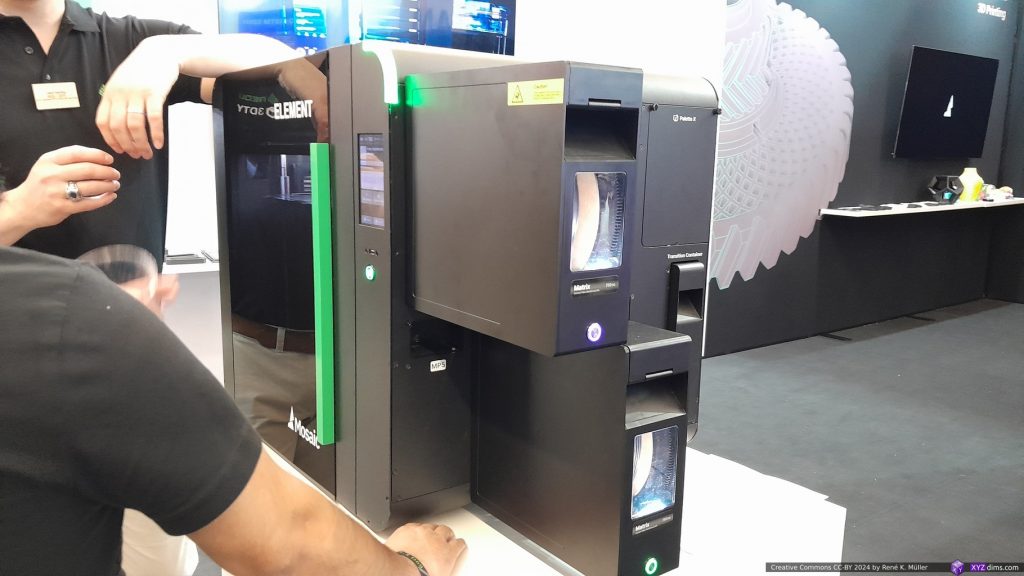
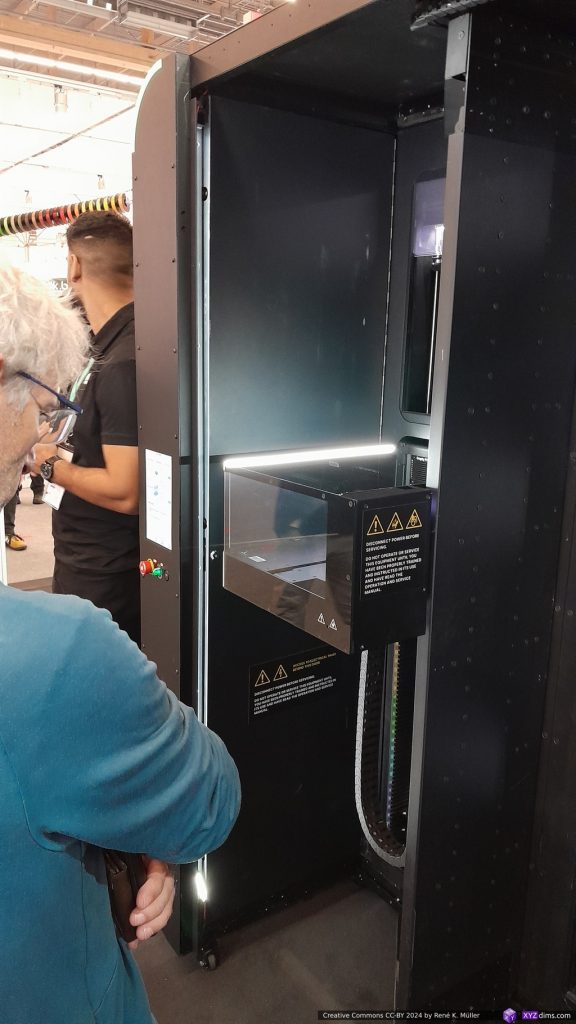

Their print farm is built on stacked printers, and a robot arm removing the built-plate with the printed piece and stack it below and refill the printers with empty build plates again.
See more at MosaicMFG.com
Miscellaneous
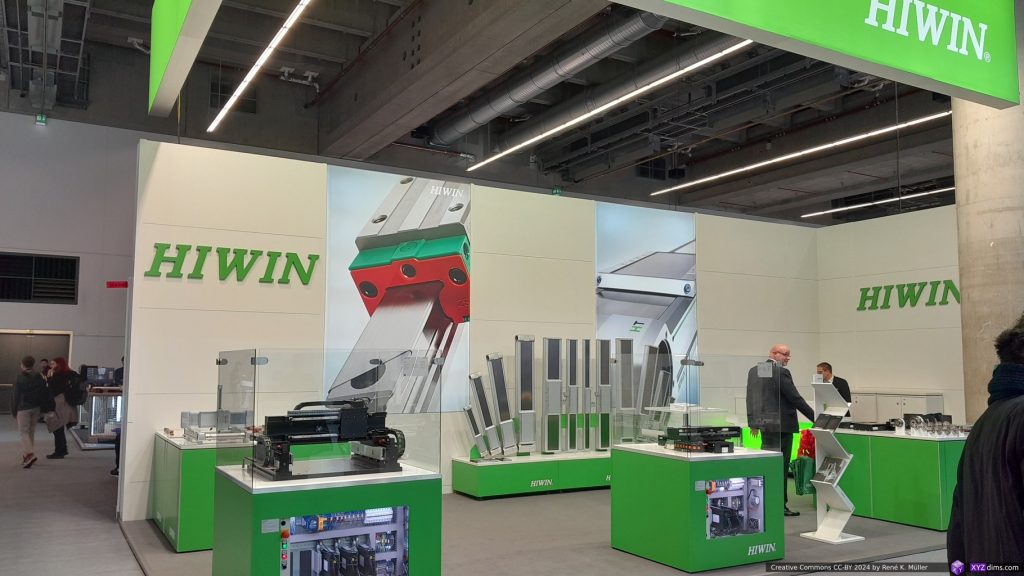
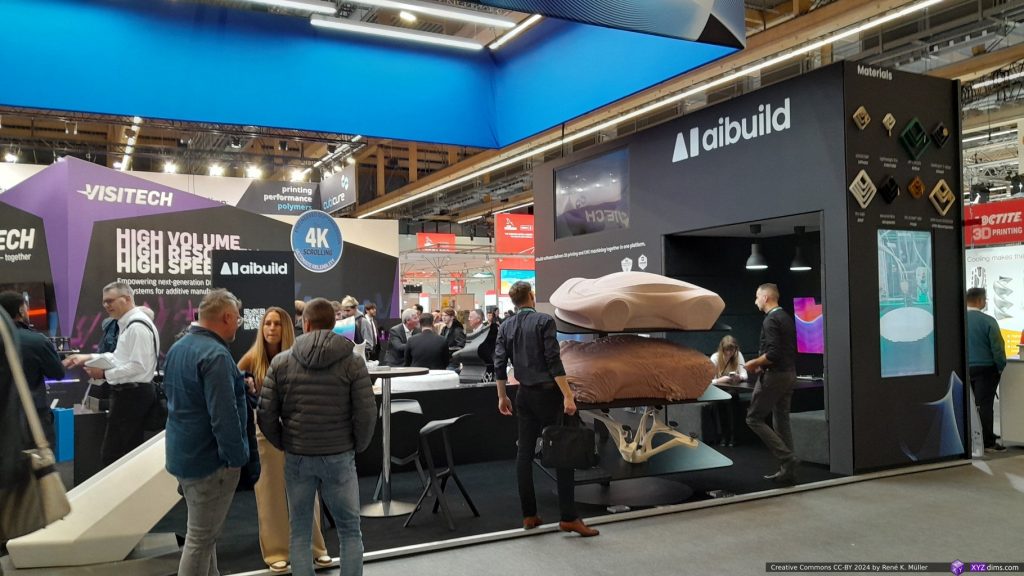
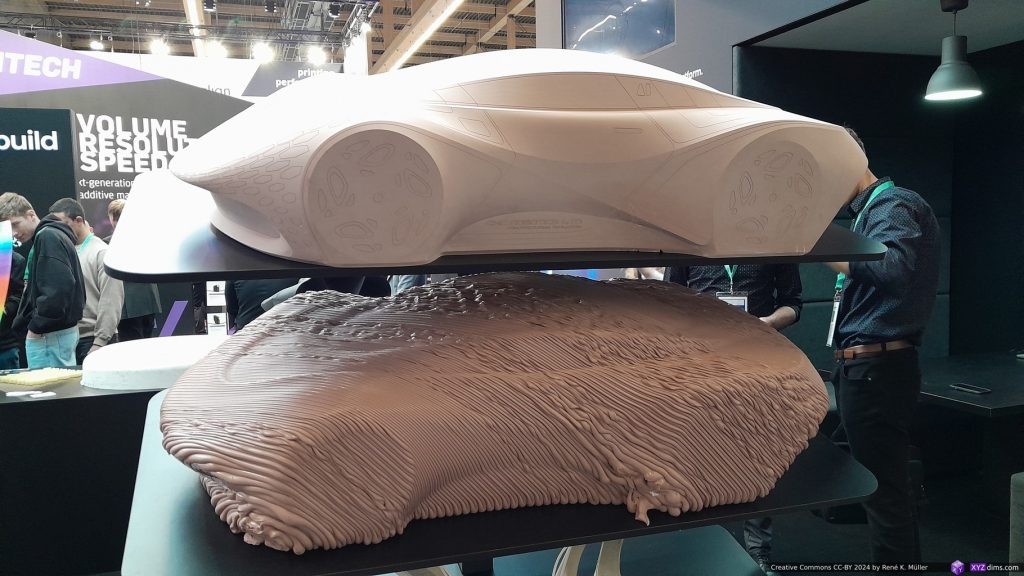


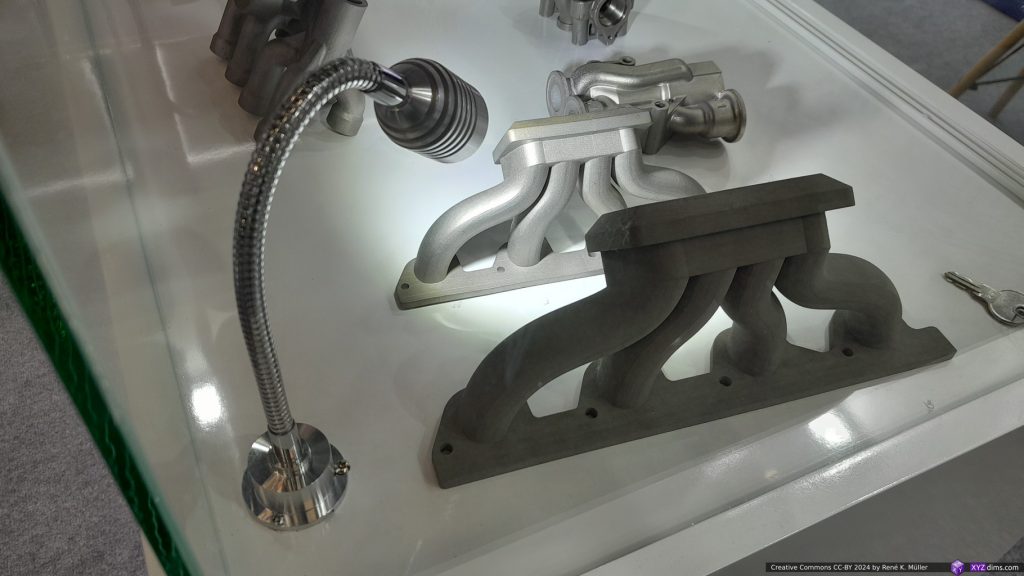
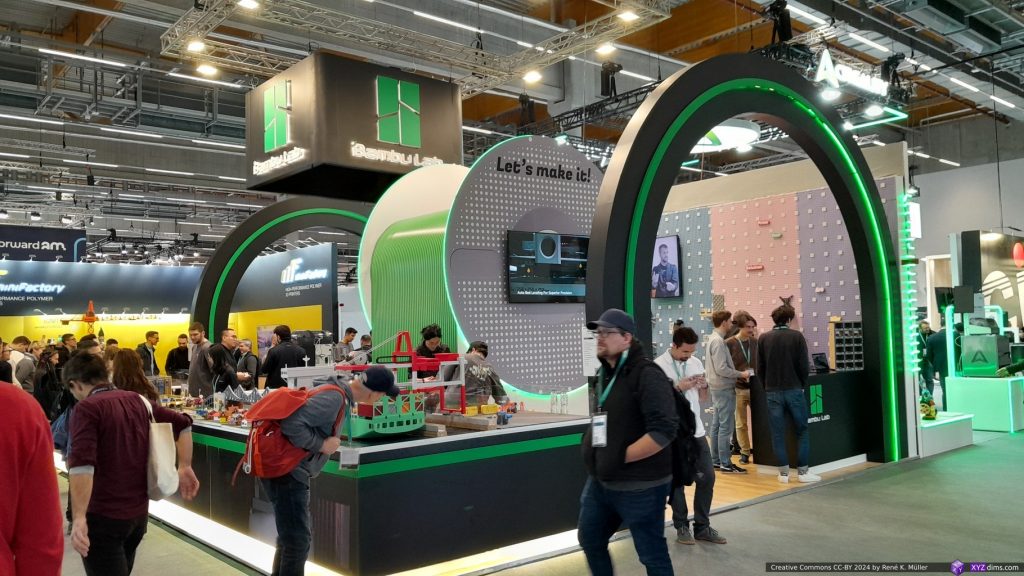
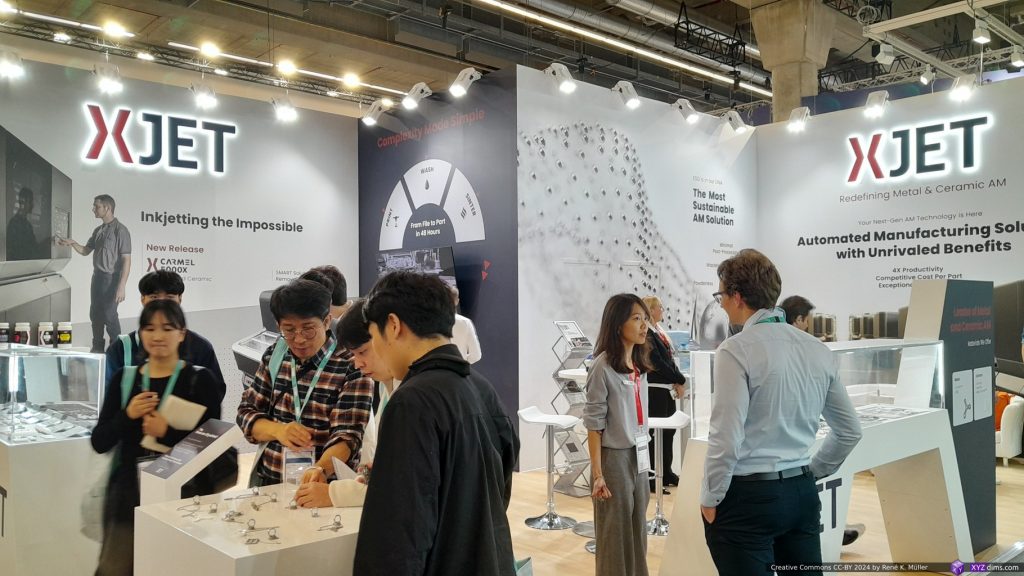
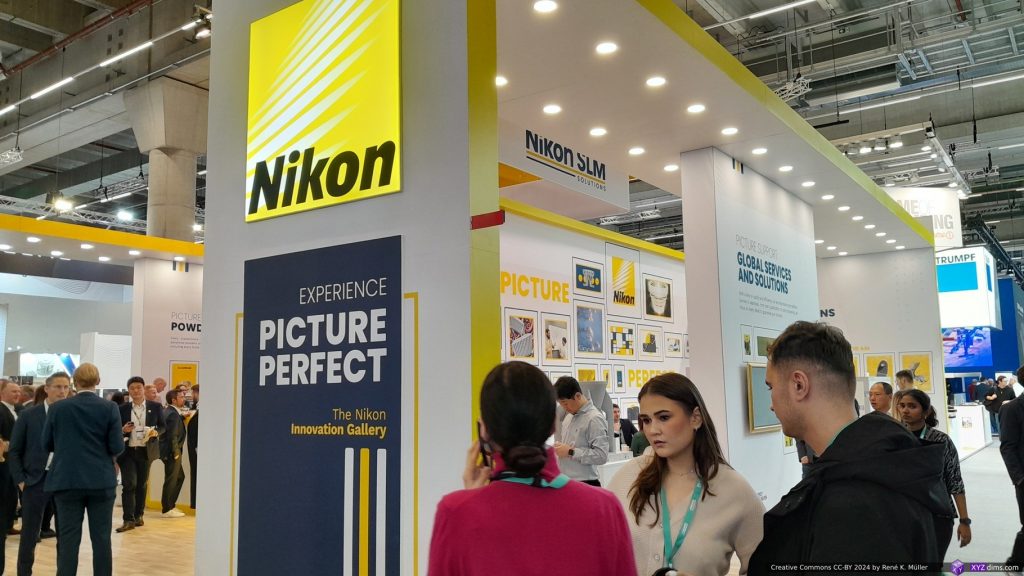
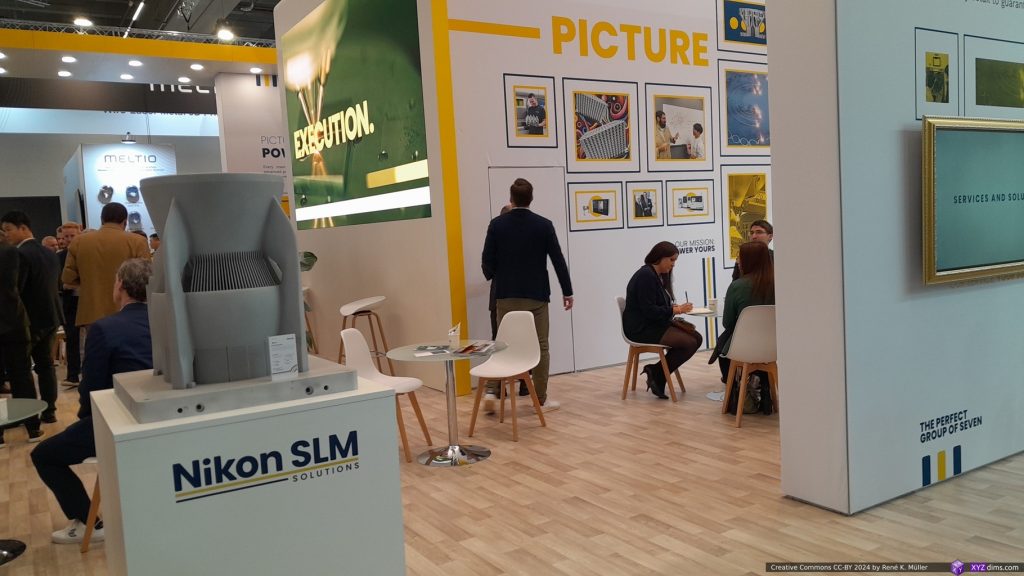
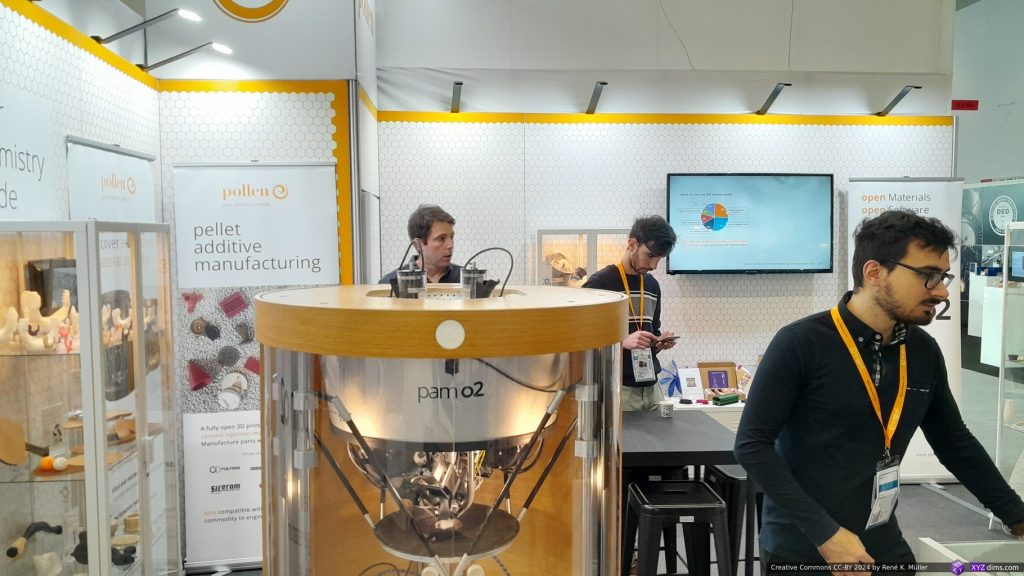
