Updates:
- 2021/05/02: adding overhang-inout with 5 segments, with conic inside- and outside-cone mode
- 2021/05/01: adding tilt sliced overhang segment variant as comparison
- 2021/04/29: video uploaded and blog-post published
- 2021/04/27: first successful tests with vertical nozzle (3-axis FDM printer)
Introduction
The past few months and weeks I focused on the non-planar slicing, and the first tests with sub-volume segmenting and thereby mixing planar and non-planar sliced G-code worked as simulation, and now in actual prints.
One of the benchmarks are 90° overhangs in different directions, and I printed with vertical nozzle on an ordinary 3-axis FDM printer, therefore I prepared the G-code with a new tool (in-development) which coordinates segmenting and planar/non-planar slicing of sub-volumes, and the conic sliced segment was sliced with 25° conic angle so it remains printable with the vertical nozzle unlike the simulation where a 4- or 5-axis FDM printer is required:
Gallery
Conic Sliced Overhang Segment
The simulation as reference:
and the actual print process with vertical nozzle on a low-cost 3-axis FDM printer:
starting z-planar building up fast z-planar switching to conic sliced “balcony” 2mm thick building the “balcony” 2mm thick extending further the “balcony” extending further the “balcony” finishing the “balcony” and switching to z-planar printing again finishing the piece finished circular underside of the overhang took a few attempts to arrive to something acceptable
Excerpt of the actual printing process with brief annotations:
Tilt Sliced Overhang Segment
Just for sake trying out, instead of conic sliced overhang segment, tilt sliced and 45° Z rotated to nicely extend to the maximum overhang position:
and the actual print of a slightly lower model but with the same features:
Comparing Tilted Sliced vs Conic Sliced Overhang Underside
Overhang In/Out: 2 Overhang Conic Segments
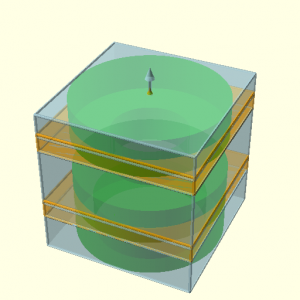
And revisiting the Overhang In/Out Model, which features ingoing and outgoing overhang, segmented into 5 sub-volumes:
- bottom: z-planar
- ingoing1) overhang: conic (inside-cone mode)
- middle: z-planar
- outgoing1) overhang: conic (outside-code mode)
- upper: z-planar
1) when dealing with conic slicing, the direction of overhang matters when deciding the mode of conic slicing, e.g. outside-cone or inside-cone.
and the actual print, a half of the model so the printing of inner overhang on the lower part of the model is visible:
z-planar and now switching to conic (inside-cone) slowly building up inner overhang with inside-cone segment building the inside-cone segment extending the inside-cone segment closing the inside-cone segment inner overhang finished back z-planar on top building up z-planar and switching to outside-cone for outgoing overhang slowly extending extending to actual overhang halved model profile solidifying the overhang overhang done, switching to z-planar again and finishing the piece finished piece finished piece
Conclusion
It took me a few days to tune the 3-axis FDM printer to print in acceptable quality of this Overhang Model No 5 and also Overhang In/Out Model. A strong part-cooler was mandatory, well adjusted print temperature and slow perimeter as those extrusions align horizontally without vertical support; and it worked: the main idea is to segment and limit the overhang part to ~2mm thickness – a quasi “balcony” – which still allows a classic vertical nozzle with part-cooler to print such, and then switch back to planar printing again.
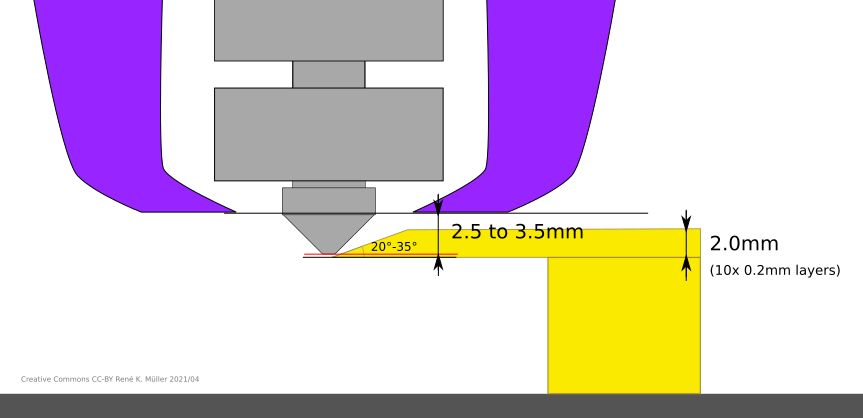
Detail settings: the conic overhang was sliced with Slicer4RTN with following settings slicer4rtn --slicer=cura-slicer --speed_wall=10 --speed_wall_0=10 --speed_wall_x=10 ...
and since the Z-axis motion is limited to 4mm/s (M6 threaded rod, 1 rotation => 1mm) the overall printing speed is slow enough to provide acceptable print quality.