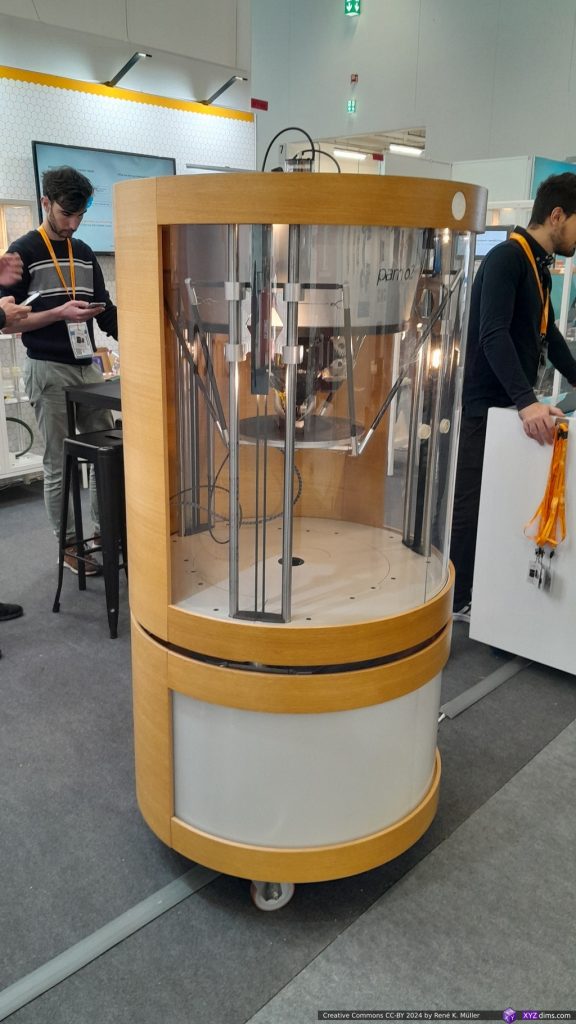
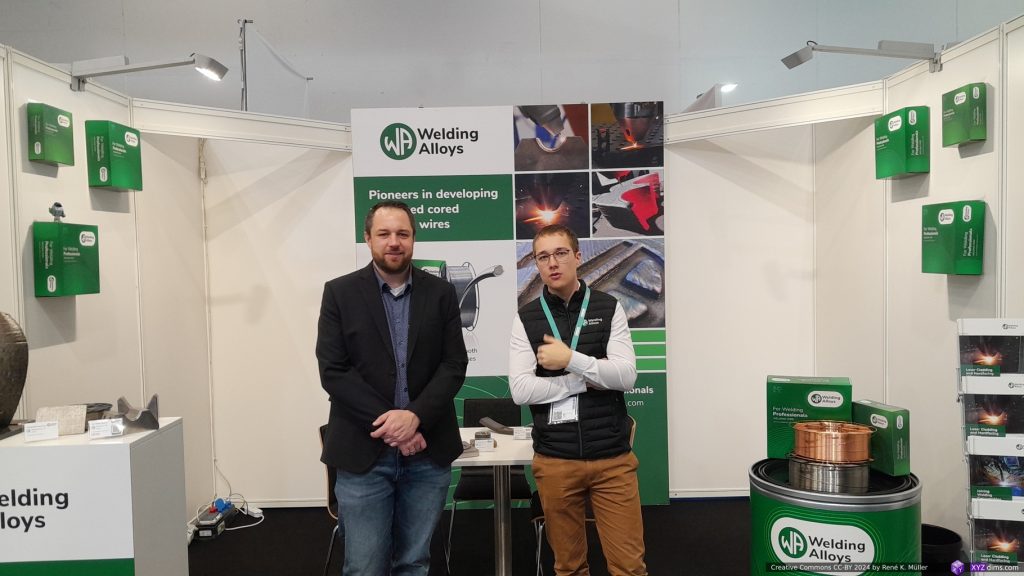
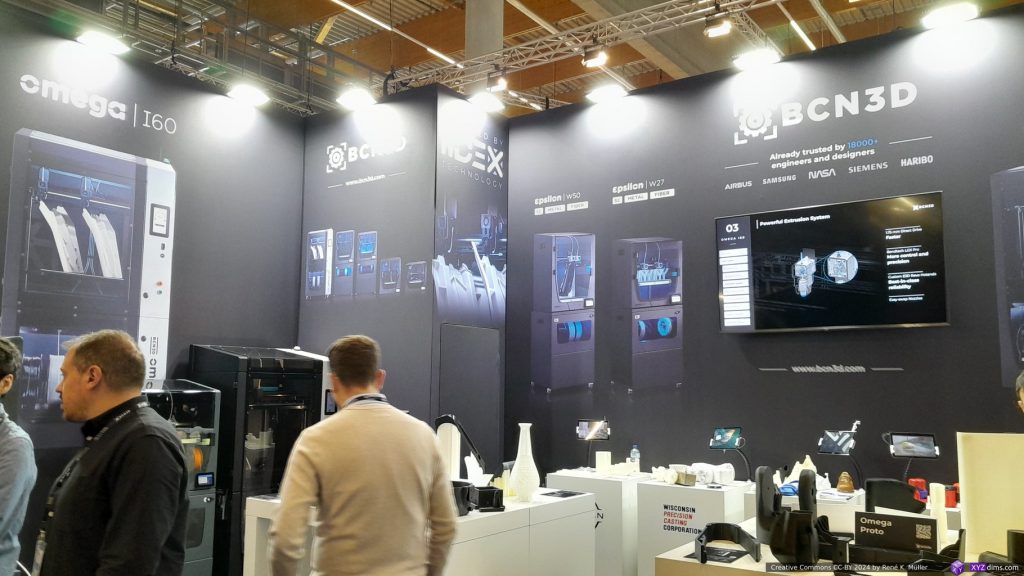

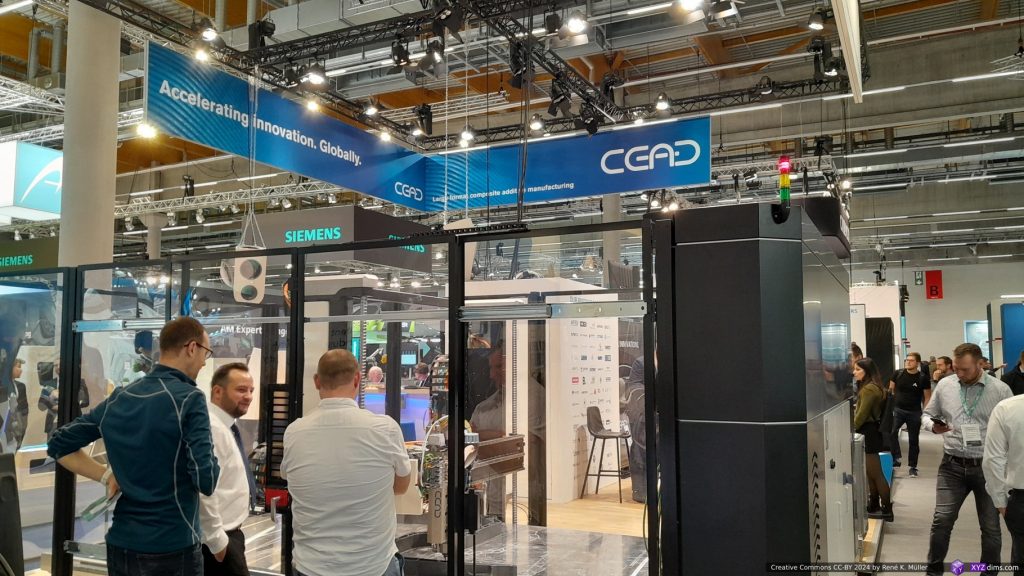
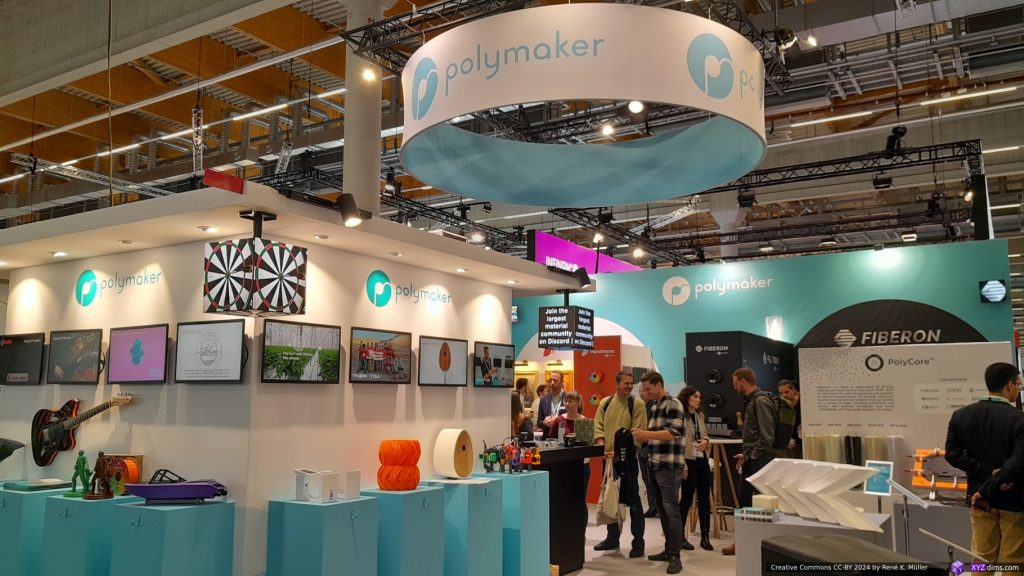
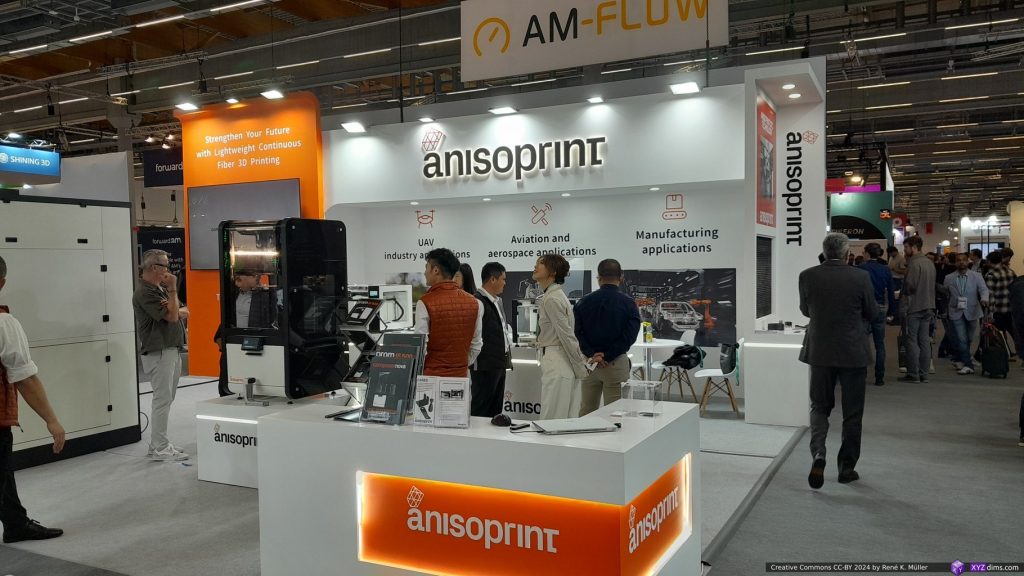
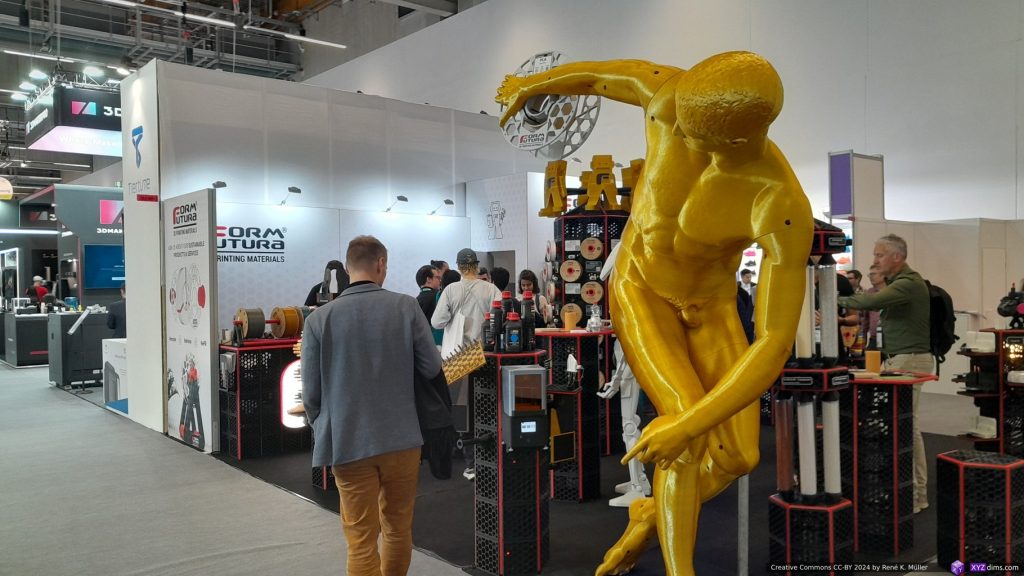
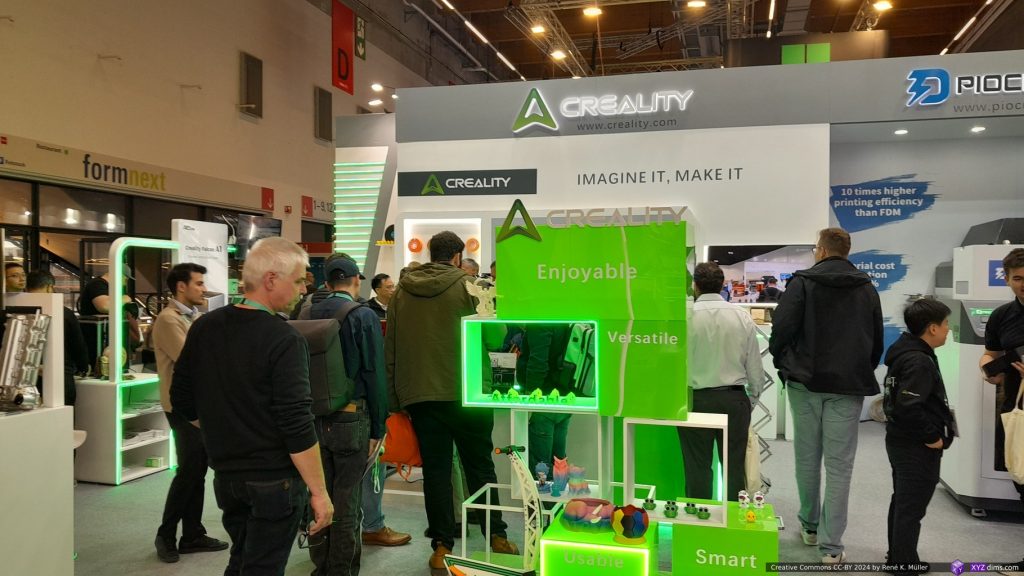
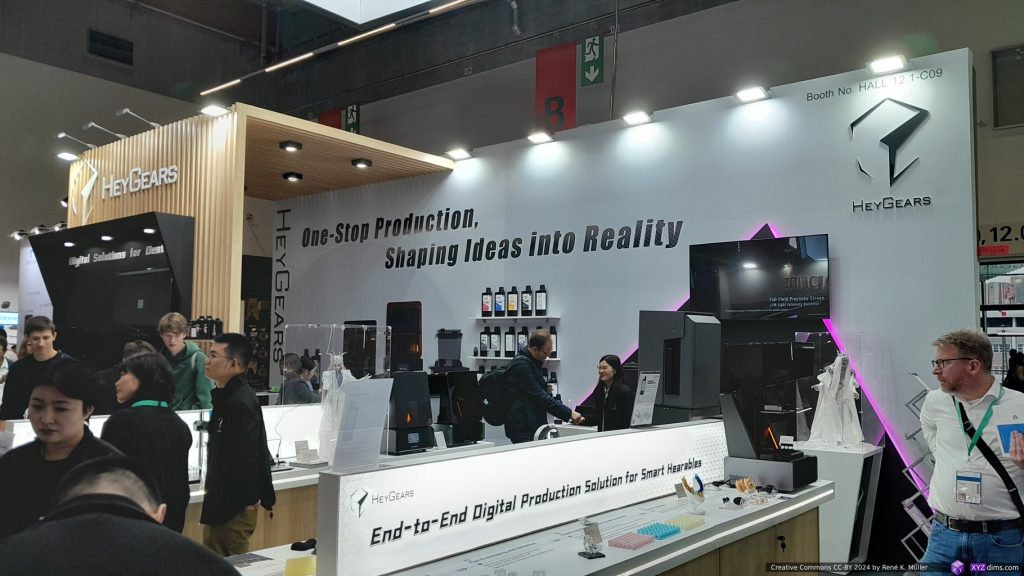

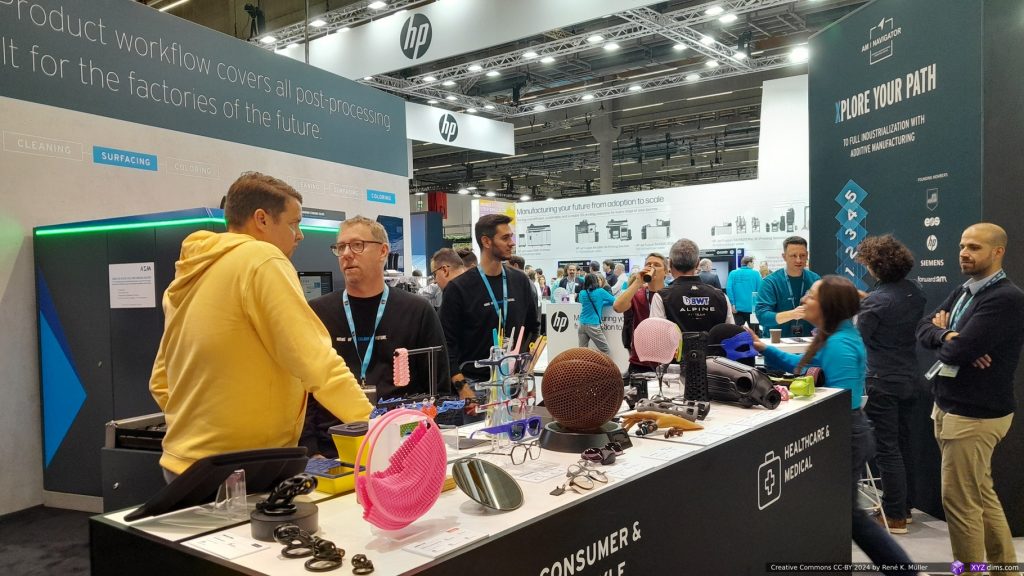
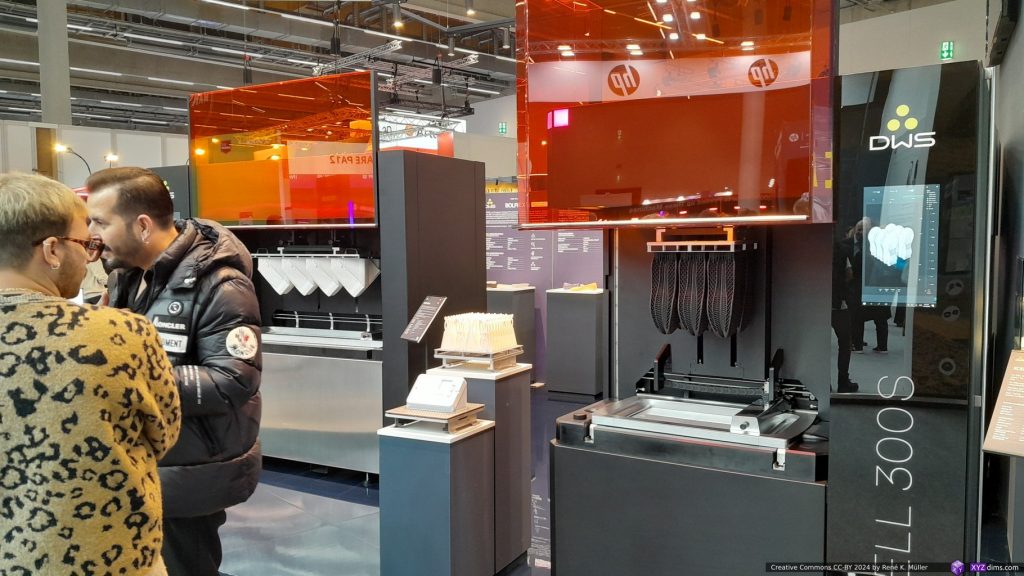
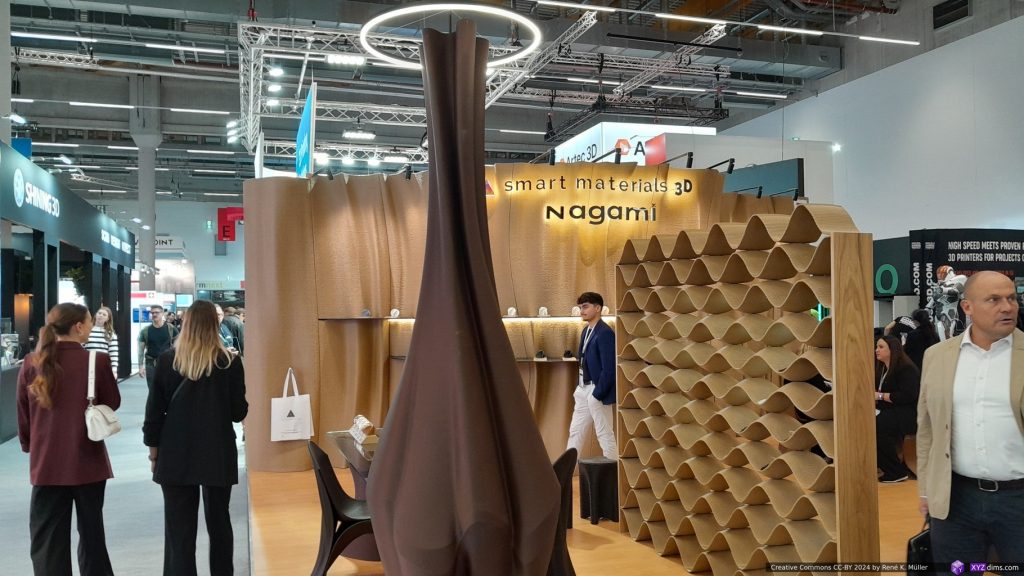
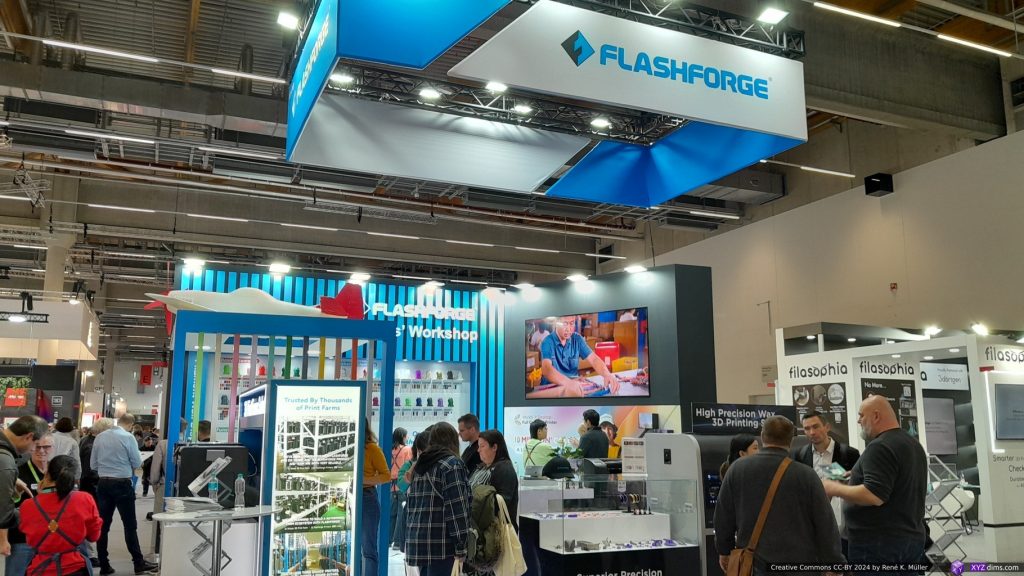
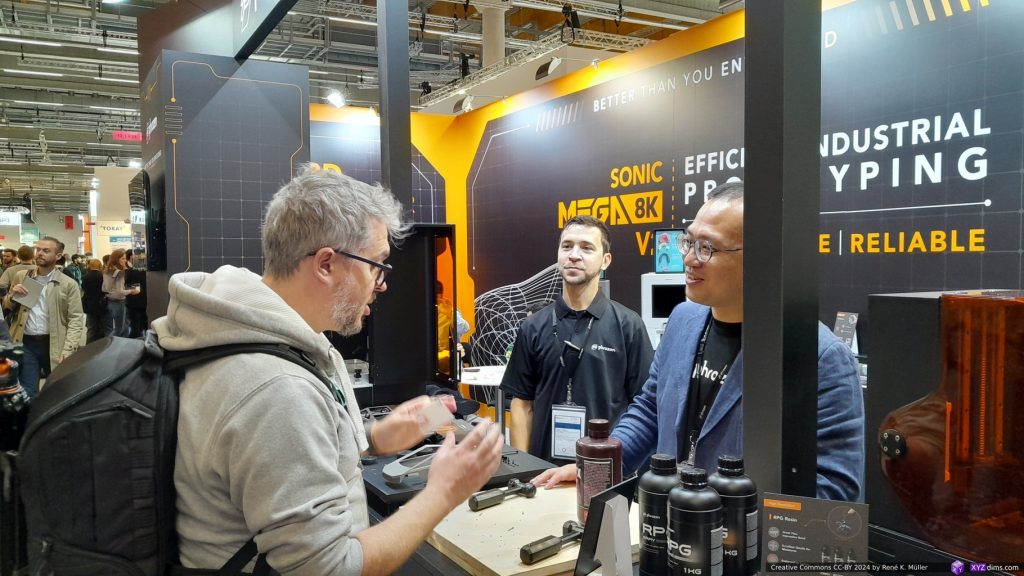
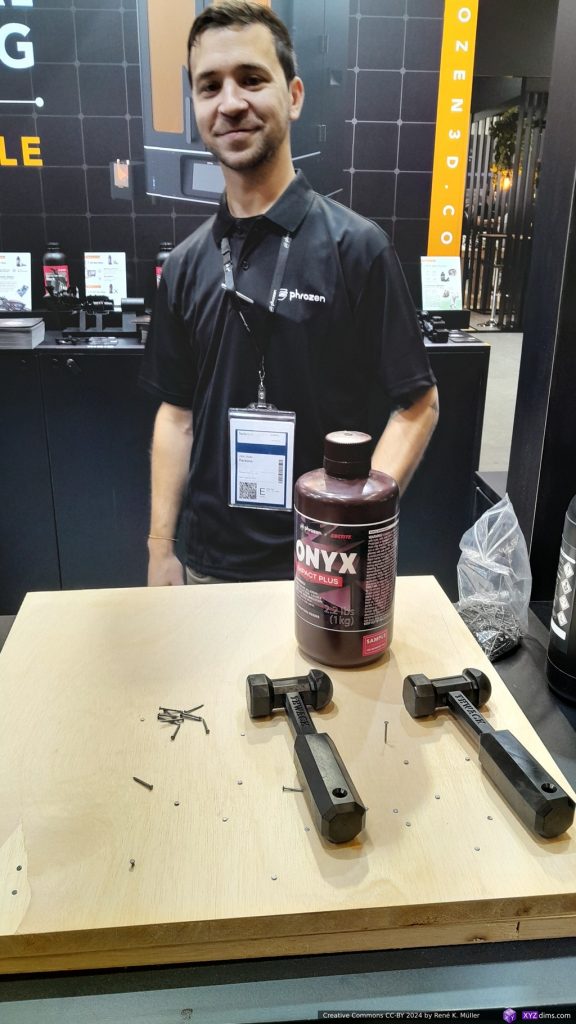
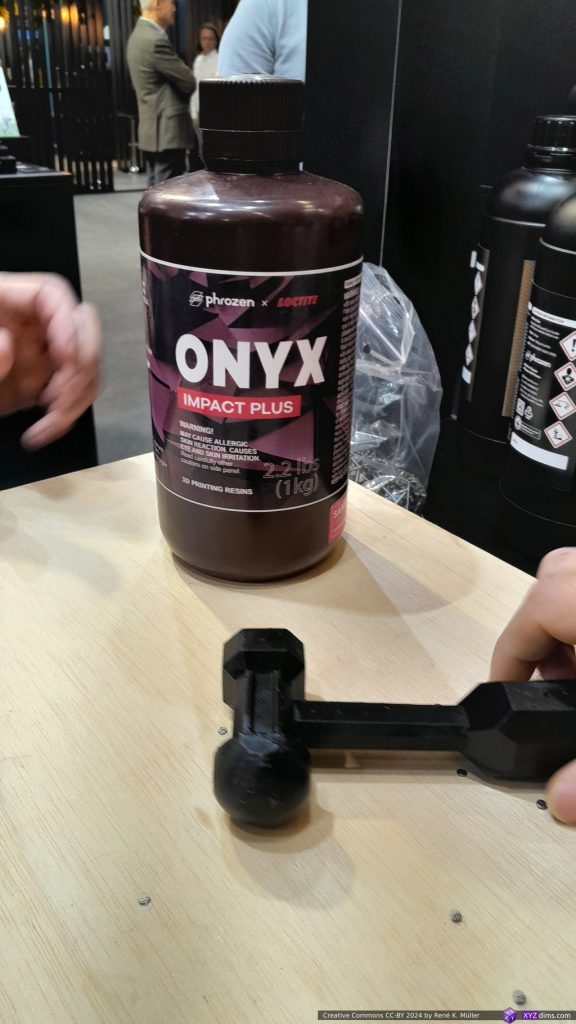
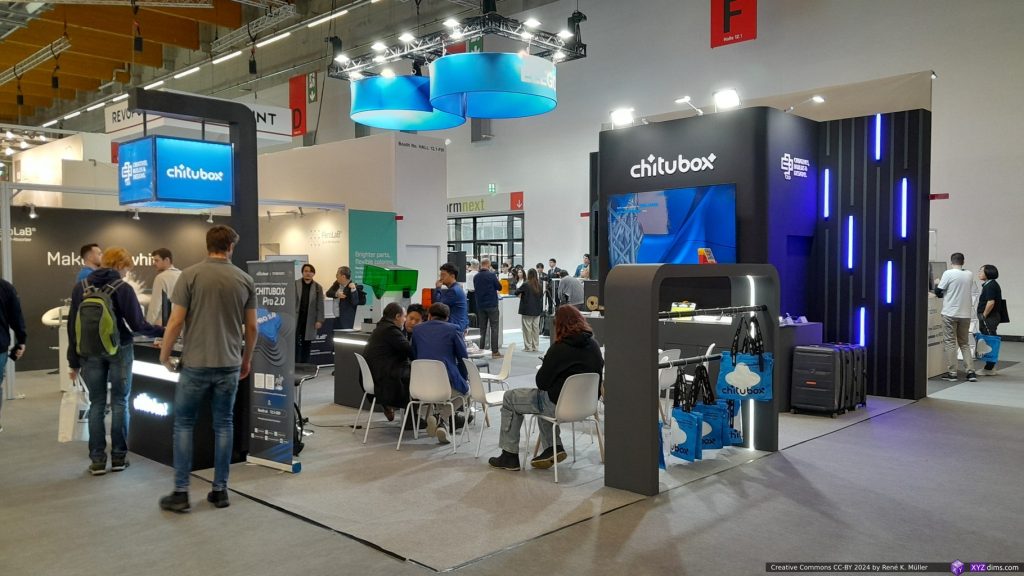
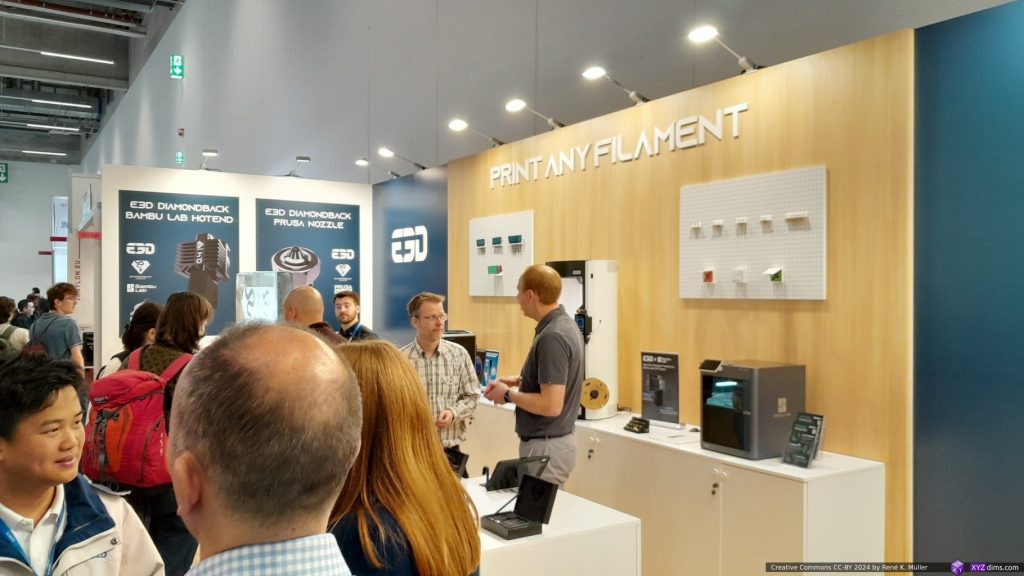
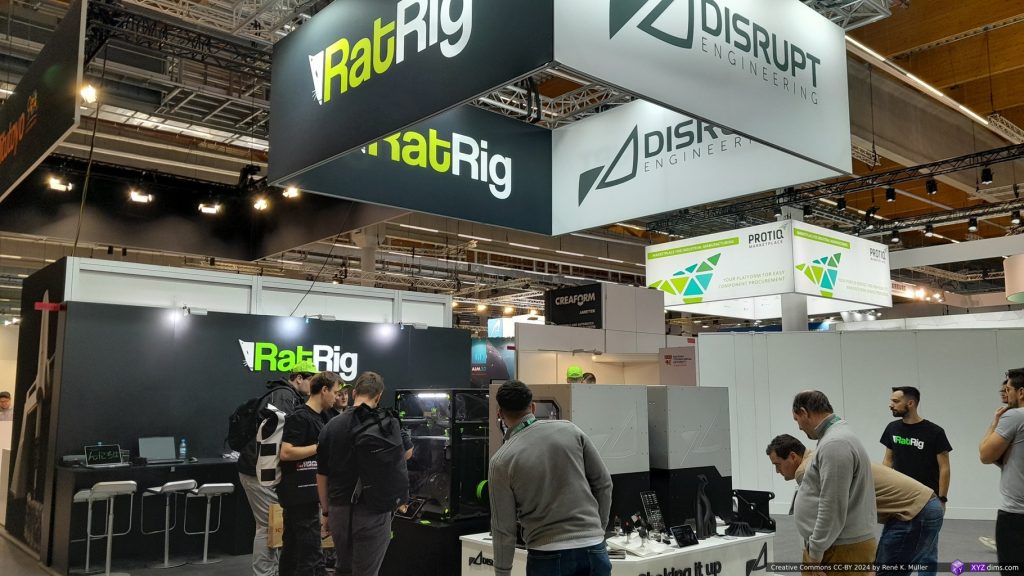
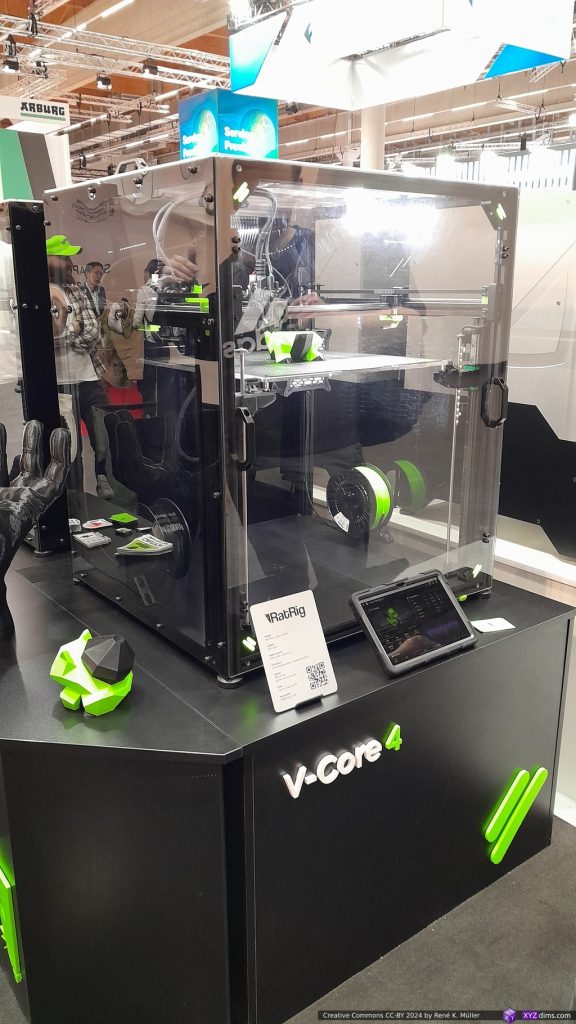
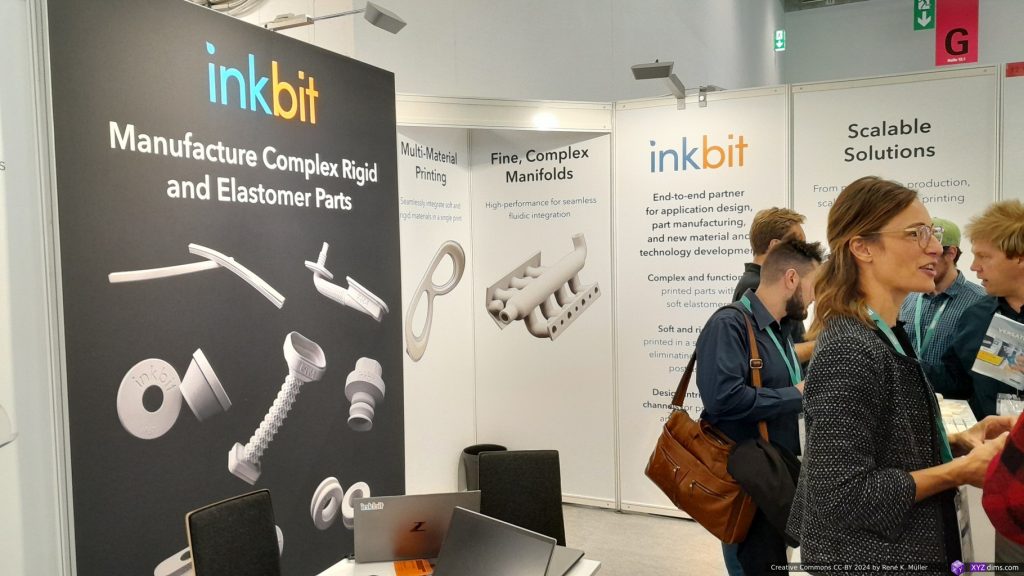
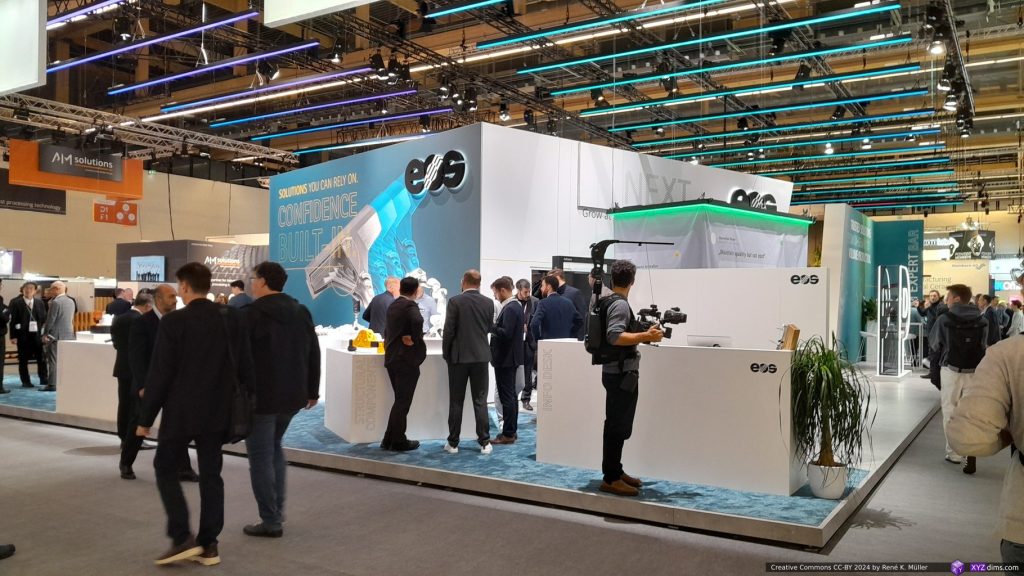
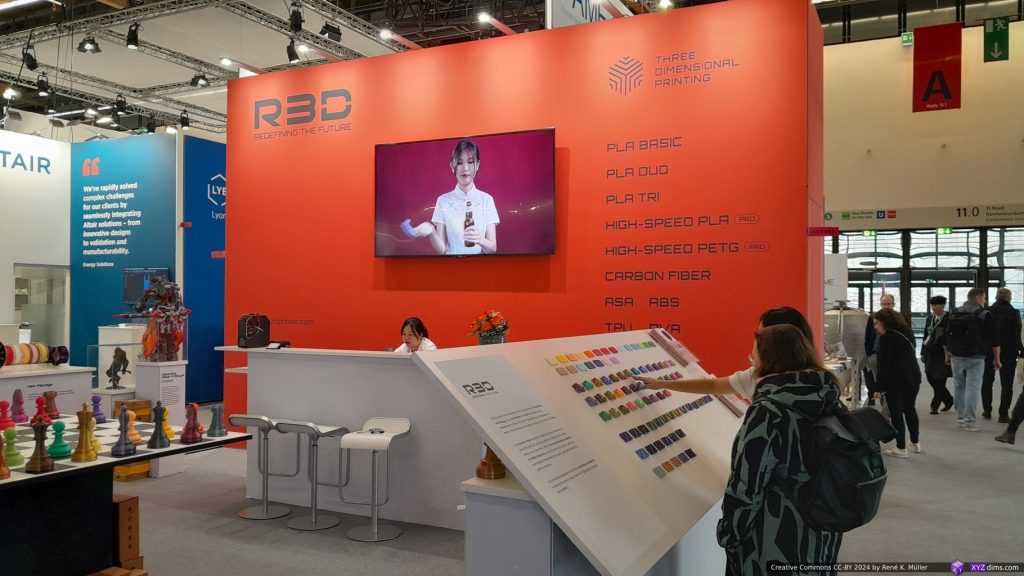
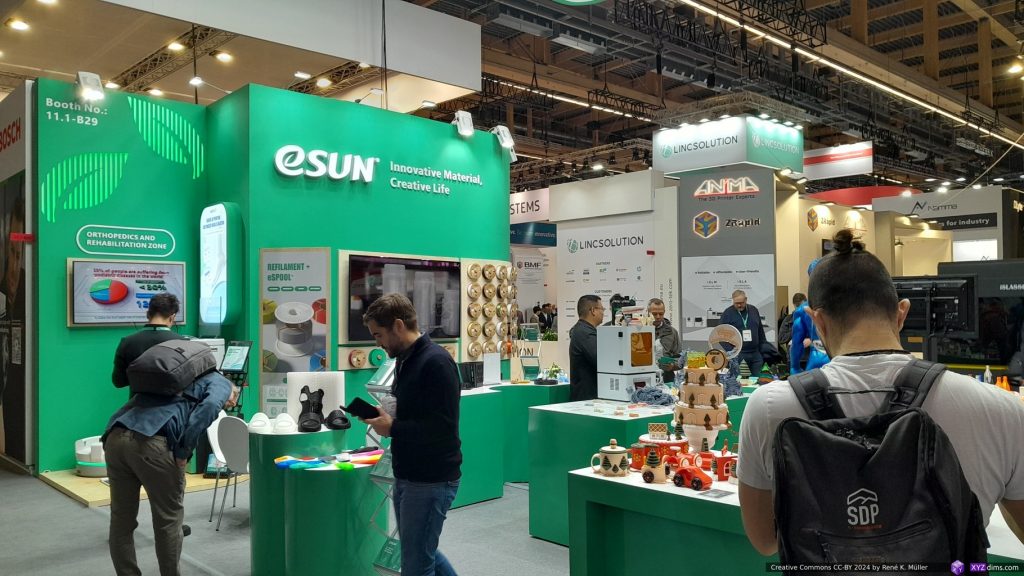
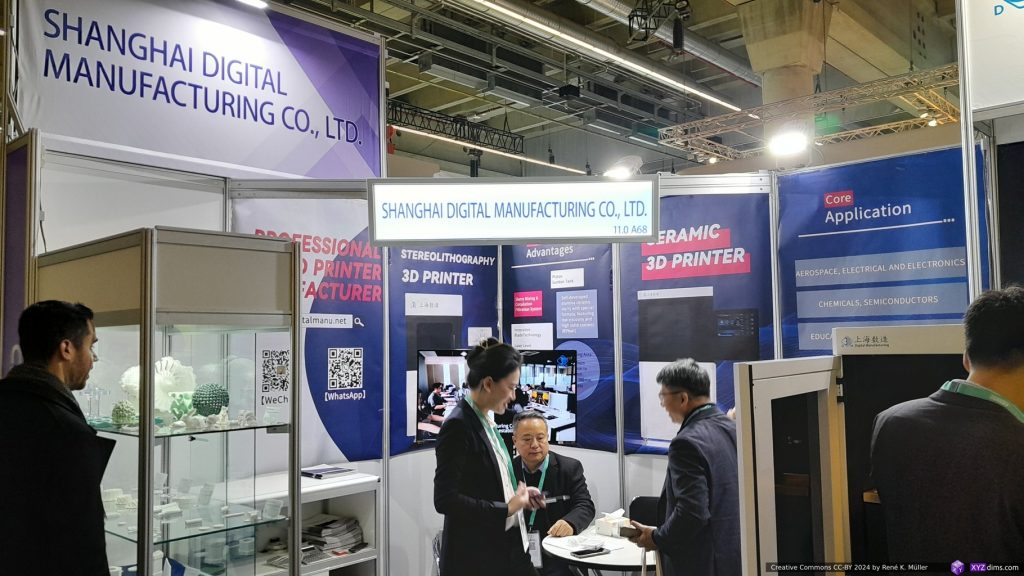
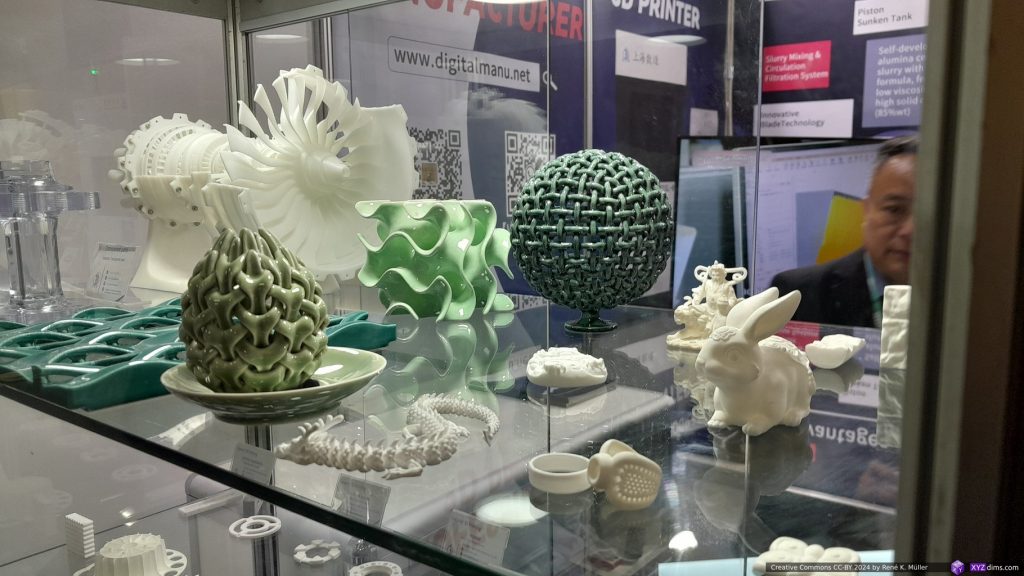
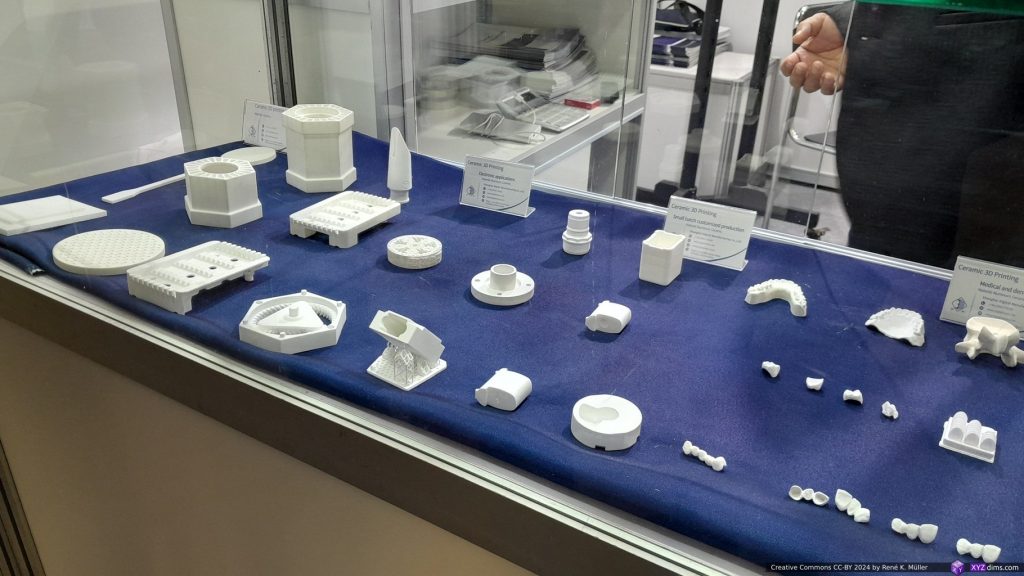
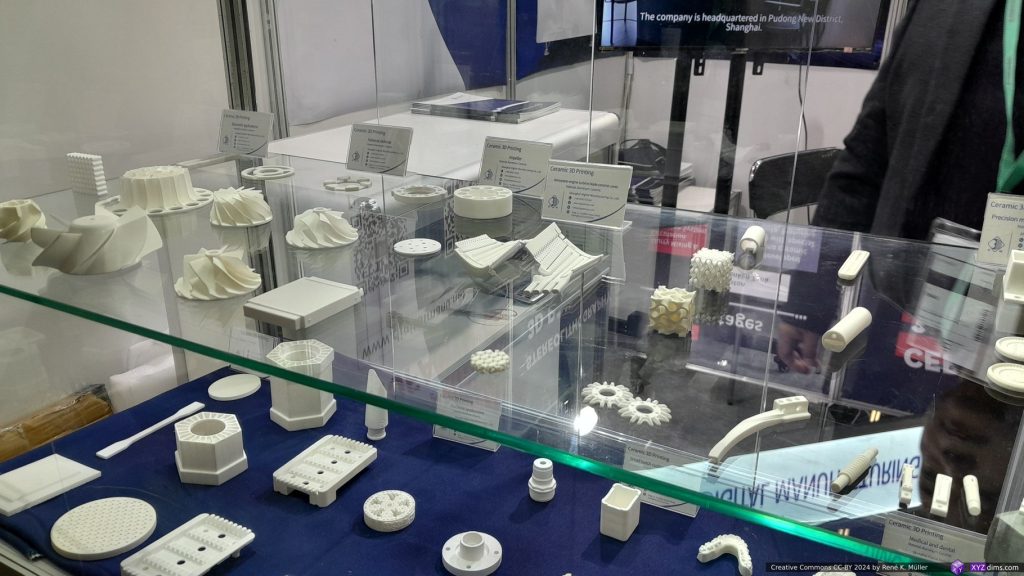
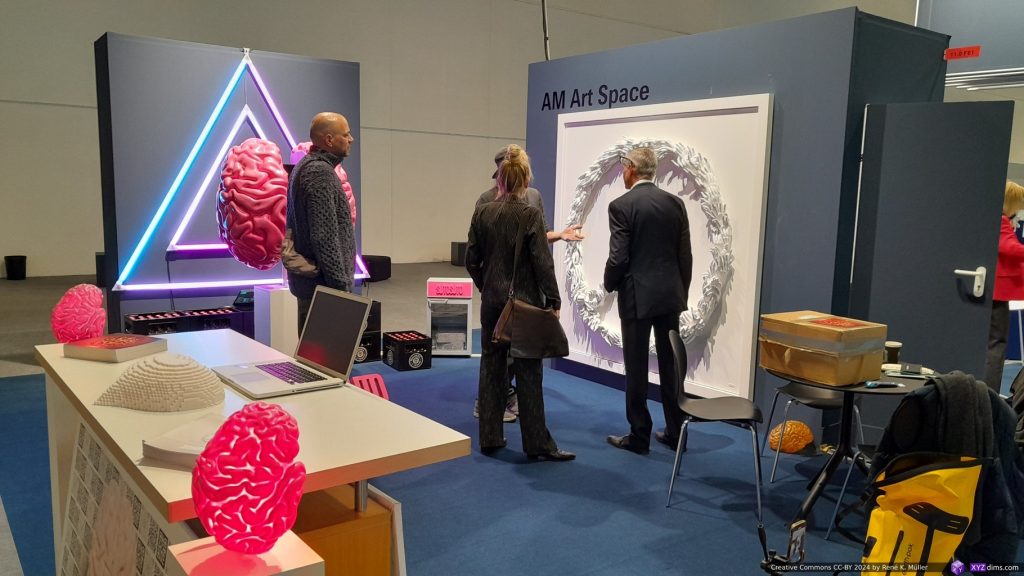
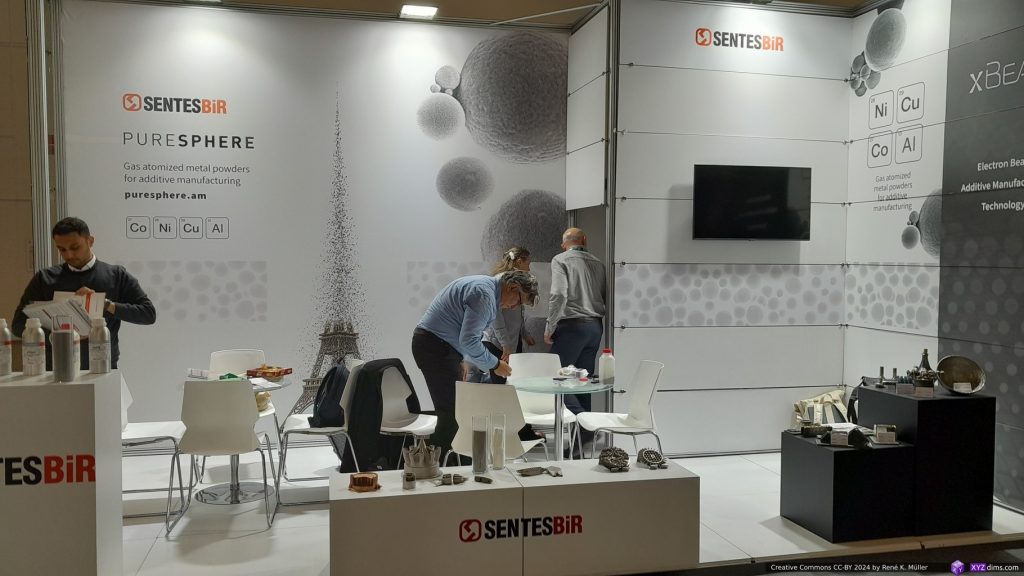
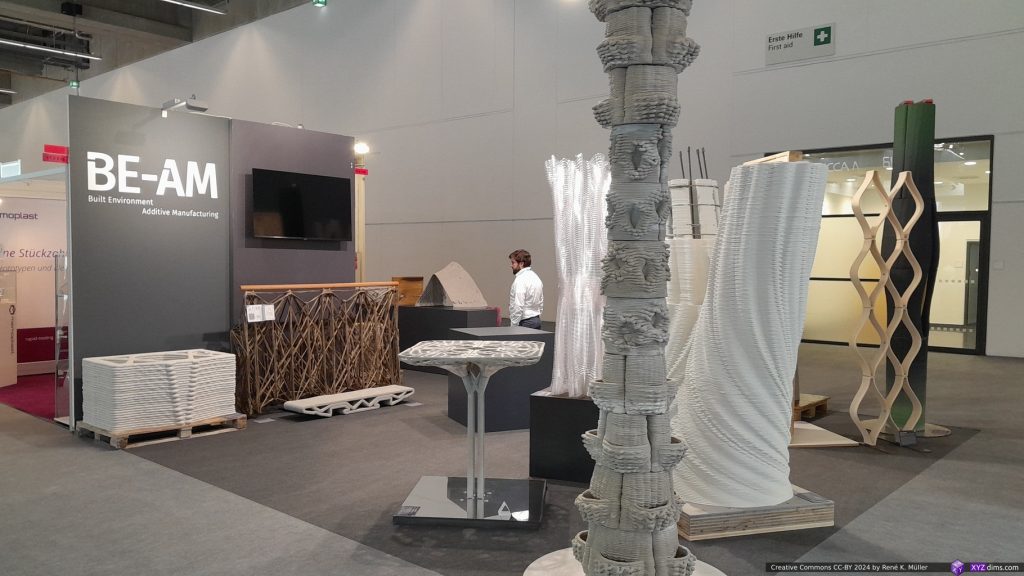
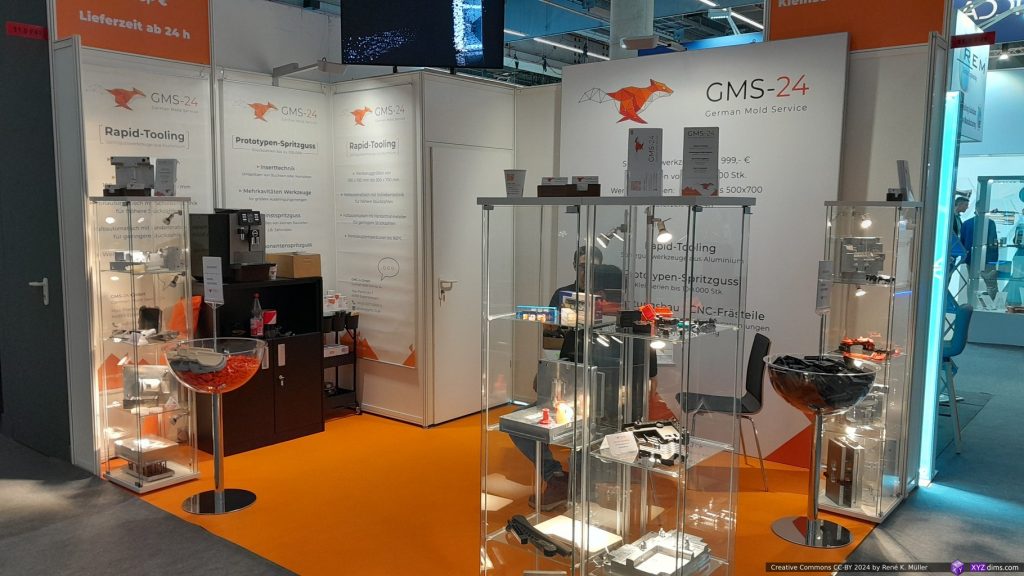

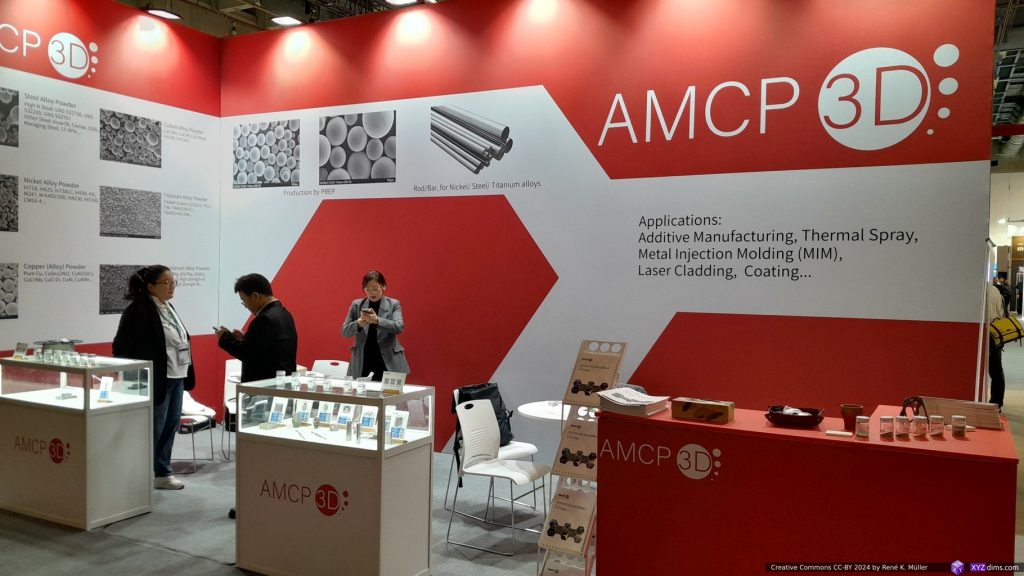
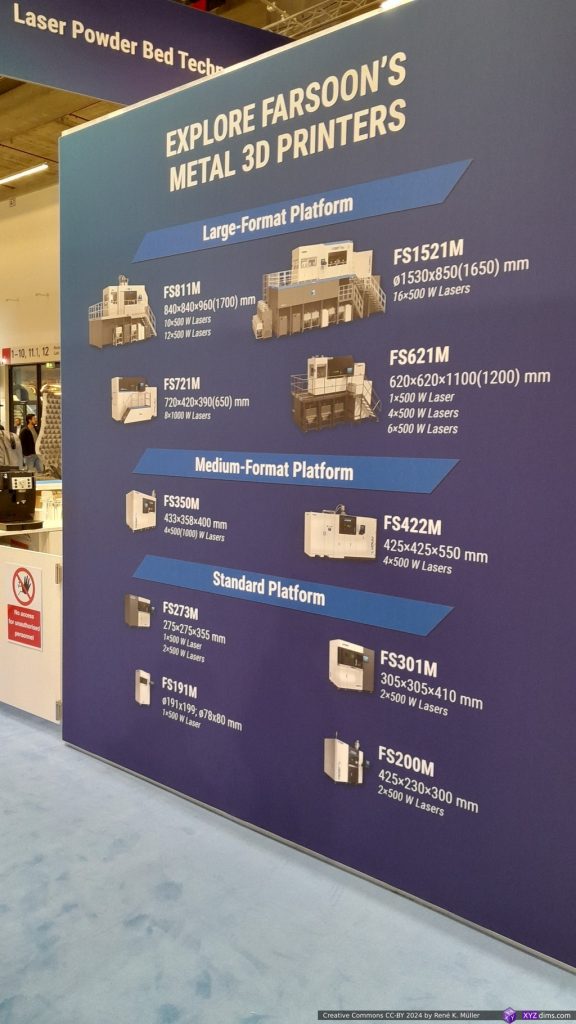
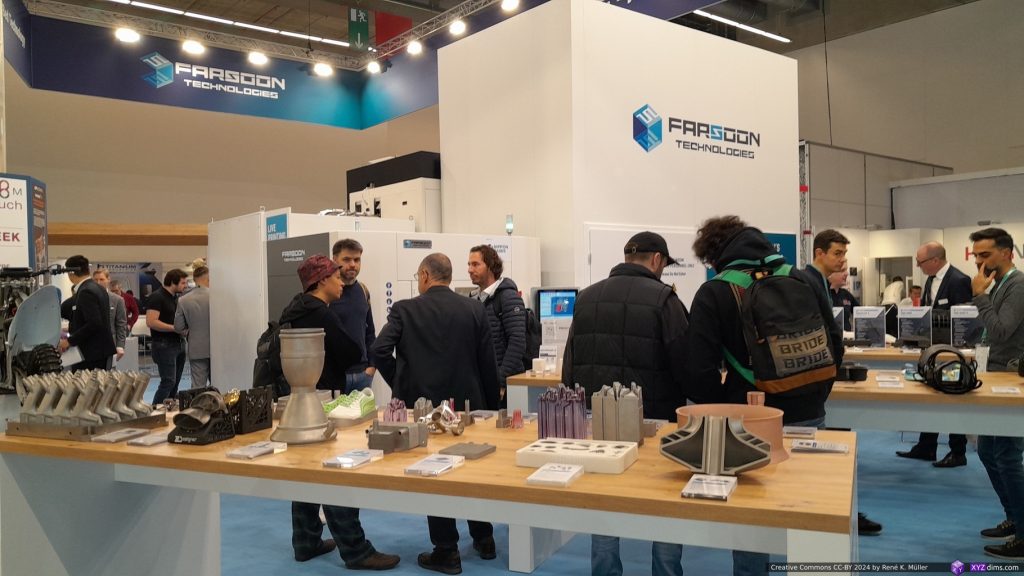
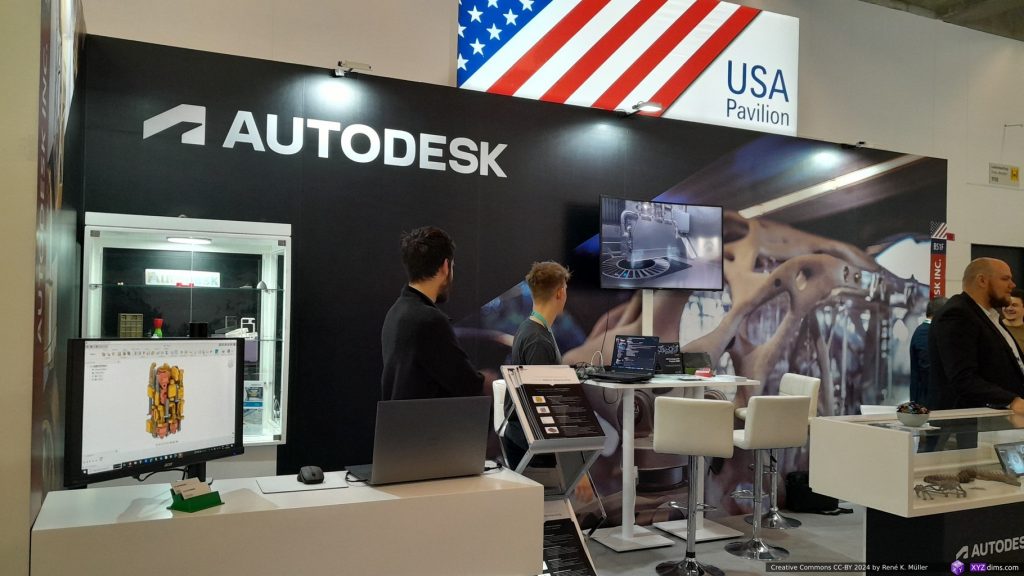
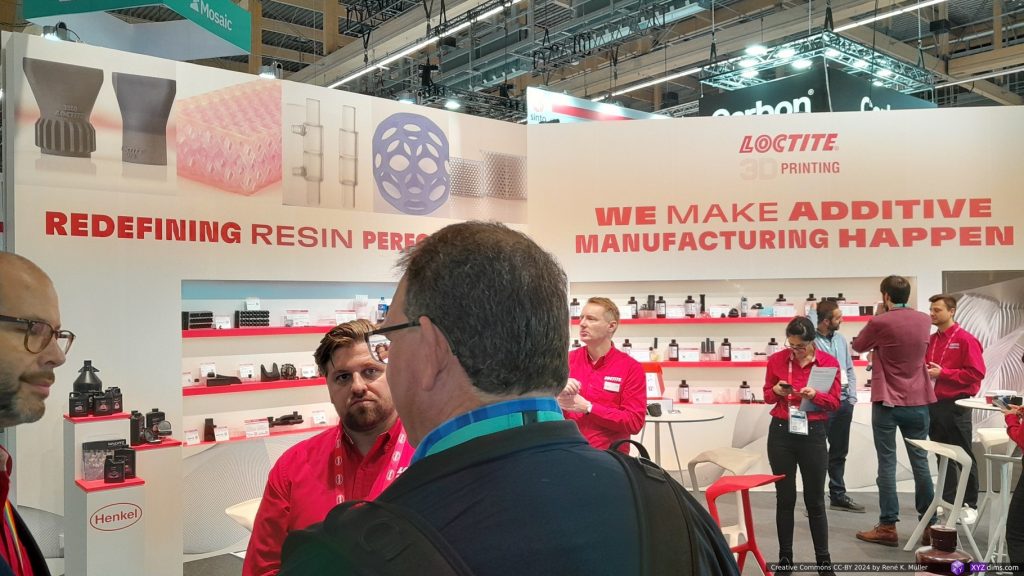
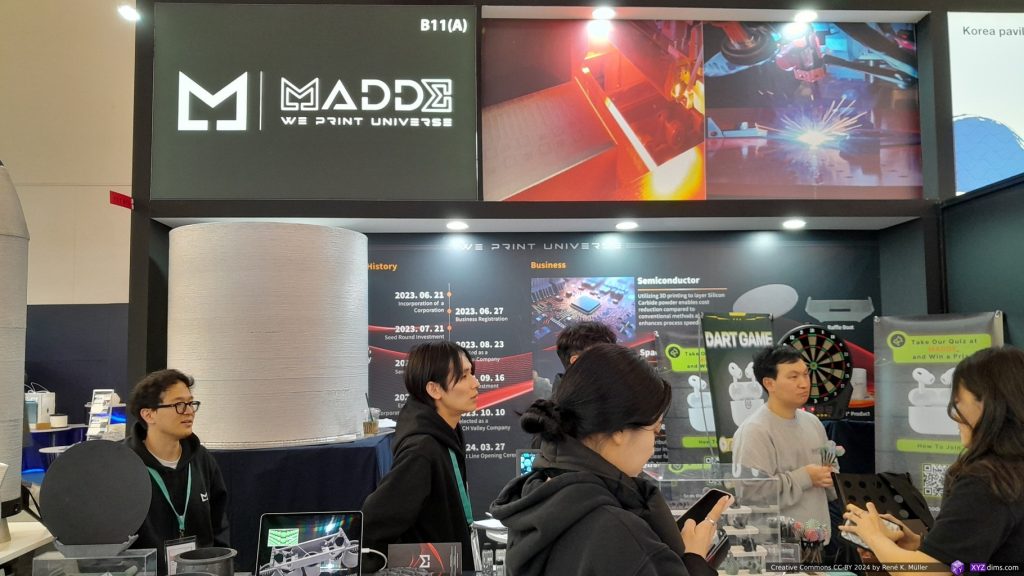
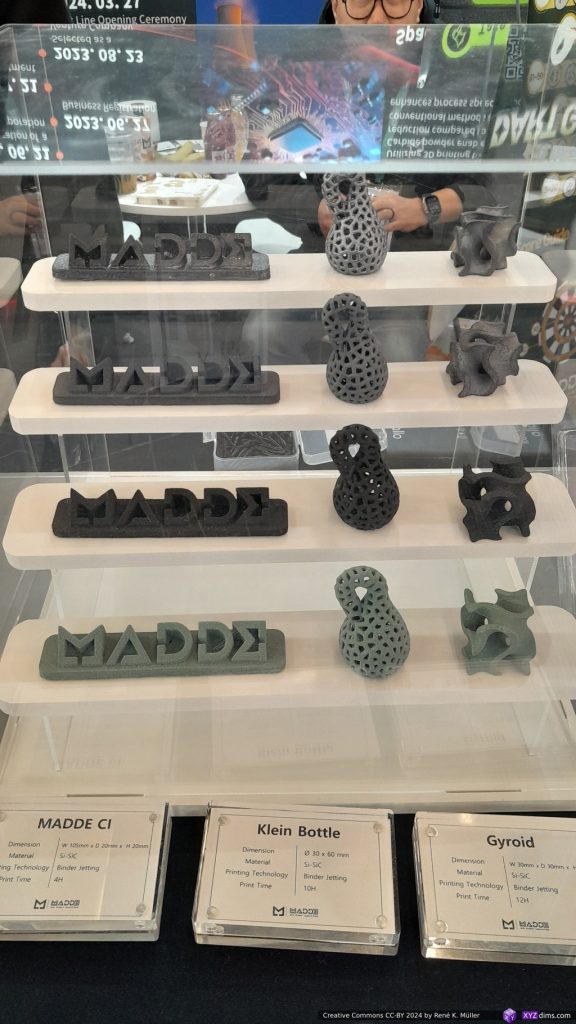
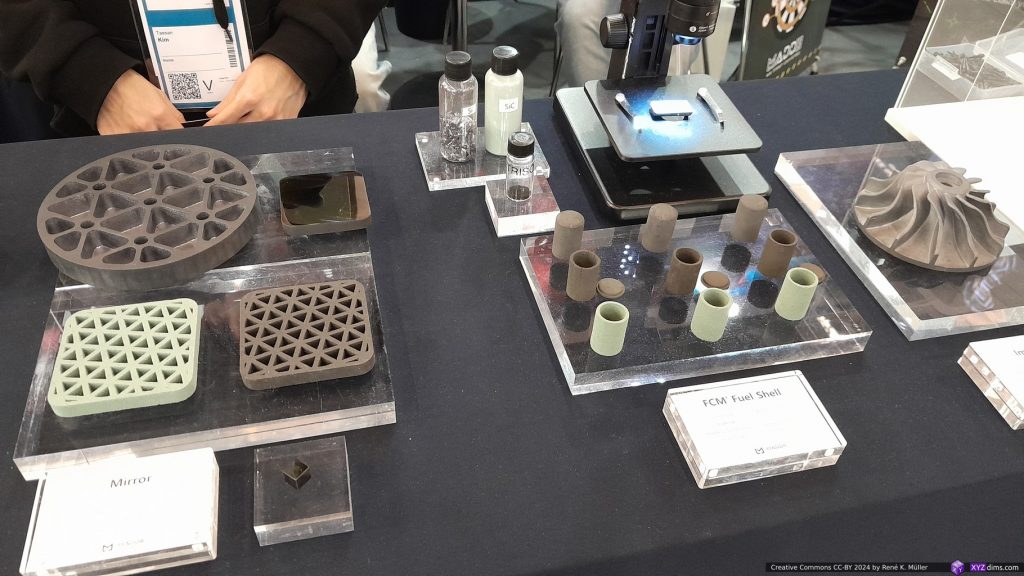
3D Printing Nerd
While roaming in the halls, I recognized a few YouTubers like Ross Graham (FauxHammer), Jon Schone (Proper Printing) and also Joel Telling (3D Printing Nerd):
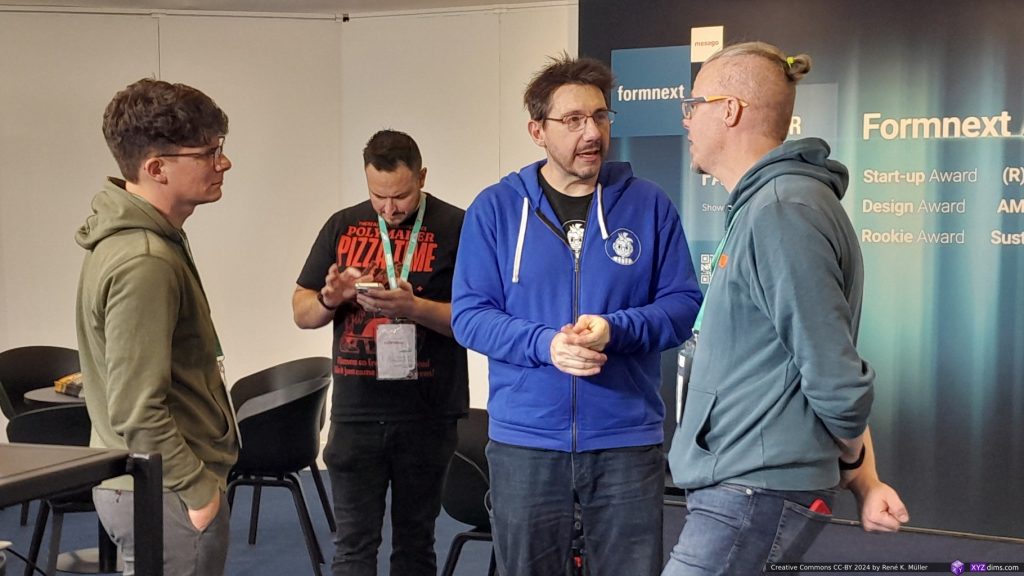
Here his marathon live-stream at Formnext 2024:
Among others were also Xolo with the Xolography light printers, Spherene with Daniel Bachmann, Josef Prusa showing the Prusa Core One, and Stratasys representative featuring SAF H350 able to process used powder with High-Energy Absorption Fluid (HAF) with Selective Absorption Fusion (SAF).
Tony Lock (Duet) & Jon Schone (Proper Printing)
As I was visiting the booth of OST (Eastern Switzerland University of Applied Sciences) & Spherene I met Jon Schone (Proper Printing) and Tony Lock (Duet3D) and we had a brief talk on multi-axis firmware & slicing and parallel printing as Jon showed in his video with a multi-gantry setup – I’m currently composing/writing on a blog-post about parallel/concurrent printing with multiple nozzles so I was keen to briefly exchange thoughts on this topic.
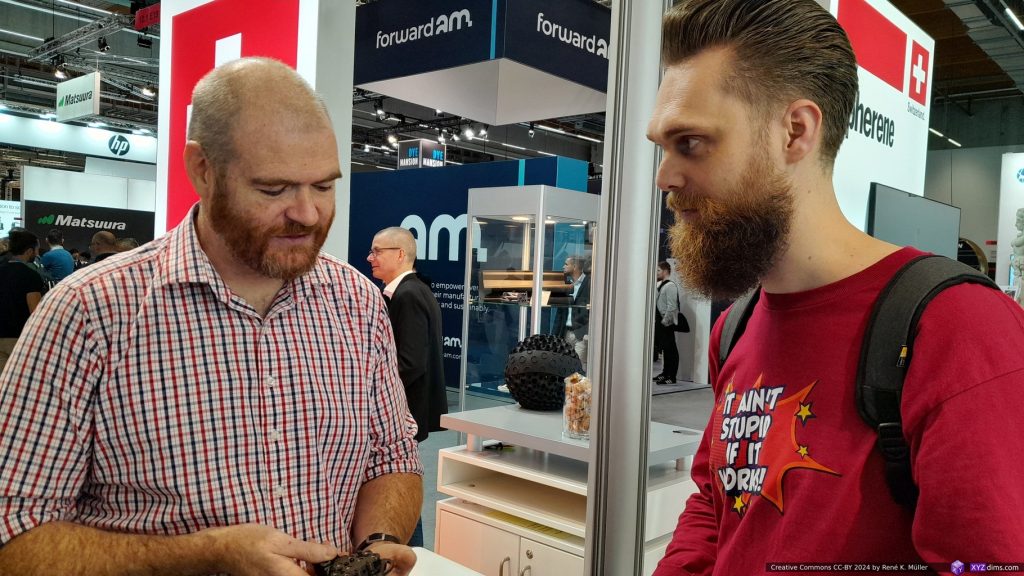
Reflection
Formnext is an overwhelming expo on all things on Additive Manufacturing, and this year less people and less exhibitors than last year. Also a few startups with big booths last year either had a small one (nTop, Inkbit, etc) or were no longer present. A couple of newcomers and startups, and some companies I have been following pushing their innovation further and exploring new applications, like Quantica.
I only stayed for 2 1/2 days (Tue-Thu) instead the full 4 days, as from last year I knew I wouldn’t be able to absorb more things with more time, there was only so much to take in. For me it was worth it, to reconnect with companies and individuals I know only online and via video calls.
The “3D Printing Hype” has peaked, the stock prices (state 2024/11/22) of Stratasys (8% or -92% of max), 3D Systems (8% or -92% of max), Desktop Metal (1.6% or -98.4% of max) or Nano Dimension (15% or -75% of max) have shown how much air and speculation was there, and now the sobering realism and use case are established. The same time MakerBot & Ultimaker merged, two exhausted 3D printer manufacturer without hardware innovation in the past years – yet Prusa, Creality, Elegoo, Anycubic still thrive on the pro- and consumer level with both FDM/FFF and MSLA resin printers, and BambuLab so successful that it caught Stratasys’s attention to sue them about patent infringements.
It’s clear to me, that Additive Manufacturing (AM) has its unique use-cases, whereas injection molds still dominate mass production due the high volume capacities and cost effective production. Additive Manufacturing may be a bland term (I like “3d printing” better), but there are still many possibilities to be explored, as Xolo or diverse university booths have shown – any kind of granular or liquid material is melted, extruded, jetted, cured or bound with an agent.
References
- Mesago: Formnext
- VoxelMatters: more Formnext 2024 news
- 3DPrint.com: Formnext
That’s it – see you perhaps in 2025 there.